The Labor Crisis No One’s Talking About: Wasted Skill, Not Missing People
In the heart of American manufacturing, a silent crisis festers—not a scarcity of machines or materials, but a squandering of human skill. Skilled operators, the artisans of the factory floor, are too often tethered to tasks that dull their expertise, while the industry laments a labor shortage projected to leave 1.9 million jobs unfilled by 2033, costing the economy $1 trillion by 2030 (Deloitte). CNC machinists, welders, and assembly technicians—masters of precision and quality—are frequently tasked with moving pallets, setting up equipment, or performing basic checks, roles that demand none of their hard-earned craft. This misallocation isn’t just inefficiency; it’s a betrayal of potential.
The true labor shortage isn’t in bodies—it’s in the vision to deploy skilled labor effectively.
Compounding this is labor hoarding, a fear-driven habit where manufacturers cling to excess workers, anxious about losing talent to rivals or facing sudden demand spikes. Nearly 90% of small businesses, including manufacturers, engaged in this practice. This creates a paradox: too many workers idling, too few deployed effectively, all while the industry grapples with a perceived scarcity.
Hoarding labor is like clutching sand—it slips through your fingers, leaving only waste.
Yet, amidst this challenge lies a transformative opportunity. Veryable’s on-demand labor platform offers a way forward, providing mid to low-skilled workers for routine tasks, freeing skilled operators to become force multipliers. This model doesn’t just fill gaps; it redefines how manufacturing values its people. This article explores the twin culprits of underutilization and labor hoarding, unpacking their role in manufacturing’s labor crisis.
The Underutilization Crisis
The numbers are stark: by 2033, U.S. manufacturing could face a shortage of 1.9 million workers, with 3.8 million new jobs needed over the next decade (NAM). This isn’t just about hiring; it’s about using the workforce we have wisely. A 2024 NAM survey found that 60% of manufacturers see attracting and retaining talent as their top challenge. The economic toll is immense: the skills gap could cost $1 trillion by 2030, with 2.1 million jobs potentially unfilled. Yet, the heart of this crisis lies in underutilization. Skilled operators—those who run complex machinery, weld with precision, or ensure quality—are often assigned low-skill tasks like material handling or basic quality checks, reducing their impact and fueling the labor shortage perception.
This misallocation has tangible consequences. Approximately 20.6% of U.S. manufacturing plants operate below full capacity due to labor or skill shortages, as reported in 2025 (SCMR Article). A CNC machinist moving pallets instead of programming tools or a welder sorting inventory rather than crafting seams wastes not just time but expertise. This leads to production delays, increased overtime costs, and missed opportunities, with 45% of executives turning down business due to labor constraints, costing billions (Deloitte Insights). The inefficiency is systemic: when skilled operators are diverted, throughput and quality suffer, amplifying the labor shortage.
Unintended Effects of Squandered Skills
The labor shortage isn’t just a gap in workers—it’s a gap in how we honor their craft. Underutilization also erodes morale. Skilled operators, trained through years of practice, feel undervalued when tasked with menial duties. This disengagement drives turnover, with the Bureau of Labor Statistics noting persistent quit rates in manufacturing through 2024 (BLS Data). A 2023 PwC survey found 25% of workers considering job changes within a year, seeking roles that match their skills. Over 80% of manufacturing professionals report turnover disrupts production (PRWeb Report).
The broader impact is a weakened competitive edge. Manufacturing thrives on precision and innovation, yet when skilled operators are sidelined, the industry’s ability to innovate diminishes. The U.S. Chamber of Commerce notes labor shortages affect nearly every state, a national challenge. Replacing a skilled operator costs $10,000 to $40,000, with 56% of manufacturers facing significant financial impacts from turnover.
