The 12 Step Guide to Manufacturing Facility Moves
It’s a huge ordeal to move into a new facility. Manufacturing leaders have spent many long nights worrying about the details of this kind of project, so we’ve provided a guide on what to do when you’re moving manufacturing facilities.
You’re probably aiming to scale your business or improve efficiency in some other way if you’re moving. That brings challenges besides just the move itself, like shifting resources and examining processes for ways to improve. It’s a lot of stress, and when faced with this many moving parts to consider, it always helps to have a plan.
At Veryable, we see businesses make these types of moves often, and we support a more efficient labor model for companies in your shoes. When you need extra help to make a big transition without slow and expensive contracts or hiring efforts, on-demand labor is a solution with flexibility and scalability. We are biased toward our solution when it comes to finding workers to get the work done, but there are also staffing firms and on-demand staffing companies to help you when moving to a new location. Whatever solution you choose, we’ve written an impartial guide for this process to save you some stress.
In this article, you will learn the twelve steps you should take when moving to a new manufacturing facility.
Twelve steps for moving manufacturing facilities
- Start planning as soon as possible
- Consider all records and inventory needs
- Identify the team you will need for moving facilities
- Prepare your layout drawings for the new facility
- Audit your machines
- Plan necessary changes to your supply chain
- Create a schedule for the move
- Make clear work instructions for all aspects of the move
- Protect products during transit
- Test your equipment after transit
- Conduct an internal audit
- Conduct your final review
Step 1: Start planning as soon as possible
When you are planning a facility move, every minute of time you can devote to planning is needed. Moving is a big project that will require careful thinking, especially if you plan to continue production during the transition and need to maximize uptime. Just like with any office move, advanced planning gives you time to foresee common issues and have a plan for addressing them. It is also wise to communicate the move to key stakeholders such as clients, workers, and investors. Clients will need to know how to reach you or where to expect their shipments from, workers will need to plan how they will travel to and from the new facility, and investors generally like to know about significant changes to the business.
Step 2: Consider all business records and inventory needs
When you have to move everything out of your facility and into another, it’s easy for things to get lost in the shuffle. Make sure that all of your business records are in order, and plan for how you will distribute products from the new location. If you are using a quality management system, now is the time to ensure that all of your documentation is up to date for when you move to the new facility. You will also need a plan for how you’re going to move all your company’s records to the new facility and ensure they are intact and organized when they get there. Create backups of the most important documents and store them securely, so that you are covered in the case of any mishaps.
Step 3: Identify the team you will need for moving facilities
The team of workers you will need to move facilities might be different from the team you need to operate machines or staff the floor every day. There will be plenty of additional work created by the move, and while you will likely need to use movers and other contractors for much of it, there are extra tasks that will fall on your in-house team. You should also plan ahead for if or how you will replace any workers who won’t be joining you at the new facility. Some workers might not want to drive across town if you’ve moved far away, and others just might not want to go through the change. To replace these workers, you can hire, use temp staffing, or try a solution like on-demand labor.
Step 4: Prepare your layout drawings for the new facility
Find your drawings for the current and new facility so you will have them as a reference. At this point, you can also start thinking through where you will put all of your machines and work areas in the new facility. This is more than just due diligence; this is an opportunity to take full advantage of the relocation because you might be able to reorganize your shop floor in a more efficient way at the new facility.
Step 5: Audit your machines
It is best to assess the condition of your machines before the move and document this information thoroughly. That way, you can make any decisions about repairing versus replacing before you go through the move. For example, you might discover that one of your machines is not in as good of shape as you thought it was. It would be wasteful to move a machine you would end up getting rid of shortly after the move. That’s why it’s necessary to examine all of your machines now and document your findings so you can make important decisions about them before the move.
Step 6: Plan necessary changes to your supply chain
Be sure to consider how the move will affect the ways you are supplied and how you supply others with your products. No matter how well you plan for this, there will likely be some surprises, so be sure to factor that into your financial expectations in the period after the move.
Step 7: Create a schedule for the move
Once you have all of your planning done, create a schedule for the facility move. This should include a timeline with as much detail as you can give. If you need to continue production while moving, you should also include in the plan how you will strategically move machines you aren’t using so that the other machines can keep running. Many companies use this staggered approach to moving facilities. Whatever approach you take, make a detailed plan so are prepared for everything.
Step 8: Make clear work instructions for all aspects of the move
Create clear work instructions for everyone who will be assisting you in the move. Each step of moving your facility’s equipment should be detailed, including how each machine should be shut down, packed, transported, unloaded, and configured at the new site. You should also consider what state your current site needs to be in when you leave. Do you have to clean everything? Do you have to turn off any utilities or any other special tasks that could easily be overlooked? Be sure to include these things in your instructions.
Step 9: Protect products during transit
It is important to protect your products just as much as your equipment when you move. This way you do not have to waste anything your team has worked hard to produce. Make sure that you have a plan in place for the careful transit of your products to your new site, especially if you have goods with a shelf life.
Step 10: Test your equipment after transit
It is important to test your equipment soon after setting it up at the new site. The last thing you want is for something to be broken right as you are settling into a whole new setup. Do a test run by building your product, using every piece of production equipment to be sure that it is working properly. Do not rush straight into full-steam ahead production before you have carefully evaluated how well your machines are working.
Step 11: Conduct an internal audit
Once everything is back up and your production process is running full bore, conduct an audit to see how you might want to change your processes now that you are in the new site. A new facility is a great trigger to look for opportunities for continuous improvement. This allows you to capitalize on the excitement and energy of experiencing your processes with a new perspective.
