The First Step to Faster Fulfillment: Mastering Dock-to-Stock Cycle Times
An operations manager at a large 3PL facility is facing a high-demand period with record inbound shipments from multiple clients. To handle the influx, the manager focuses efforts on order picking and packing, allocating more staff and resources to these areas in the hopes of meeting delivery deadlines. However, as days pass, delays continue to build, and orders are not moving out as quickly as expected. Customer complaints start coming in, as promised lead times are missed, and inventory seems to be bottlenecking somewhere along the process.
Digging deeper, the manager discovers that the issue originates at the receiving dock. Pallets and cartons of goods have been arriving faster than they can be processed, leaving products stuck in the receiving area. Without a clear process to move these goods efficiently from dock to stock, they linger, unrecorded in inventory, and unavailable for picking. The team has overlooked Dock-to-Stock Cycle Time as a critical metric, focusing only on later stages of the process without considering the impact of delays in receiving and putaway.
This oversight in monitoring Dock-to-Stock Cycle Time has a cascading effect, disrupting inventory availability and delaying order fulfillment. With items not properly processed, the picking team is often waiting for products that haven’t yet been put into inventory, wasting valuable time. This scenario reveals the importance of Dock-to-Stock Cycle Time, as any delay in moving goods from the dock into inventory storage creates a domino effect, holding up orders and impacting customer satisfaction. Recognizing the significance of this metric, the operations manager understands that optimizing Dock-to-Stock Cycle Time is essential for ensuring seamless inventory flow, particularly in high-demand periods where every hour counts.
Dock to Stock Cycle Time
In today’s dynamic logistics landscape, capacity constraints in major fulfillment networks are impacting companies nationwide. As demand surges across eCommerce and inventory management, many businesses experience significant delays in receiving and processing inbound shipments. These disruptions are prompting companies to look for alternative solutions through third-party logistics (3PL) providers who can ensure a steady flow of inventory while maintaining service level agreements (SLAs). For 3PLs, Dock-to-Stock Cycle Time has become an essential KPI, helping them increase throughput, absorb volume, and uphold service standards. This metric measures how quickly goods move from receiving docks to inventory storage and impacts all downstream processes, making it crucial to operational efficiency and customer satisfaction.
Understanding Dock-to-Stock Cycle Time and Its Strategic Importance
Dock-to-Stock Cycle Time represents the period from goods’ arrival at a warehouse to their availability in inventory. A shorter Dock-to-Stock Cycle Time reflects a warehouse’s efficiency in processing incoming shipments, reducing delays, and supporting faster order fulfillment. In high-demand markets, this metric becomes even more critical, as it directly impacts the 3PL’s ability to handle fluctuating volumes while maintaining performance.
As noted in “Principles of Operations Management” by Jay Heizer and Barry Render, “reducing cycle time improves responsiveness and reduces overall costs.” Short Dock-to-Stock times create operational agility, allowing 3PLs to process orders promptly, keep up with seasonal demand, and avoid stockouts or bottlenecks in fulfillment. In high-stakes supply chain environments, streamlined Dock-to-Stock Cycle Time can be a differentiator that gives 3PLs an edge in meeting SLAs and enhancing customer satisfaction.
Key KPIs to Monitor During High-Demand Periods
Beyond Dock-to-Stock Cycle Time, several KPIs are essential for 3PLs navigating increased demand and maintaining SLA compliance. These KPIs help maintain efficiency and can guide data-driven decision-making:
1. Receiving Cycle Time
Receiving Cycle Time tracks the duration from goods’ arrival to readiness for putaway. This metric is crucial for 3PLs to ensure goods move efficiently through the receiving process, setting the pace for the rest of the workflow. As Taiichi Ohno states in “Toyota Production System,” “minimizing time in every phase of production is essential for efficiency.” Streamlined receiving processes enable 3PLs to handle surges without accumulating bottlenecks.
2. Order Lead Time
This KPI measures the total time from order placement to delivery, and reflects a facility’s ability to meet customer expectations consistently. Shortening Order Lead Time requires highly coordinated receiving and fulfillment stages, allowing 3PLs to meet tight SLAs during peak times.
3. Putaway Accuracy
Accuracy in putaway ensures items are correctly stored and accessible for fulfillment. Errors in this stage increase order errors and can delay shipments. As James A. Tompkins writes in “The Warehouse Management Handbook,” “errors in putaway disrupt every subsequent stage.” Reliable putaway processes are foundational for smooth operations, especially when handling high-volume periods.