The Trap of Labor Hoarding
Labor hoarding—retaining excess workers to guard against talent loss or demand spikes—is a pervasive issue in manufacturing. Driven by fears of competitors poaching skilled operators or sudden market surges, this practice is seen as a necessary evil. A 2024 NIST blog post argues that hoarding is critical due to the scarcity of skilled labor, with 80% of employers reporting difficulty filling roles—a 17-year high.
Labor hoarding comes at a steep cost. It leads to idle workers, disengaged teams, and inflated payrolls, draining resources that could fuel innovation. The U.S. Chamber of Commerce notes that hoarding is acute in manufacturing, where competition for skilled operators is fierce. Many U.S. manufacturers hoard labor to avoid rehiring costs in a tight market, often resulting in underutilized staff.
Hoarding labor isn’t security—it’s stagnation, chaining potential to fear.
This practice undermines morale. Skilled operators kept on payrolls without meaningful tasks feel undervalued, increasing turnover and worsening the labor shortage. The BLS reported persistent manufacturing quit rates through 2024, with workers seeking purpose-driven roles, and a 2023 PwC survey found 25% of workers considering job changes within a year, driven by skill misalignment. This creates a vicious cycle: hoarding to avoid shortages leads to disengagement, driving talent away.
Clinging to excess workers doesn’t build resilience—it builds resentment.
Labor hoarding is a relic of a less dynamic era, ill-suited to today’s volatile market. Manufacturers need agility, not static workforces. In short, labor hoarding is a bandage on a broken system, masking symptoms while ignoring the disease: a fear that traps us in holding what we have instead of building what we need.
Veryable’s Solution
Veryable’s on-demand labor platform offers a transformative solution to underutilization and labor hoarding. By utilizing on-demand operators immediately for routine tasks like material handling, equipment setup, and basic quality control, your highly skilled operators are freed to focus solely on high-value work—operating complex machinery, welding, or ensuring precision quality. This strategic allocation transforms skilled operators into force multipliers, amplifying their impact on throughput and quality. A welder no longer fetching materials can craft flawless seams, while a machinist freed from setup duties can program intricate parts. Over time, these force-multiplying operators can be upskilled to back up high-skilled tasks as well.
Real-world success stories highlight the impact.
- Mack Tool & Engineering accessed specialized skills for medical and aerospace parts
- RTIC maintained stringent quality standards while delivering with unmatchable lead times for custom orders
- PhoLicious scaled rapidly to meet demand without excess payroll, fulfilling large orders efficiently
- Scentsational aligned workforce capacity with customer orders, driving sustainable growth
- ShineOn cut costs and launched products at zero cost by matching labor to demand
These cases show how Veryable optimizes workforce efficiency, enhancing profitability and agility.
Veryable addresses labor hoarding by enabling real-time workforce scaling. Manufacturers can deploy operators precisely when needed, eliminating the need for surplus staff. This flexibility reduces costs and enhances responsiveness to market shifts. By ensuring skilled operators focus on meaningful tasks, Veryable boosts job satisfaction, reducing turnover.
This approach positions manufacturers to attract and retain talent in a competitive market. Veryable’s model moves manufacturers from scarcity to abundance, leveraging on-demand labor to maximize skilled operators’ contributions.
The Bigger Picture
The manufacturing labor shortage is not just a challenge—it’s a chance to redefine how we value human skill. Skilled operators are the cornerstone of innovation, yet their potential is squandered when assigned low-skill tasks or left idle through hoarding. Veryable’s model challenges this, offering a path to a more efficient, innovative, and resilient industry. By addressing underutilization and hoarding, manufacturers can close the labor gap and foster a purpose-driven workforce.
This transformation reshapes the manufacturing ecosystem. Freed from menial tasks, skilled operators drive innovation, developing products and processes that enhance competitiveness. Flexible workforce scaling reduces waste and boosts agility, enabling manufacturers to meet market demands efficiently. These changes ripple through the economy, fostering higher productivity, lower costs, and greater growth. A thriving manufacturing sector creates jobs across industries, strengthening the U.S.’s global position.
