Visual Management in Manufacturing and Logistics
There are likely many times you’ve encountered problems that arose from something being unclear. Communication is key, as the saying goes. That’s where visual management comes in.
Veryable is interested in this because we want manufacturing and logistics companies to succeed by implementing best practices. When you combine clearly defined processes and work standards with our on-demand labor marketplace, you can gain a strong competitive edge.
That’s why in this article, you’ll learn what visual management is and how it can benefit your operations. You’ll see examples of visual management in action and learn how you can implement it in your own facilities.
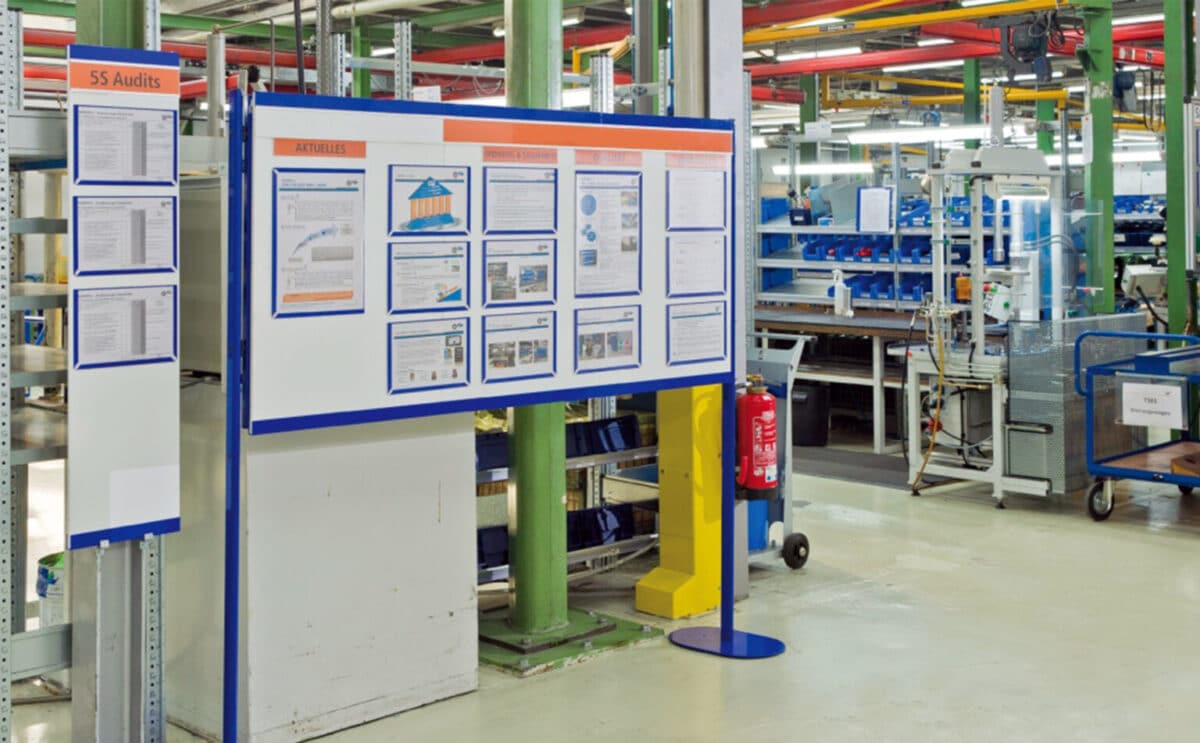
What is visual management?
Visual management is the display of information in the workplace to inform teams, enforce work standards, and highlight or prevent problems. There are many ways to use visual management, and this concept is deeply embedded in Lean thinking.
Functions of visual management
Share information
The most obvious function of visual management is to share information. This is done through dashboards, markings in the work environment, lights, and the like.
Develop work standards
By tracking and displaying information about the work being done, visual management enables the development of work standards. For example, with a clearly visible record of what’s being accomplished, you can set a standard pace. Likewise, if you record the steps of a process in a visual medium, you are creating a work standard.
