Introduction to LEAN 4.0
Lean manufacturing is ready for its next iteration. While Lean theory draws upon practices that have been around for centuries, the commonly practiced version of Lean today is somewhere between 60 and 80 years old dating back to the early days of TPS.
Lean in its current form works across a broad spectrum of environments. Rather, we believe that today’s landscape offers practitioners new capabilities, consistent with traditional Lean theory, that can take business performance and manufacturing theory to the next level.
A Quick Introductory Story
I had a client once, a medium sized industrial equipment manufacturer, that reached out to help address a stagnant growth situation. They were a fairly mature Lean shop with robust planning and operational practices. However, they had only managed to achieve 1% Year Over Year revenue growth over the last 3 years despite a healthy market and growing customer base.
They would conduct demand planning analysis on a quarterly basis (every 13 weeks) to determine their line rates for the quarter and were pretty rigid about communicating product lead times to the market. Their typical lead times were 2-6 weeks, where 2 weeks was approximately industry standard, and lead times were adjusted weekly based on their firm backlog.
Whenever large order volumes came in, the plant would smooth out the demand over future weeks and extend lead times accordingly. Not surprisingly, as the plant whittled away at the order book, few new orders came in until lead times returned closer to 2 weeks. The analysis concluded that they were missing ~50% of potential business due to this accordion pattern. It’s the classic case of a self-fulfilling prophecy that all too many manufacturers deal with today. You could grow your business if you eliminated self-imposed constraints and listened more closely to the market.
The Problem With Averages
“The assembly line can only work only if you have a standardized product” – Henry Ford
While Ford’s claim specifically refers to a production line, it’s reasonable to extrapolate his point to apply to a broader notion of “progressive flow.” Furthermore, to what lengths can we extrapolate the notion of a “standardized product”? Is it limited to product platforms, the whole portfolio, the whole product strategy? Our contention is that it’s most useful to think in terms of the entire product strategy, e.g., design, feature, cost, lead times, etc. Now ask yourself: how much functional standardization do I actually have across my product portfolio and manufacturing strategy?
It’s not a stretch to restate Ford’s claim as such: “Progressive flow is difficult, and potentially impossible, if you have high degrees of variation in product design and customer requirements.” More often than not, the problems we see in manufacturing stem from businesses unsuccessfully fighting to reconcile this statement on a daily basis. Establishing a progressive flow environment relies on planning around averages. High degrees of variation widen the gaps between the averages, which are the basis of your production plan, and your daily production requirements. The result is a production environment that is inconsistent with market expectations.
Quantum Takt and Heijunka
If we’re learning anything from the current environment, it should be that customer-centricity and speed win in today’s market. Traditional TAKT and Heijunka scheduling are inherently at odds with both. You can imagine an environment 50 years ago where you had a handful of SKUs and you were the only player offering such products. Given that you had your customer base hostage to a small catalog and varying lead times, you could trust averages and apply production smoothing mechanisms to level out daily requirements and keep costs as low as possible.
The game has changed, however, and customers are not tolerating anything short of how they want it, when they want it. Ignoring this need can be a death sentence for businesses and stubbornly applying old fashioned TAKT and Heijunka practices makes you incompatible with your customers. The answer lies in shrinking the time horizon – going from a 13-week TAKT calculation to a daily or less TAKT calculation (i.e., Quantum TAKT). Anticipating demand in 13-week increments is not good enough anymore. Demand in today’s environment needs to be dealt with at the lowest and most finite possible level.