The shift also tackles societal challenges. Aligning labor with purpose improves job satisfaction, reducing turnover and attracting younger workers. Veryable aligns with this, creating workplaces where all operators feel valued. This counters the narrative of manufacturing as a declining industry, reshaping perceptions to draw new talent.
Veryable’s model is a scalable blueprint for industry-wide change. By adopting these strategies, manufacturers can thrive, creating a future where work is meaningful, productive, and sustainable. This is a call to action—to relax fears, retool labor models, and reap the rewards of a revitalized American manufacturing landscape.
Previous Posts
Trump 2.0 Week 12 Recap: Discussing The Reciprocal Tariff Pause, The Escalating Trade War With China, and More
The Future of Manufacturing and Logistics
Create a free business profile today to explore our platform.
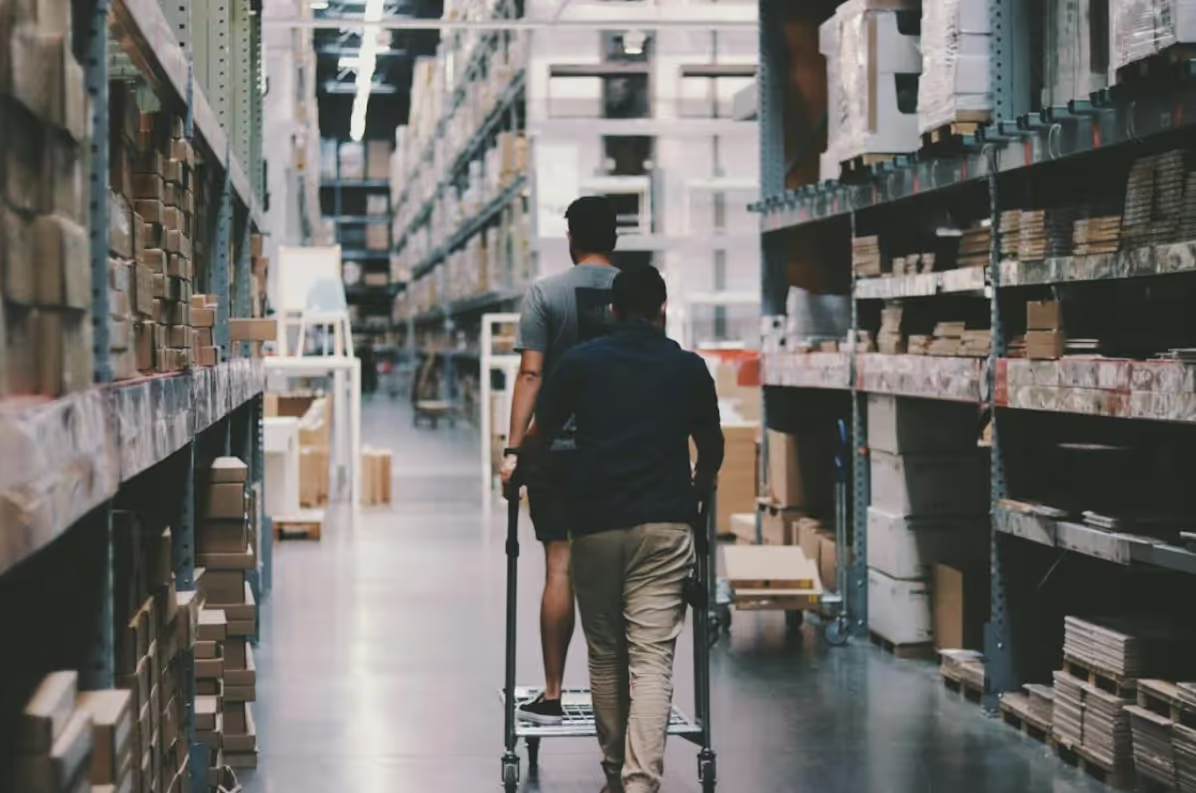