Strategies for 3PLs to Optimize Dock-to-Stock Cycle Time
To optimize Dock-to-Stock Cycle Time, 3PLs need a blend of adaptive workforce models, efficient receiving processes, and advanced workforce management. These strategies, when implemented effectively, enable 3PLs to meet the demands of high-velocity markets:
1. Flexibility in Workforce Scaling
A scalable workforce model empowers 3PLs to adjust labor capacity in line with volume shifts, helping handle demand peaks while avoiding the overhead costs of permanent staff. In “The Machine That Changed the World” by James P. Womack, Daniel T. Jones, and Daniel Roos, they emphasize, “flexibility in staffing allows companies to respond to changes in demand without the inefficiencies of excess labor.” This flexibility ensures that 3PLs can quickly ramp up skilled labor during peak seasons without overcommitting to long-term costs. Scaling labor up or down as needed is especially useful when dealing with seasonal or unpredictable surges. A flexible workforce minimizes idle time during slow periods and provides enough operators to prevent bottlenecks when volume spikes. This approach improves overall cycle time and reduces excess spending, aligning labor expenses with demand levels. Flexible workforce models also allow for rapid adjustment to client needs, helping 3PLs remain resilient in changing markets.
2. Enhanced Receiving Efficiency
Receiving efficiency is critical for rapid inventory turnover, impacting Dock-to-Stock times and overall throughput. By training operators on streamlined receiving processes, 3PLs can ensure goods are processed and moved to storage without unnecessary delays. In “Lean Thinking” by Womack and Jones, the authors describe eliminating waste in every step of the process, stating that “wasted movement and delays are opportunities to apply lean principles.” By reducing non-value-added activities, 3PLs can maximize receiving throughput, avoiding inventory backlogs and enabling faster processing. Efficient receiving directly supports a 3PL’s ability to manage high volumes and fluctuating order demands. Streamlined receiving enables workers to unload and process goods quickly, freeing up dock space and allowing new shipments to flow in. This approach also supports Dock-to-Stock Cycle Time by moving inventory through the warehouse as quickly as possible, reducing order lead times and creating a seamless flow from dock to inventory.
3. Workforce Management System for Precision Scheduling
Implementing a workforce management system enables 3PLs to match labor availability with real-time demand, optimizing labor utilization without overstaffing. A well-integrated workforce management system helps allocate operators based on actual workload requirements, which directly improves Dock-to-Stock Cycle Time by ensuring the right amount of staff at peak periods. As noted in “Operations and Supply Chain Management” by F. Robert Jacobs and Richard B. Chase, “intelligent scheduling enables companies to match resource needs to demand efficiently,” helping to create a precise balance between staffing and productivity. By dynamically adjusting operator schedules, 3PLs can eliminate common staffing issues that lead to delays and inefficiencies. Workforce management systems allow supervisors to scale labor allocation according to order volumes, maintaining high service levels while avoiding excessive labor costs. This optimized scheduling provides consistent coverage at the receiving stage, accelerating processing times, and keeping inventory flow uninterrupted.
4. Accurate and Efficient Putaway Practices
Accurate putaway practices reduce the risk of misplaced inventory, which can create picking errors and slow fulfillment. Proper training and consistent execution ensure that inventory is always correctly placed, minimizing retrieval time during picking. In “Warehouse & Distribution Science” by Bartholdi and Hackman, the authors assert that “effective putaway practices set the foundation for downstream processes, reducing time spent in correctional tasks and ensuring smoother operations.” Efficient putaway supports every subsequent stage of the fulfillment process, improving overall productivity. Streamlining putaway helps avoid costly and time-consuming corrections while making products readily accessible to operators. This supports faster order fulfillment, a shorter Dock-to-Stock Cycle Time, and a better end-to-end customer experience. Accurate putaway practices are essential for large, complex inventories, where misplacement can have a substantial impact on order lead times and picking efficiency.
5. Cost Efficiency Through Labor Flexibility
Flexible labor models reduce operational costs by aligning workforce resources with actual demand levels. This approach enables 3PLs to avoid the high overhead costs associated with a permanent workforce while meeting peak demand with a scalable labor force. As discussed in “Lean Warehousing” by Paul A. Myerson, “labor should be viewed as an agile resource, capable of adjusting with demand.” Effective labor flexibility reduces waste while enabling high responsiveness to demand fluctuations, maintaining efficiency without sacrificing productivity. Aligning labor with demand improves cost efficiency and supports agility, as 3PLs can adjust labor spending according to workload rather than fixed costs. This approach not only optimizes labor expenses but also supports operational scalability, providing a responsive workforce that meets SLAs. The result is an efficient, cost-effective operation with reduced overhead and increased adaptability to high-demand cycles.