Share work standards
After work standards have been developed, visual management is used to display these work standards in the appropriate context so that there is no question as to what the standards are. If you record the steps of a process and then create visual cues in the physical environment to guide the work, this makes the work standard clear to anyone who approaches the workstation.
Highlight problems
Visual management can be used to quickly signal when something has gone wrong. Automated systems for this can be especially useful for supervisors and workers alike, because they allow individuals to focus on other tasks unless a problem is highlighted. Then a signal goes out as soon as an issue is identified, and they can quickly solve it before getting back to their original task.
Solve problems
Visual management can be used to solve problems as well. If there is a location or process in a facility where there is often confusion, proper visual management will solve this problem. Likewise, if there is a machine that operators often misuse, visual management could prevent a problem in the first place by making it clear how to properly use the machine.
Why should you use visual management?
There are many workplace benefits and tangible business outcomes which can result from the implementation of visual management.
Benefits of visual management
Transparent processes
When you implement visual management, it becomes easier for everyone to see what is happening in a process. A well-designed process makes the work easy to follow for the operator and supervisors.
Accountability and consistency
Due to the more transparent processes, holding workers accountable is easier with visual management. When anyone can easily see what’s happening in a process, bad work has fewer places to hide. This results in clear expectations and improved consistency.
Work facilitation
Visual management facilitates work by removing ambiguity to help operators and supervisors focus on the value-add tasks they are assigned. Visual management can also remove obstacles to work by ensuring that operators attempting to perform two different tasks do not interfere with each other. Simply put, it helps workers and supervisors “stay in their lane” so that the flow of work is smooth.
Reduced need for training
Visual management can enable real-time training by making the work intuitive. With visual cues and clear guidance, most tasks become straightforward enough that an operator with minimal experience could learn them in one day.
Business outcomes of visual management
Improved process efficiency
Clear visual cues and process design using visual management can improve the efficiency of processes. Operators who face less ambiguity in their work can work faster. Processes that are designed with visual management ideas like poka-yoke in mind can eliminate ambiguity and reduce wasted time on figuring out what’s next.
Reduced waste
Waste reduction (a major component of the Lean methodology) is a primary outcome of visual management. Clear visual signals help supervisors identify and eliminate waste. Process design using visual management helps operators avoid errors and work more efficiently. There is great potential for waste reduction using visual management tools, which we will explore more in the sections below.
Safer workflows
With less room for error and more clear instruction for operators, you can eliminate many safety issues through visual management. For example, if a forklift should only drive in certain areas, clear markings on the floor will help the forklift driver stay where they should be and take extra caution in areas near other workers.
Optimized inventory
When you apply visual management to inventory, you can more easily see when a stock is running low, or when you already have plenty of something. This will prevent overstock, stockouts, and extra work among operators searching for inventory.
How to implement visual management?
Types of visual management
Factory layout
Believe it or not, the layout of your factory is a type of visual management. The location of work areas in relation to each other communicates something to workers and supervisors. The flow of work should be prioritized in your layout, and you should focus on ensuring there is visibility of the work wherever possible. You want workers to be able to navigate the building and flow with their work in an efficient way, and you want supervisors to be able to keep an eye on things easily.
Tools and parts
A popular methodology called 5S is a visual management tool focused on organizing workspaces and continually keeping the workplace tidy. One emphasis of 5S is on creating a clearly defined place for every tool and part, which eliminates time wasted searching for tools. This could be accomplished with a shadow board, for example.
