Andon Systems: Definition, Types, and Benefits
You’ve probably encountered a scenario in which you needed to stop production to solve an issue causing defects. And you probably lost more output than you would have liked, especially if you didn't find out about it until a few hours later when someone casually mentioned the problem at the water cooler like it was common knowledge.
At Veryable, we help companies improve operational efficiency by building flexible labor capacity to meet their daily demand. Companies can’t achieve improvements if they can’t keep their line running properly, so we want to highlight andon as a powerful tool to help with this.
In this article, you’ll learn what andon systems are, how to pick which is right for you, and why you should be using one in your manufacturing facility.
What are Andon Systems?
Manufacturing facilities use andon systems to signal problems in real time, directly from the production line, in a standardized way to enable rapid response. Workers use andon systems to alert supervisors, call maintenance, or even to shut down the line to address an error.
The purpose of andon systems is to standardize and speed up the flow of information from the source of the problem to the person who can fix it. If you are familiar with the Lean concept of jidoka (a four-step method for addressing root causes), then you will see the power of andon systems as a tool for applying jidoka.
In the absence of an andon system, a problem might be noticed by an operator but ignored because they know (or assume) that a quality inspection step later down the line will deal with it. That means the problem will exist longer and runs the risk of becoming a quality escape.
With an andon system, the operator could immediately signal that they’ve seen a problem, and the supervisor can respond quickly to investigate. Luckily for the supervisor, andon systems also collect and display the signals in a predictable manner for supervisors to pay attention to. This way they are free to do other important tasks, knowing the andon system will alert them if any problems arise.
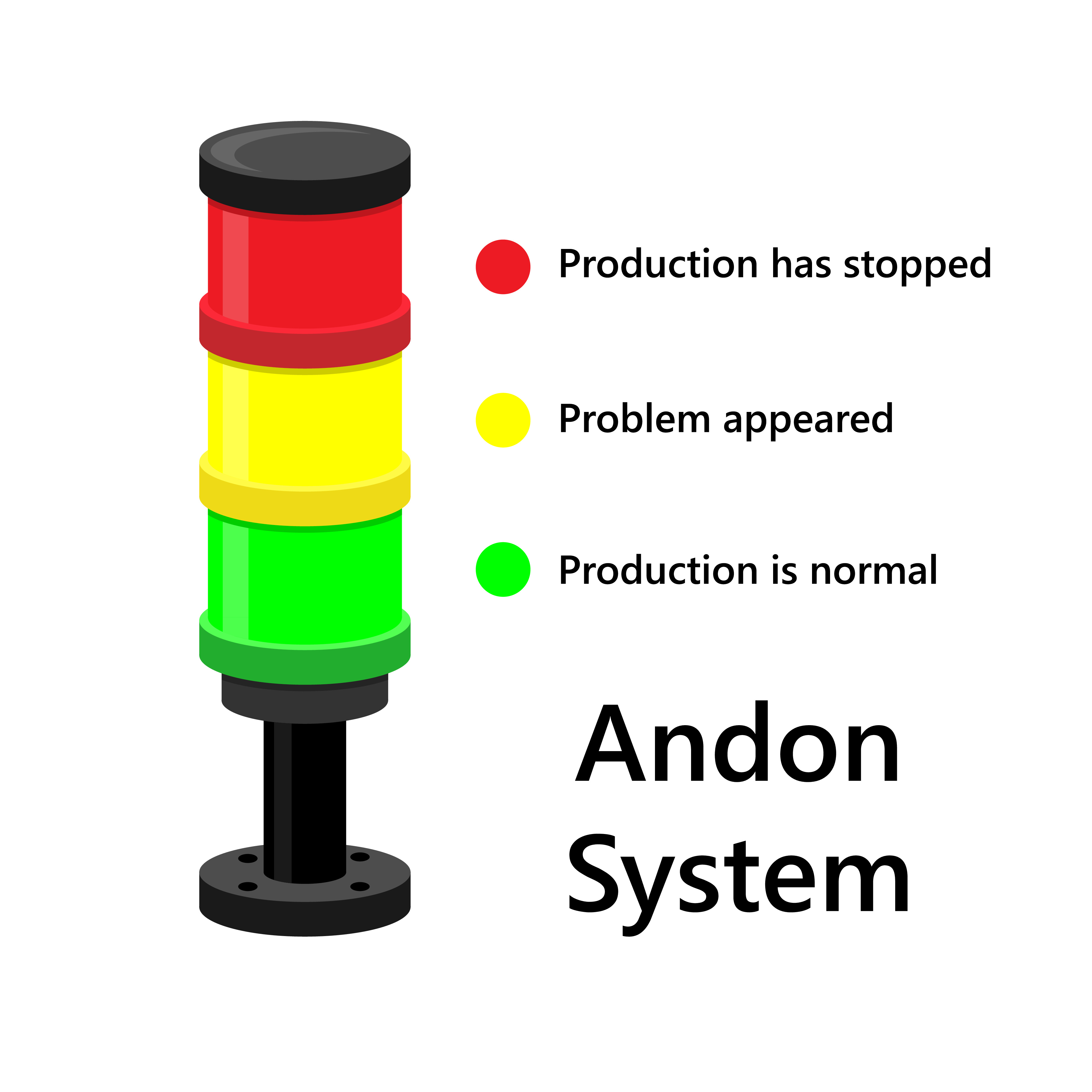
Who Uses Andon Systems?
Toyota (yes, that Toyota) has long used the andon system in its production line. Other major companies that have used andon systems include:
- 3M
- Cartier
- CAT
- Delta
- Honeywell
Just because other companies are using andon systems doesn’t mean they’re a good fit for you, but if some of the most recognizable manufacturers are using them, andon systems are worth considering.
How do Andon Systems Work?
Andon systems need an input and an output. The input comes from the worker on the line, a poka-yoke, or a machine’s PLC. The output is usually intended for the team leader.
Choosing the right inputs and outputs depends on your specific situation: how is your shop arranged? What are your workstations like? How do your supervisors move around the shop?
