Don't Call Yourself Lean If You Don't Use On-Demand Labor
The current lean paradigm is about to drastically change, leading to an expansion of just-in-time. While leveling is a part of any lean production system, we need to see it for what it is: a countermeasure to rigidities that ends up being anti-lean. The gist of this article is that we now have a better solution.
Digital marketplace platforms are a good example of what economists call a “general purpose technology”: something that doesn’t just reduce costs or improve productivity but produces a cascade of improvements and makes things possible that used to be impossible—hence their power.
Veryable, for example, is a platform that allows workers who don’t wish to (or can’t) operate within the constraints of a traditional full-time/part-time employment contract, to find businesses for short work engagements. What immediately came to my mind when I first heard about it was “just-in-time”: this was just-in-time labor, and it would change everything.
Labor and Just-in-Time
Kiichiro Toyoda’s 1938 concept of just-in-time is at the heart of Toyota's transformation from an insignificant producer to the largest and most respected automobile manufacturer on the planet: “I believe that the most important thing is to ensure that there is neither shortage nor excess, that is, to ensure that there is no excess labor and time for the designated production. There is no waste and there is no excess. It means not having to wait for parts to be circulated around. For Just-in-Time, it is important that each part be ready 'just in time'. This is the first principle of increasing efficiency.”
But to implement the concept, practitioners had to draw the line at labor. Through persistence and ingenuity, they invented techniques such as SMED (rapid changeover, which enabled the reduction of batch sizes), flow cells or kanban, and overcame the naysayers. But they never broke through the rigidity of labor. Advances on flexible manpower lines and multiskilling did add a bit of flexibility, but always within the confines of a fixed number of workers that could only be changed monthly—and even then, not by much. They were constrained by the high transaction costs associated with hiring, onboarding and offboarding.
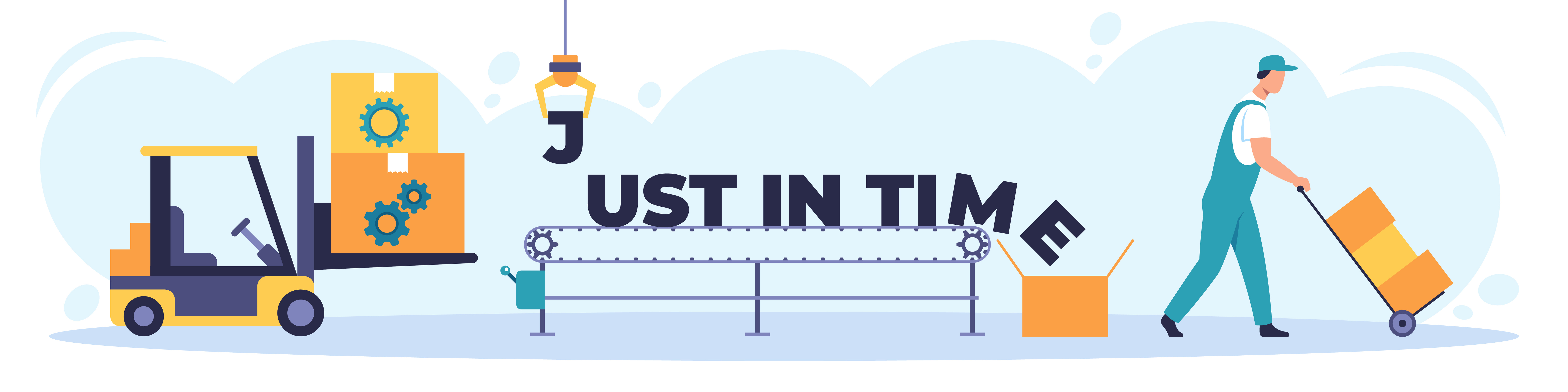
Leveling Isn't Lean
The result was a limited application of the just-in-time principle, with a workaround known as production leveling, which—if you really think about it—is the opposite of all we call lean. Yet, it is accepted without question as a fundamental block of any lean system. Leveling is the accepted deviation from just-in-time which increases inventory and/or lead time. The only reason we level is that some resources are still too rigid for just-in-time. If you can’t scale workers up and down to follow your customer demand any faster than say, once a month, then you have to produce based on the average monthly demand. This is what we call the leveling period.
The longer the leveling period, the greater the gap between actual daily demand and leveled production. Typically, this results in inventory (in the form of supermarkets), but depending on the production environment, it may also result in longer lead times if the “inventory” takes the form of unreleased customer orders. Formulated this way, can we really say with a straight face that leveling (aka heijunka) is lean?
Labor is a major reason for leveling, and equipment is another. Plants usually have excess equipment capacity by design, so this may play a smaller role, but nevertheless, the unused capacity is an economic drag on the business.