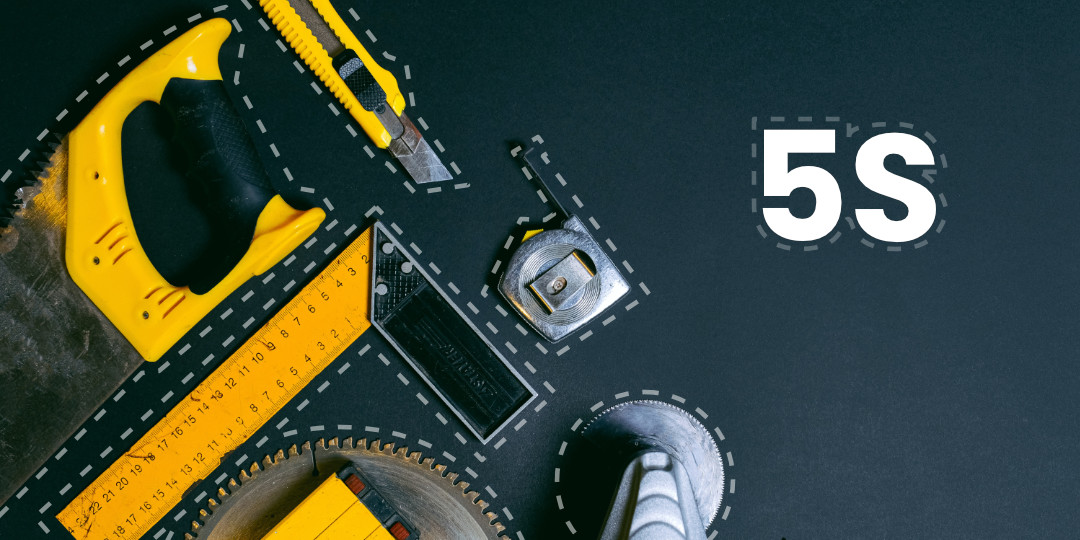
Markings
Markings on surfaces such as floors, racks, and walls are powerful tools for communicating information in the context where it’s needed. Examples include lanes for forklifts, directions for pickers and stockers in the inventory area, and clear labels on machines.
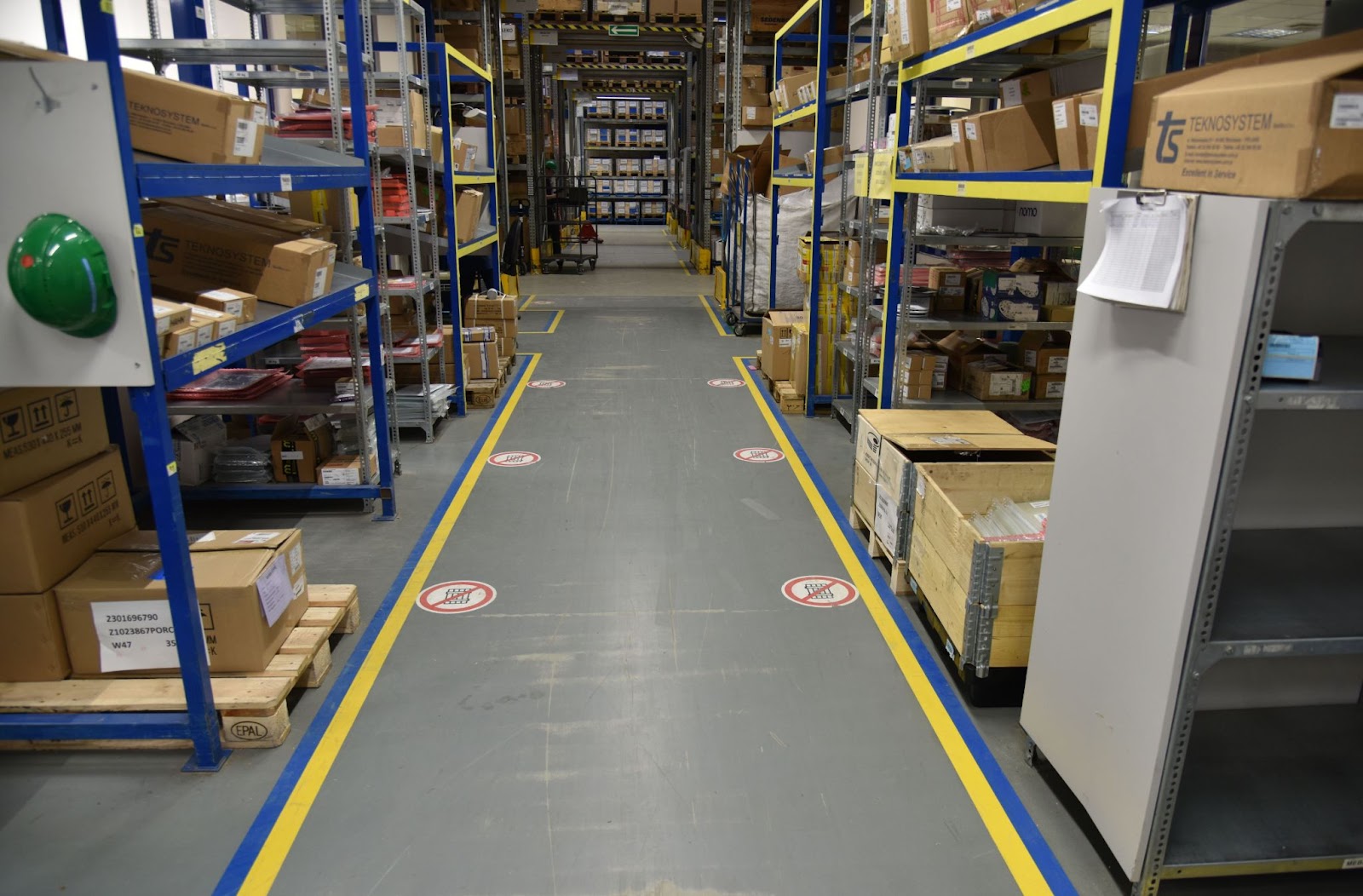
Data displays
Digital data displays on the shop floor showing key metrics in real-time and signaling problems on the line are another example of visual management. These displays typically include information such as an efficiency metric so you can see at a glance if a line is on pace, or a status section to show any abnormalities on the line. They are designed to be visible from far away and are often color-coded for at-a-glance understanding of the information they present.
Examples of visual management tools
Guidelines for visual management
- Be consistent if you have multiple instances of the same visual management tool
- Be clear in your presentation of information
- Make key information visible from far away (40ft)
- Use green for good (hit/exceed target) and red for bad (miss target)
- Show key metrics (people, quality, schedule, cost, 5S)
- Display information in the right location (the info presented should be user-specific)
Who should be responsible for visual management?
Management should implement the tools and receive reports from supervisors on their efficacy. Supervisors should be primarily responsible for enforcing the use of visual management tools, and they should maintain the tools. Employees should give input and be responsible for adhering to guidelines surrounding input into any interactive visual management systems.
Your management team and supervisors should work together to determine what areas would benefit from visual management.
