Clean Up Your Shop Floor
If your production facility or shop floor is struggling to maintain consistent results or reach productivity targets, then it’s time to step back and consider taking a more basic approach and cleaning up your facility. Uncontrolled production variability cannot be addressed until the work areas have been organized and eliminated as a source of variability.
Unless you address the noise in the system first, performance improvement projects will not lead to sustained results, nor will the operation become stable. A fundamental approach needs to be deployed in the form of 5s to organize an area and focus its design on production, regardless of whether you use a formal Lean or Six Sigma framework.
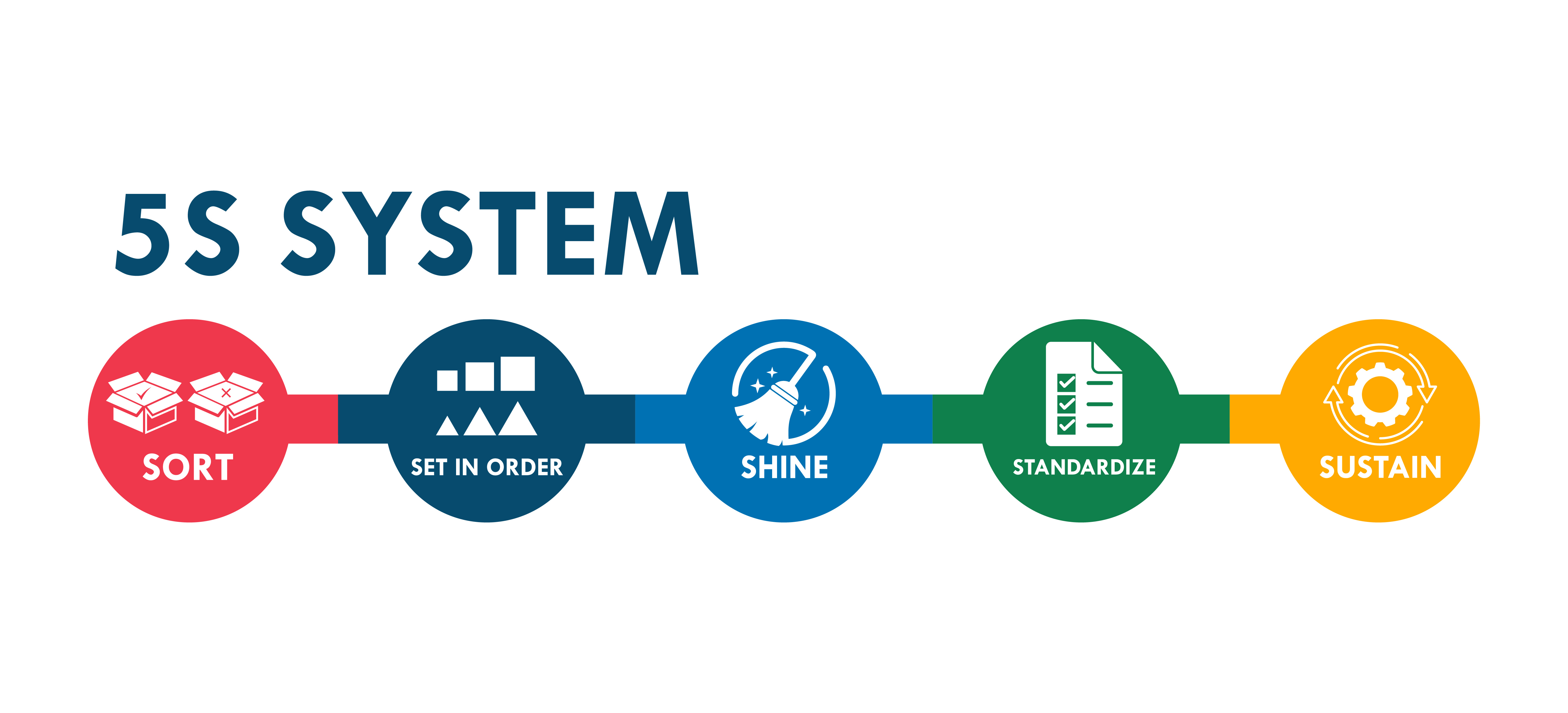
5S pillars
The purpose of the 5s framework is to produce a clean, organized work environment that will enable repeatable high performance. The 5s principles are a foundational piece of the Toyota Production System because consistent results are not possible in a chaotic, disorganized environment. Let’s take a look at each principle:
- Sort – sort tools, parts, and machines to determine its purpose and remove unnecessary items
- Set in Order – develop organizational approach and location for each tool, part storage, and work references to bring order to the area
- Shine – keep the work area clean and organized, particularly one’s own area, on a daily basis
- Standardize – set the expectation that sort, set in order, and shine are part of the operating procedures and describe how and when they will occur
- Sustain – build the 5s fundamentals into the culture and drive participation throughout the organization, including managers to workers
Benefits of cleaning up
By clearing away the clutter, the underlying factors that inhibit performance will become apparent as issues that were masked by the inconsistent workflow of a cluttered environment surface, such as product starting to back up at certain work centers or reoccurring maintenance issues arising. Creating a better work environment in the facility will also lead to a place where people are proud to work, and this will improve morale and retention once people feel connected to where they work.