We will explain the benefits of each input and output type in the sections below to help you decide which andon system to implement based on your answers to the questions above.
Andon System Inputs
There are a few main types of inputs for andon systems:
- Andon cords
- Andon buttons
- Automated andon systems
The inputs are used by operators on the production line to signal a problem. There can be one or multiple inputs for an operator to use at each process step. This setup ensures that the operator can quickly indicate that a problem has occurred, and the supervisor can see exactly where the problem is.
Automated andon systems are the most technically advanced andon systems, and as such they will require additional setup and technical capabilities that the other andon systems would not require. These systems use sensors and data from IIOT devices as inputs, which means smaller shops might not be equipped to get much value out of automated andon systems. However, with the higher investment come the benefits of automating the andon system: less room for operator error, customizable alert triggers, and enhanced analytical capabilities.
Andon cords are best suited to production lines where operators need to move along the line and all the operators in one team are close together, so they can use one andon. These cords are typically installed in the ceiling or along the top of a structure above a production line’s workstations.
Andon buttons are better for simple or small workstations. This is because a button can’t cover as much ground as a rope, and isn’t as easily accessible unless you install multiple andon buttons. The benefit of a button is that they can be installed closer to the operator and would not hang near the workstation. If a cord would get in your operators’ way, then a button is a better choice.
Andon System Outputs
The most common outputs from an andon system are:
- Stack lights
- Andon boards
- Audio alerts
- Electronic messages (SMS, email, instant message)
Choosing the right output for you is a matter of knowing your space and knowing what your workers and supervisors need to be able to communicate effectively.
Of course, having more than one method of alerting your supervisors doesn’t hurt. It might be helpful to have visual and audio alerts, for example, even if your visual alerts can easily be seen by supervisors.
This increases the chances of them seeing an alert right away, and won’t be harmful so long as you don’t overdo it with the alerts. People will learn to ignore alerts if they occur too often and become noise. Or they will become annoyed by them and rush to shut them off, instead of staying calm and fixing the problem. Keep this in mind when designing your system.
Visual Signals
If your facility is very noisy, you should use lights or boards to display information visually. This will ensure your supervisors see the signals, instead of relying on them to hear the signals when so much other noise can block them out.