Bringing It All Together: Why Dock-to-Stock Matters
In today’s logistics environment, Dock-to-Stock Cycle Time has become an essential metric for 3PLs navigating fluctuating demand. By focusing on adaptable workforce solutions, data-driven management, and efficient putaway practices, 3PLs can maintain high service standards and meet SLA commitments. Optimizing Dock-to-Stock Cycle Time enables 3PLs to handle demand spikes with agility, ensuring efficient, cost-effective operations and establishing a competitive advantage in a rapidly evolving market.
Getting Started
To get started with on-demand labor, take 5 minutes to create your free business profile. Our team of experts will reach out shortly after to walk you through the process and ensure that your team is setup for success. If you need any assistance, please contact us.
Previous Posts
The Labor Crisis No One’s Talking About: Wasted Skill, Not Missing People
The Future of Manufacturing and Logistics
Create a free business profile today to explore our platform.
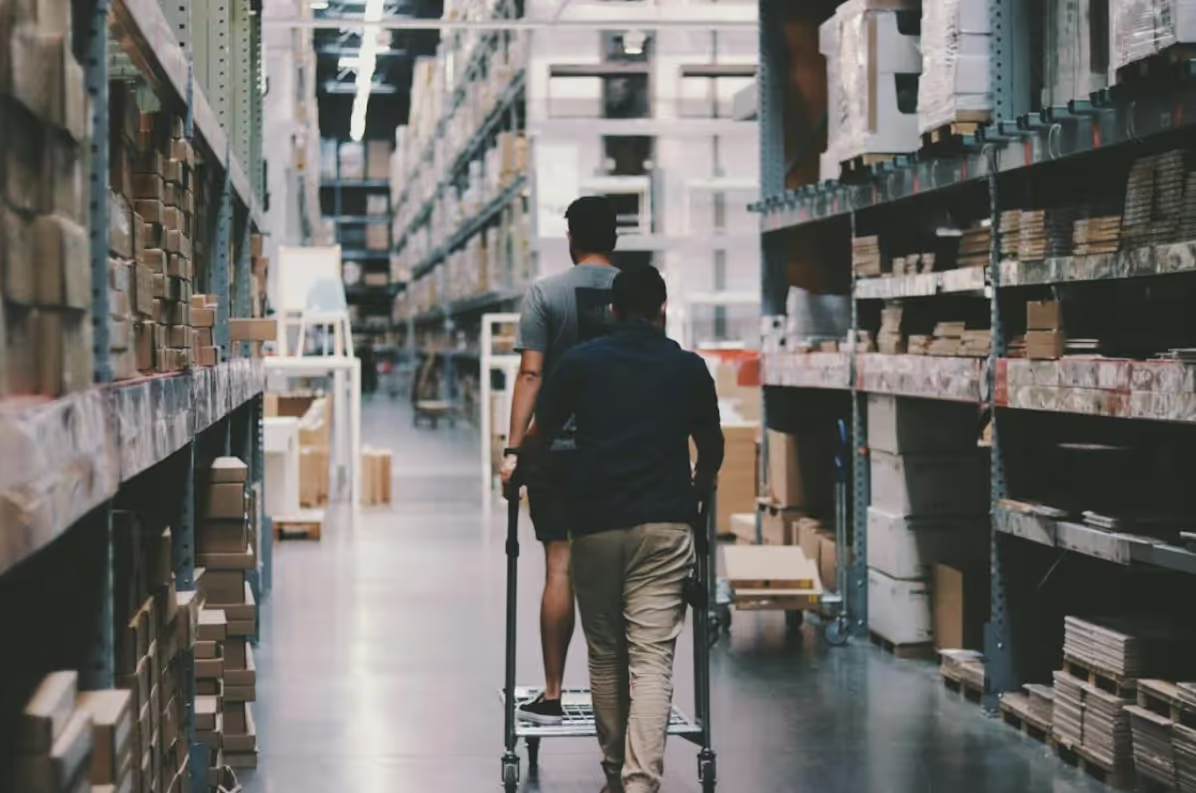