Step 12: Conduct your final review
After you have done all of these steps, conduct one final review and talk through your internal audit with leaders in your company. They will appreciate the update and you will get the chance to pick their brains about new ways to improve as you settle into the new facility.
Get a Head Start On Fulfilling Your Labor Needs
As mentioned above, you might need extra workers to assist with the move or to replace workers who won’t be joining you at the new facility.
Instead of pulling your full-time employees away from their regular work during the move, you could use Veryable's on-demand labor platform to find workers to help with this transition. This will keep you from extending lead times, having to pay overtime, and hurting your on-time, in-full delivery rate.
To replace the workers who won’t be joining you at the new facility, we suggest not hiring more full-time workers until you are absolutely certain that you need to. This is costly and with so many other uncertainties surrounding a move, this would be a short-term decision with potential long-term effects.
Instead, you could enjoy the flexibility of an on-demand labor solution. With on-demand labor, you could meet your immediate need by bringing in workers long enough to help with the transition. Once you establish a connection with these workers through the platform, you can easily add them to your labor pool if you want them to work with you again in the future. Using on-demand labor would reduce the number of lost full-time employees you would have to replace and eliminate the need to ask your current employees for overtime.
On-demand labor fits this situation perfectly, due to the lack of commitment required to find workers this way, and the fact that they want to work short-term.
See how RTIC was able to seamlessly move into a new facility across Houston by utilizing Veryable Operators
Case Study: New Location Launch
In 2022, a 300 person facility launched their new location in step with Veryable. Faced with a tough labor market in the area, and expected KPIs to hit, Company A turned to Veryable. Company A focused early hiring efforts on Plant Manager, Shift Supervisors, and Department Leads - Utilizing Veryable Operators for the larger need of laborer roles. HR continued to hire full time employees while the Operations team was able to hit KPIs. As full time headcount increased, the number of Veryable operators decreased until reaching ideal headcount. In the end, Veryable allowed the Operations team to get the facility operating several months earlier than previous locations, resulting in over $2.7M in additional revenue and a 34% increase in on-time deliveries.
Previous Posts
Hidden Inefficiencies in American Manufacturing and How that Impacts Capacity & Consumer Prices
The Future of Manufacturing and Logistics
Create a free business profile today to explore our platform.
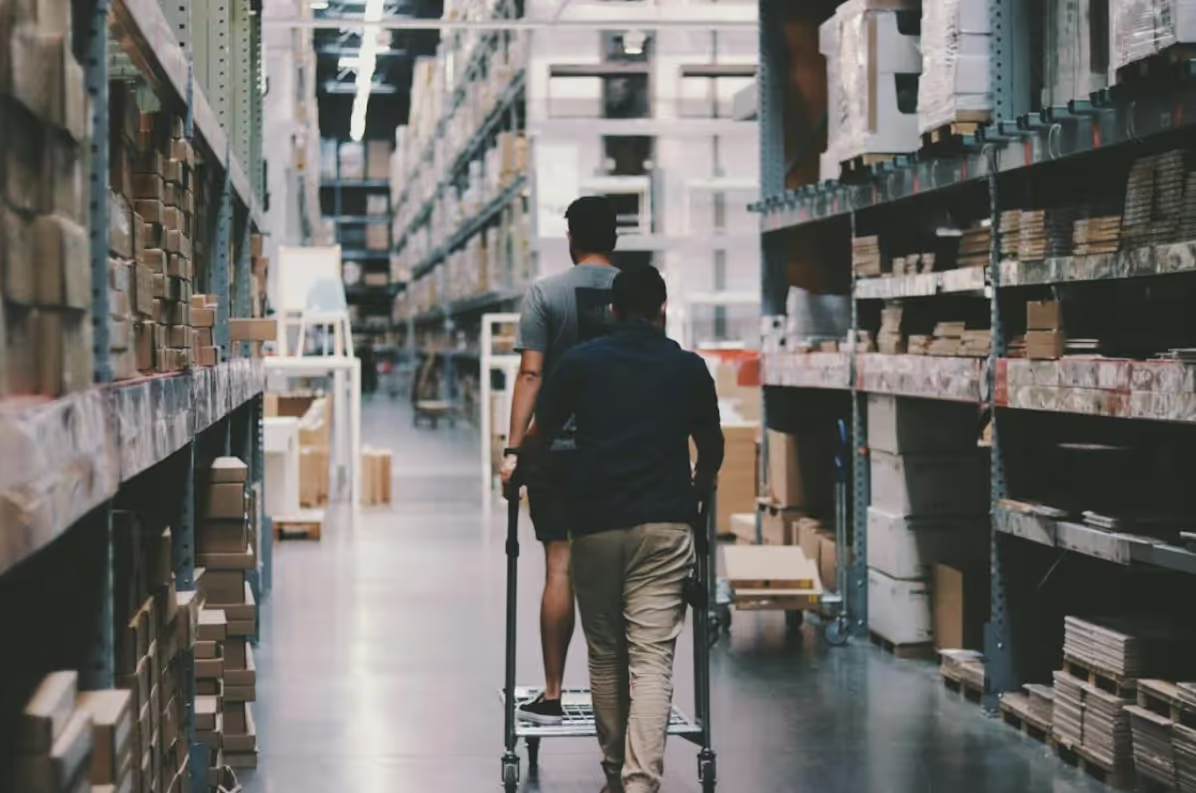