Stack lights are a common way of sending visual andon signals. These typically consist of three lights on the top of a pole, with each representing a different level of urgency. Green means good, yellow typically means a small error has occurred, and red typically signifies a more urgent matter.
There are also andon boards that can be displayed using LEDs or other digital displays like televisions. These can represent sections of the shop floor and display color-coded information so that supervisors and managers can see the overall status of the facility at a glance. These boards might contain information for multiple product lines.
Audio Signals
If your facility does not have many clear lines of sight for supervisors to see visual alerts, then you should have audio alerts and electronic messages to help your supervisors get alerts even when they can’t see the lights or boards easily.
Electronic Messages
If you want to notify people further from the shop floor or even outside the facility that a stoppage has occurred, you can set some andon systems to send out alerts via email, text, or other digital media to specific contacts.
This is beneficial if you have people who might not be on the shop floor but still need to be aware that the line has stopped. For example, if your shipping department won’t have anything to do because your line has been stopped for a few hours, you could alert them automatically so they can make important capacity decisions.
What are the Benefits of Andon Systems for Manufacturers?
Andon systems are beneficial because they enable manufacturers to move quickly to address problems at the root cause and keep production running smoothly. They can also be used to enable workers to stop the line quickly if needed, or to trigger a series of alerts that increase in urgency and travel up the chain of command while problems remain unsolved.
The key benefits of using andon are the following capabilities:
- Immediately address issues
- Prevent recurring issues
- Reduce downtime
- Give supervisors more time for high-leverage work
- Encourage continuous improvement
The fast flow of information through an andon system means workers can immediately get the help they need to address production issues. This minimizes downtime and avoids recurring issues by ensuring that problems are fixed as soon as possible and addressed at the root.
With andon systems, supervisors can focus on high-leverage work and trust that the andon system will notify them of an issue. That way, they aren’t as focused on identifying defects as they are on making process improvements and other operational excellence initiatives.
With your operators and supervisors equipped to do high-leverage work and address issues quickly, a culture of continuous improvement will be easier to foster. Because operators own the quality of their work, they’ll feel more comfortable taking action, knowing that they have been entrusted with signaling that the quality is subpar. And because supervisors now have some time freed to focus on high-leverage operational improvements, they’ll feel more responsible for seeing these initiatives through because there’s no longer the distraction of quality issues.
What’s Next After Andon Systems in Your Lean Journey?
Andon systems are a great foundational Lean tool for your operations to use for driving consistent quality and preventing waste.
Once you implement your andon system, you will spot where your defects are coming from. With increased clarity on what parts of your process need to be fixed, you might find that redesigning a certain process would help reduce these defects.
When you need to redesign a process, poka-yoke is a powerful Lean tool for making the work mistake-proof. Read our blog on poka-yoke to learn the benefits of mistake-proofing your processes with poka-yoke.
How can Veryable help surface and take action on capacity related issues?
Andon systems are about surfacing an issue, and quickly taking action to resolve that and this is exactly what Veryable suite of operational tools enable. Labor is a critical component of every operation, and it touches every aspect of your operation. Veryable has two platforms that can help transform how you utilize your full time employees, and how you can tap into thousands of rated and experienced Operators to scale your labor up and down with demand. These tools give you a Just In Time workforce that will make your operation better, faster, and more cost competitive.
Here is a brief overview of the platforms…
Veryable's On-Demand Labor Marketplace
Labor will directly or indirectly touch every aspect of your operational performance. It is also one of the largest expenses on your P&L. Ignoring opportunity or being comfortable doing things the way they've always been done makes it just that much harder to find net improvement elsewhere. Leveraging Veryable’s On-Demand Labor Marketplace to build a flexible extension of your full-time workforce will allow your team to precisely match labor capacity to demand on a daily basis. Adopting this approach gives your operations leaders the resources they need to deliver the maximum return for the business and the most value for the customer.
