On-Time, In-Full (OTIF): A Key Supply Chain Metric
Delivering on time and including everything the customer ordered are key to succeeding in the supply chain. So how should you measure your performance in this area?
At Veryable, we know how important OTIF is because we empower businesses to improve their performance by using our on-demand labor marketplace to gain flexible capacity. We won’t focus on that here, but instead will share what we’ve seen work for other high performing businesses.
In this article, you’ll learn what the on-time, in-full metric is, how to calculate it, and how to improve your performance in this key area.
Definitions of On-Time, In-Full
The basic definition of on-time, in-full (OTIF) is the percentage of orders you fill that include everything the customer ordered and arrive at the designated location on time. This metric shows your business’s ability to deliver on its promises and build trust with the customer.
There are different ways to measure OTIF, depending on what perspective you have on this metric. If you view it from your business’s perspective, you will measure it differently than if you look at it from the customer’s perspective.
One way of measuring OTIF is as a measure of how often you deliver on-time based on your average lead time. This gives your business the most wiggle room, but is not the best customer experience. While it might look good on paper, this is not the approach for you if your business wants to gain a competitive edge.
The other way of defining OTIF is as a measure of how often you meet the customer’s desired delivery date and deliver everything they need. This is the truest measure of on-time delivery. Viewing the lead time from the customer’s perspective provides the best customer experience and can win you repeat business.
The On-Time, In-Full formula
The on-time, in-full formula is simply the percentage of all deliveries that are shipped on time and in full. The formula is:
(Orders delivered on-time / Total # of orders shipped) * 100
You should aim for OTIF to be at least 95% if you want to compete with leading companies in the supply chain. You can really start to stand out if your OTIF is above 98%.
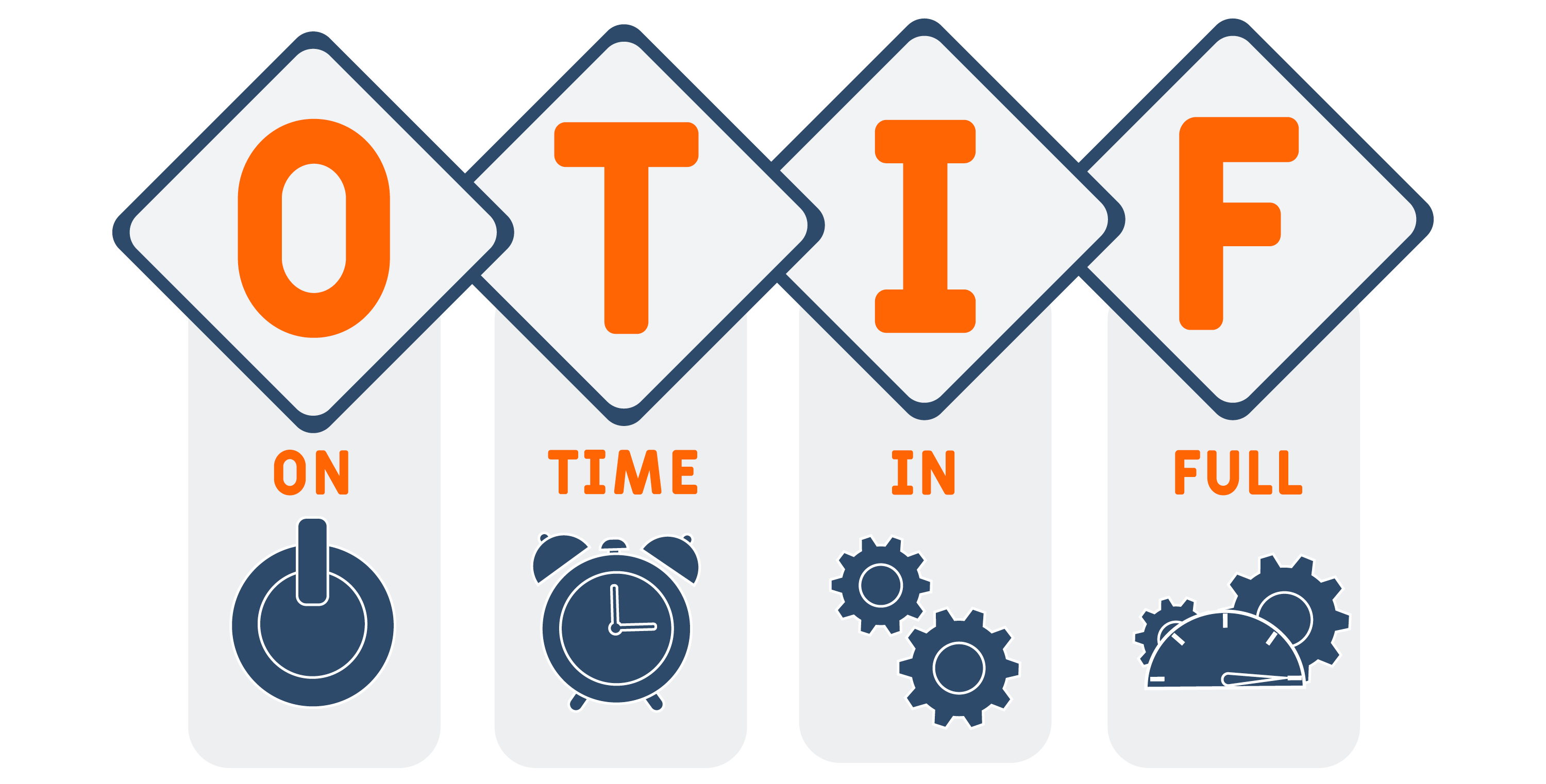
How to Improve OTIF
If your on-time, in-full rates aren’t where they need to be, there are key steps you can take to make a huge difference. You will need to analyze your whole process and the expectations you’re setting for the customer.
