Hidden Inefficiencies in American Manufacturing and How that Impacts Capacity & Consumer Prices
You'd have to be living under a rock to have not heard that tariffs are currently a big part of the news cycle. One of the key talking points is around how these tariffs could force reshoring and then, whether or not manufacturers can even shift production to the U.S. if they want to.
Articles have been written highlighting all of the obstacles that onshoring presents with some common themes showing up:
- Onshoring will take years.
- Onshoring will need qualified labor.
- Onshoring will raise costs.
I point out these themes because - while onshoring/reshoring isn't going to be a walk in the park - there are hidden inefficiencies in American manufacturing that give us a feeling of "constraint" when the reality is that we have the ability to get so much more out of what we already have. In many cases, we don't need to build massive new factories, we just need to more fully utilize the ones that we already have.
It's tough to get the exact data (trust me I tried), but there are countless manufacturers that are not optimizing their production output. They're running 1 shift, 40 hours a week (occasionally 50), and have an order backlog that ensures they can consistently keep their employees "busy."
Let's dig into the impact of that.
In a given week there are 168 available hours. A manufacturer that runs a 40 hour production week is only scheduling 23.8% of all available hours.
Right off the bat, many factories are only running 23.8% of the time. Then, you have to factor in OEE. For those not familiar, OEE stands for Overall Equipment Effectiveness and measures how effectively a manufacturing process is utilized compared to its full potential during planned production time. It takes into account:
- Availability - the percentage of planned production time that the equipment is available for operation.
- Performance - the speed at which the equipment operates compared to its theoretical maximum speed.
- Quality - the percentage of good units produced compared to the total units produced.
World Class organizations run at 85%+ OEE. Unfortunately, most manufacturers aren't operating at that level and the average OEE score across manufacturing falls around 60%. So take that 23.8% down to 14.3%.
We know that it's impossible to hit 100% OEE. However, if more factories ran 24/7 production and those same factories could operate at a world class level on OEE, we'd be looking at 85% of theoretical maximum production capacity available to us instead of 14.3%.
Going back to the obstacles that are constantly presented, we can start to chip away at those pretty quickly. For a good number of American manufacturing operations (of course not all), we can increase output 594% just by more effectively utilizing the facilities and equipment that are already in place. This isn't a years-long exercise that requires significant capital investment, nor is it as easy as flipping a switch, but it's VERY possible and just requires some leaders who are willing to put in the work to make it happen.
Taking this a step further, we can start to look at how that rolls into prices. There are countless textbooks written on accounting for manufacturing companies, but at a very high level, we can just look at fixed costs (not worrying about allocations, direct vs. indirect, etc.) to get a taste of how these hidden inefficiencies roll through to the consumer. Let's take a manufacturer who is currently running 40 hours every week with average OEE and produces 20,000 units/month. Total fixed costs come out to $267,000/month. In this example, the fixed cost per unit is $13.35.
Assuming that same manufacturer was running 24/7 with 85% OEE, they could produce 118,881 units. With total fixed costs of $267,000/month, the fixed cost per unit is now $2.25.
Going back to the obstacles presented, we can further chip away at those when it comes to onshoring raising costs. If executed properly, you can start to drive down the cost of American manufacturing by delivering improved productivity from our manufacturing facilities.
Of course, the feedback you'd get as you lay out these numbers is that these American manufacturers can't run 24/7 because there aren't enough qualified people (Obstacle 2 from above) who want to work in manufacturing anyway. So even if we could theoretically run our factories more and improve OEE at the same time, it doesn't really matter because where are we going to find the people who want to work and who have the necessary skills?
At Veryable, we have thousands of partners across the country who can attest to the fact that there are plenty of people who want to work in manufacturing. Veryable gives you a way to not only tap into manufacturing labor, but to do so in a way that allows you to build additional capabilities into your operations at the same time. With our Workforce Management software you can ensure you're optimizing your workforce & production scheduling to deliver what the business needs at the lowest cost per unit and with our digital marketplace for on-demand labor you can build a skilled, trained, flexible extension of your workforce that allows you to fully remove labor as a constraint on your operations, improving productivity, flexibility, and agility in the process.
American manufacturers have leaders at the helm who are expert problem solvers, and many of these leaders just need a little freedom to operate to be able to deliver what many people are saying is impossible. I say we give them the tools they need and let them get to work.
Previous Posts
Flow or Fail: Throughput Is the Real Warehouse Constraint
The Future of Manufacturing and Logistics
Create a free business profile today to explore our platform.
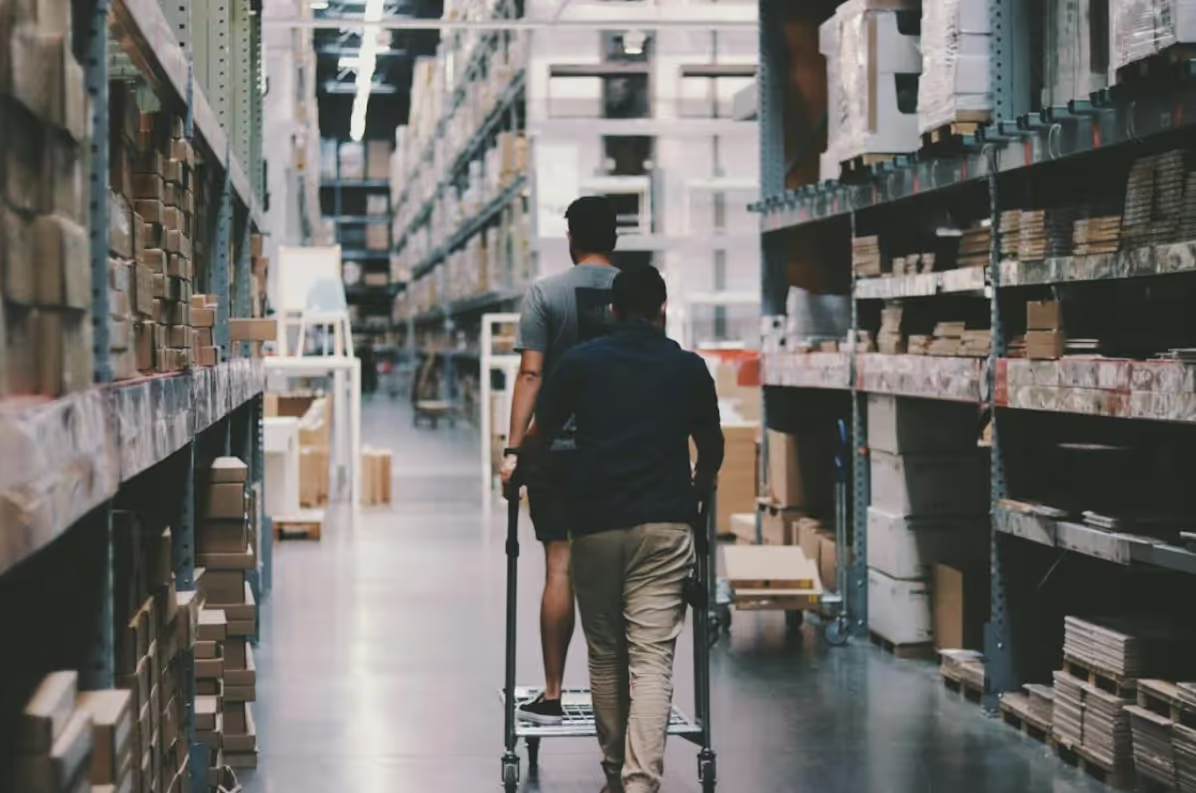