Veryable's Workforce Management Tool
Veryable’s Workforce Management Tool ties together multiple systems (ERP, WMS, MES, HRIS, etc.) to use real-time data to automate the labor planning process and guide your leadership in making better critical decisions. This eliminates guessing, protects against costly forecasting inaccuracies, and enables performance-based decision making without the burden of manual spreadsheet updates or back-of-the-napkin estimating. This tool can operate as a stand alone platform for your full time employees, or you can access Veryable's on-demand marketplace from within this tool to fill any gaps in your operation on short notice. The best part is, you'll be able to view real-time performance data in just clicks for both full time employees as well as Veryable Operators.
Together these systems truly optimize every labor dollar spent across your footprint. This enables better visibility to translate best practices, and can act as a roadmap for continuous improvement.
For more information, visit our Lean Center of Excellence Homepage or our homepage for Continuous Improvement, Operational Excellence, and Lean Professionals.
Previous Posts
Trump 2.0 Week 14 Recap: Discussing The De-Escalation of the U.S-China Trade Conflict, New Deals With Key Trade Partners In The Works, and More
The Future of Manufacturing and Logistics
Create a free business profile today to explore our platform.
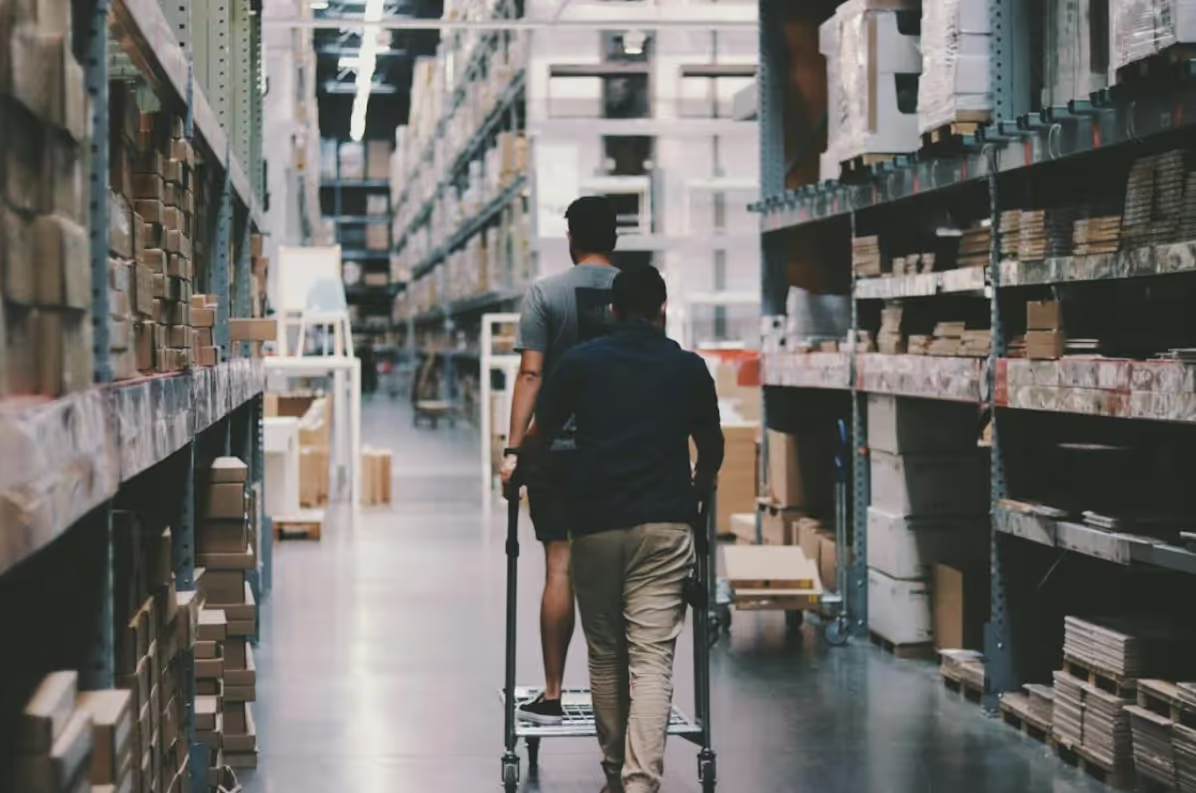