The main way you can improve OTIF is to reduce your cycle times. This means you can complete your work more quickly and ship the order sooner. Reducing cycle times will give you more wiggle room to start shipping earlier and eventually take on more orders, once your OTIF is where it needs to be.
To improve cycle time, you should monitor and manage bottlenecks, eliminate activities that don’t add value, reduce setup activities, fund improvements in value-add activities, and add shifts or workers to increase capacity. Adhering closely to Lean manufacturing principles will get you far in this direction.
Example activities that would fuel improvement include ensuring the dock is clean so that search time for materials is minimized, ensuring tools are organized at each workspace, removing inventory piles from the flow of work, and ensuring workers are keeping pace and reporting any defects as soon as they see them.
Finally, you should ensure you are setting clear expectations for yourself in the eyes of the customer. Make the promise date clear, and make it one that you can meet! The more the customer understands what you are offering and how quickly you can do it, the less likely they are to get frustrated or make unrealistic requests.
Learn more about how to improve OTIF by starting with our in-depth blog on reducing your cycle times to improve service levels.
To learn how The Veryable Solution can help you improve OTIF Performance, click here.
Previous Posts
Trump 2.0 Week 25 In Review: July Deadline Extended, 50% Copper Tariff Announced, and Higher Tariffs for Canada, Brazil, and BRICS
The Future of Manufacturing and Logistics
Create a free business profile today to explore our platform.
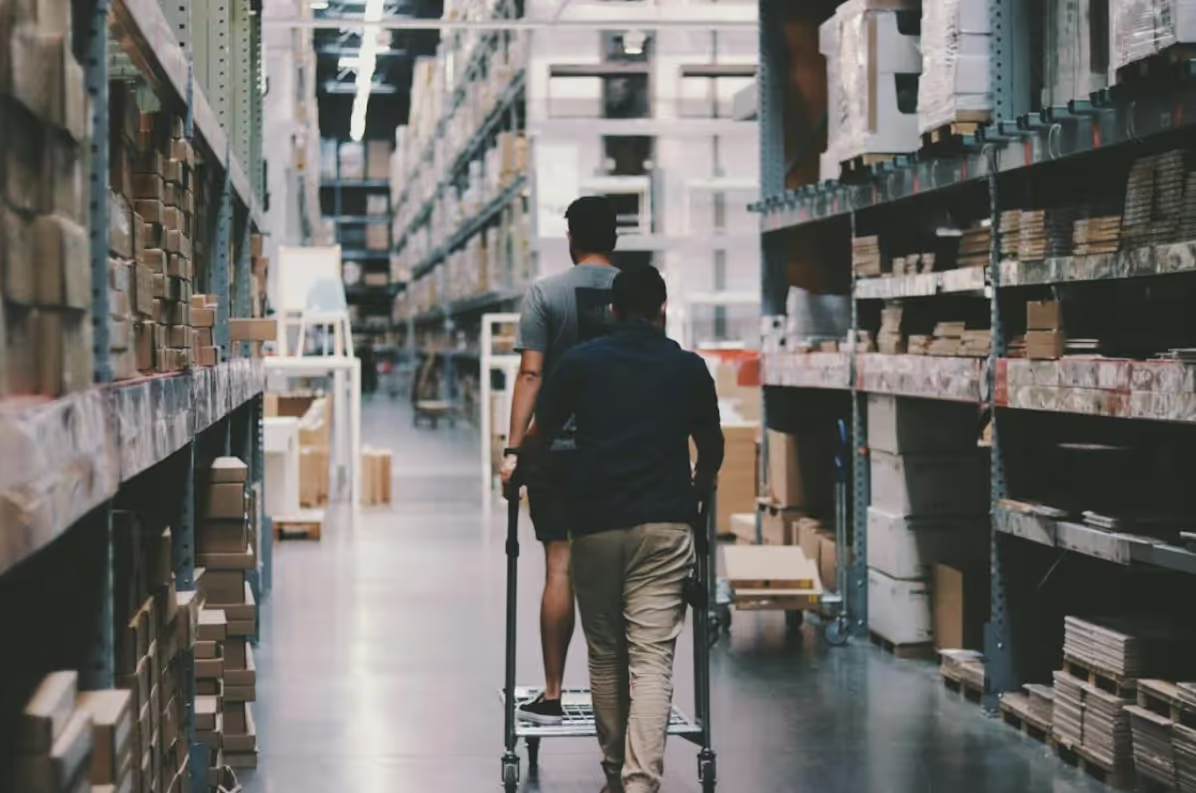