On-demand solution to start
Here at Veryable, we have the know-how to support 5s implementation through our Veryable Operating Services, plus the on-demand labor you’ll need to clean and organize the facility. Bringing in on-demand operators for organizational projects is a great way to start using the platform to build your own labor pool.
For more information, visit our Lean Center of Excellence Homepage or our homepage for Continuous Improvement, Operational Excellence, and Lean Professionals.
Previous Posts
Capitalizing on Q4 Opportunities: How Forward-Thinking Business Leaders Are Scaling Smarter
The Future of Manufacturing and Logistics
Create a free business profile today to explore our platform.
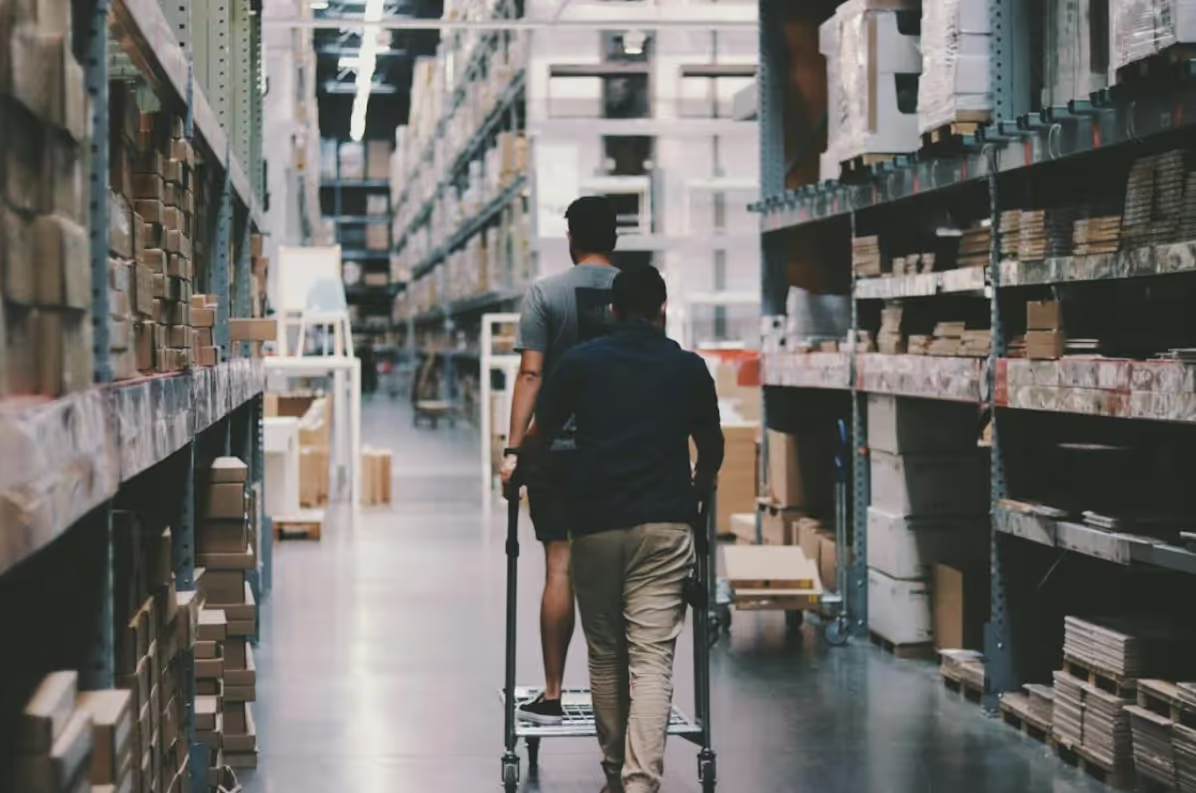