Digital Marketplaces And The Power of Flexibility
This is where digital marketplaces change the lean paradigm. They overcome the rigidity currently built into the use of labor and equipment by matching demand and supply at essentially zero transactional cost. Just like reducing changeover costs enables lower batch size and just-in-time for materials, reducing transactional costs enables small batch size for the use of the two other manufacturing resources, labor and equipment. Our experience at Veryable is that a business today can post an offer for a same-day work shift, get operators bidding on the opportunity within minutes, and fulfill 93.2% of their posted offers. Thus, one use case for the platform is to compensate for unexpected absences or “failure demand” without sacrificing the continuous improvement activities that typically get sidelined when the product “needs to get out the door”. The main use case, of course, is to post short opportunities (or “ops”) to closely follow actual customer needs.
Even for equipment rigidities, a marketplace solution can open up extraordinary possibilities. All plants have idle machinery. Imagine making a machine available for other businesses who have a need for additional capacity. You know you won’t need machine X for the next two days, but a neighboring company might just have suffered a breakdown on a similar equipment and won’t get it repaired until next week. You can post your machine’s availability and specifications, be found on the platform, and monetize your idle assets while the other party keeps its promised shipping dates. Moving material and finding storage space is also possible on B2B marketplaces today, which illustrates the cascading effects of the technology.
Generalization of just-in-time is the new frontier in lean. It’s an exciting world where new tools and methods are being developed, and fantastic opportunities abound. Soon, you won’t be able to call yourself a lean company if you don’t use on-demand labor.
For more information, visit our Lean Center of Excellence Homepage or our homepage for Continuous Improvement, Operational Excellence, and Lean Professionals.
Previous Posts
Trump 2.0 Week 12 Recap: Discussing The Reciprocal Tariff Pause, The Escalating Trade War With China, and More
The Future of Manufacturing and Logistics
Create a free business profile today to explore our platform.
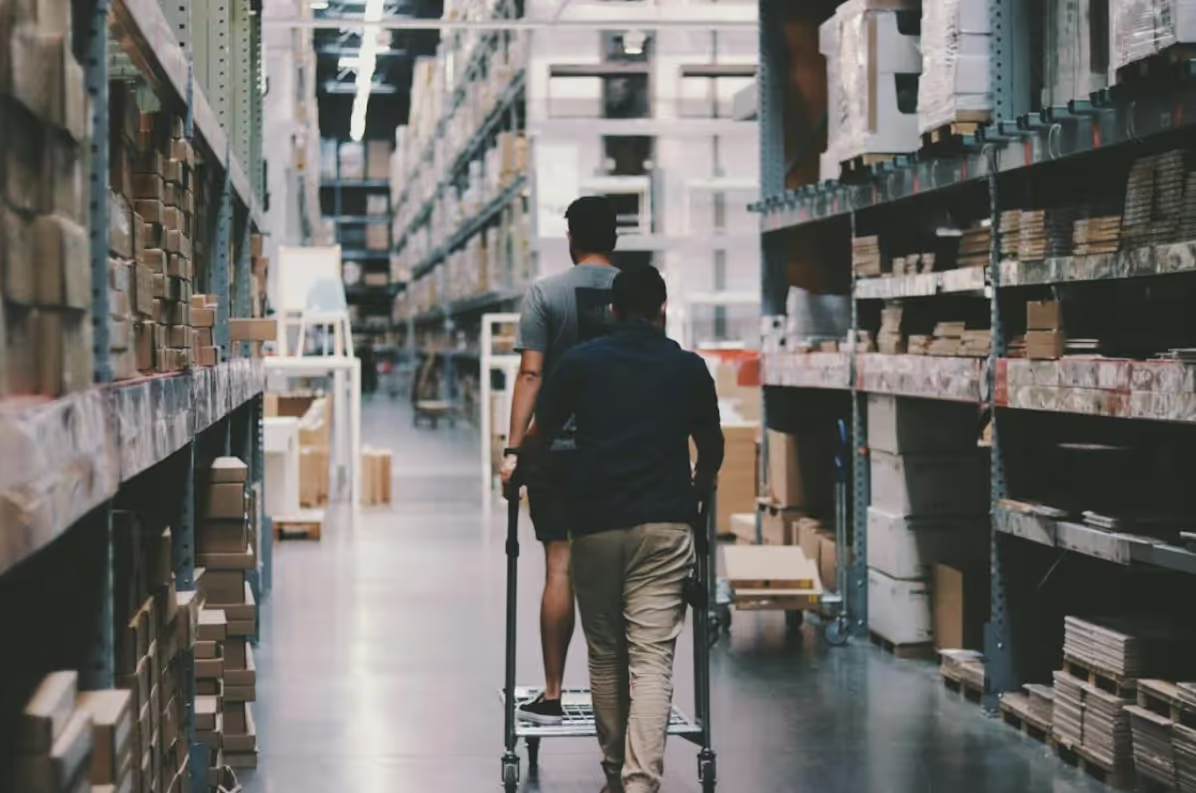