Before implementing the visual management tools your leadership team identifies, your supervisors should meet with the shop floor. This meeting is for workers to understand the purpose of the tools and have an opportunity to provide insights into their processes and give input on how the tools should be deployed.
What’s next after visual management?
When you’re ready to move further in your continuous improvement journey, there are many more tools in the Lean methodology toolbox to help you succeed.
You can find more guides and resources like this one on our Lean Center of Excellence Homepage.
Veryable can help you take action on opportunities highlighted with visual management
Visual management helps you see performance to a standard, reason for a miss, and the opportunity to take corrective action to keep that from happening again. Labor is one of the most critical components of an operation, and creating a Just In Time component to your workforce will increase the speed and agility of your operations. Here are two tools that can help you transform your operations, drive waste out, and help make your operations more competitive.
Veryable's On-Demand Labor Marketplace
Labor will directly or indirectly touch every aspect of your operational performance. It is also one of the largest expenses on your P&L. Ignoring opportunity or being comfortable doing things the way they've always been done makes it just that much harder to find net improvement elsewhere. Leveraging Veryable’s On-Demand Labor Marketplace to build a flexible extension of your full-time workforce will allow your team to precisely match labor capacity to demand on a daily basis. Adopting this approach gives your operations leaders the resources they need to deliver the maximum return for the business and the most value for the customer.
Veryable's Workforce Management Tool
Veryable’s Workforce Management Tool ties together multiple systems (ERP, WMS, MES, HRIS, etc.) to use real-time data to automate the labor planning process and guide your leadership in making better critical decisions. This eliminates guessing, protects against costly forecasting inaccuracies, and enables performance-based decision making without the burden of manual spreadsheet updates or back-of-the-napkin estimating. This tool can operate as a stand alone platform for your full time employees, or you can access Veryable's on-demand marketplace from within this tool to fill any gaps in your operation on short notice. The best part is, you'll be able to view real-time performance data in just clicks for both full time employees as well as Veryable Operators.
Together these systems truly optimize every labor dollar spent across your footprint. This enables better visibility to translate best practices, and can act as a roadmap for continuous improvement.
To learn more, visit our homepage for Continuous Improvement, Operational Excellence, and Lean Professionals.
Previous Posts
The Labor Crisis No One’s Talking About: Wasted Skill, Not Missing People
The Future of Manufacturing and Logistics
Create a free business profile today to explore our platform.
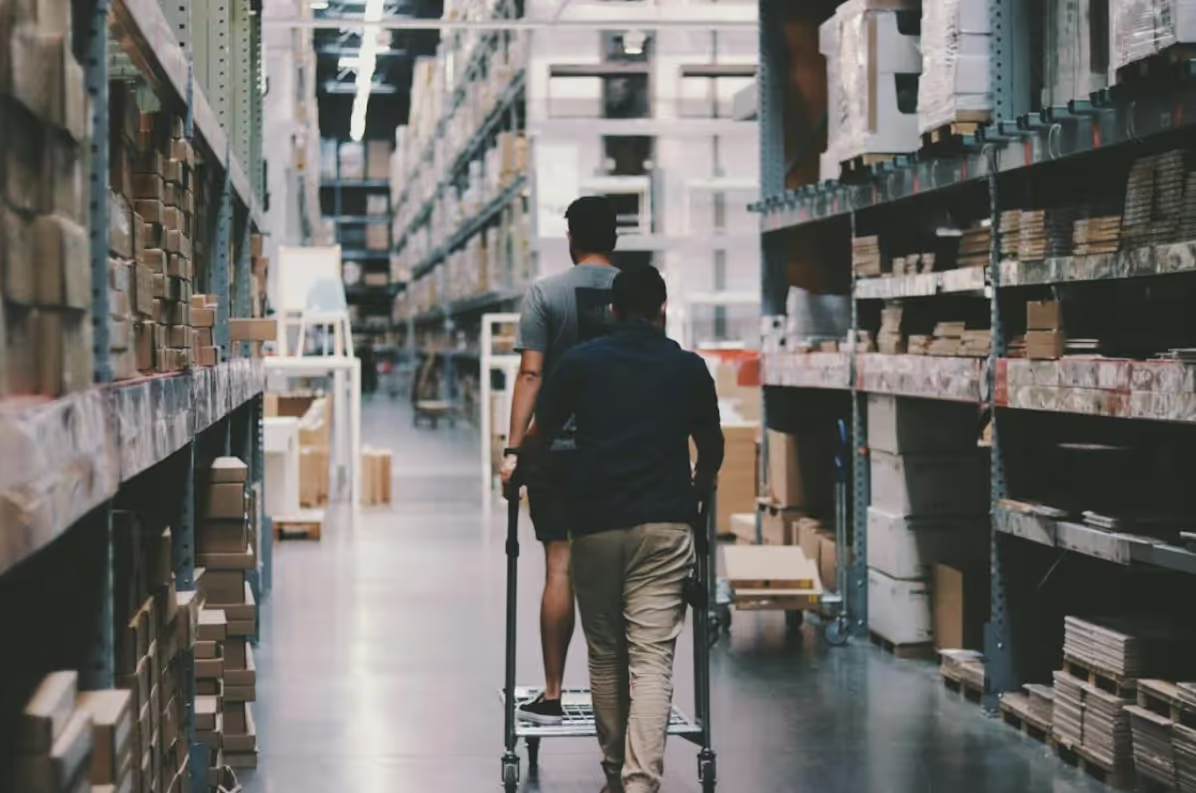