Introducing Lean 4.0
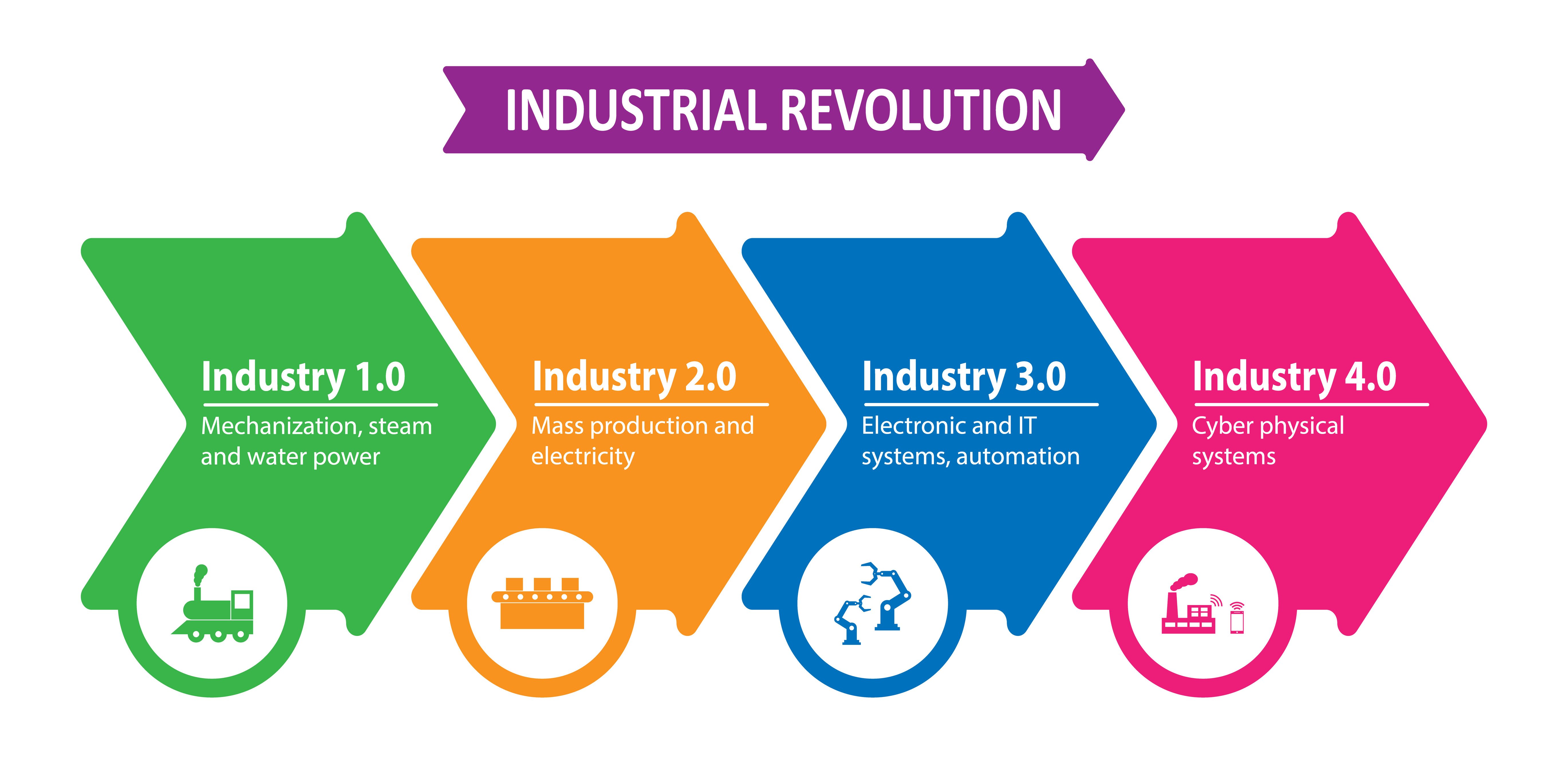
All innovation in the digital manufacturing environment can boil down to improving the precision of your operations, either through asset/human capital performance or operational intelligence. How you think about Lean’s role in the future should be no different.
Starting with this core premise is critical: if what you’re doing is incompatible with the needs of the market than it’s time to evolve or someone else will. It’s about building in complete flexibility and agility to achieve your full market entitlement. In a sense, it’s about eliminating (potentially all) demand planning to liberate your business to win the series of possible games versus the single game you are anticipating. Only then will you break the shackles of a production philosophy that pulls you back to your original estimate instead of reaching your full market potential.
Step one in this journey is to set table stakes on what the market requires and work backward to optimize internal flexibility and agility. Does the market require 1,000 variations of your core product at 2-week lead times across the portfolio? If so, you will probably need to focus on establishing TAKT in finite increments, employing Heijunka only within those intervals, better localizing your supply chain, and taking advantage of on-demand labor to eliminate labor related capacity constraints. Perhaps IoT, additive manufacturing technologies, and wearables would help address the perceived challenges in doing these things. Leading companies are already orienting their strategies accordingly – today it’s a matter of playing offense but soon it will be a matter of defense.
Stay tuned for more in our Lean 4.0 series.
For more information, visit our Lean Center of Excellence Homepage or our homepage for Continuous Improvement, Operational Excellence, and Lean Professionals.
Previous Posts
Trump 2.0 Week 12 Recap: Discussing The Reciprocal Tariff Pause, The Escalating Trade War With China, and More
The Future of Manufacturing and Logistics
Create a free business profile today to explore our platform.
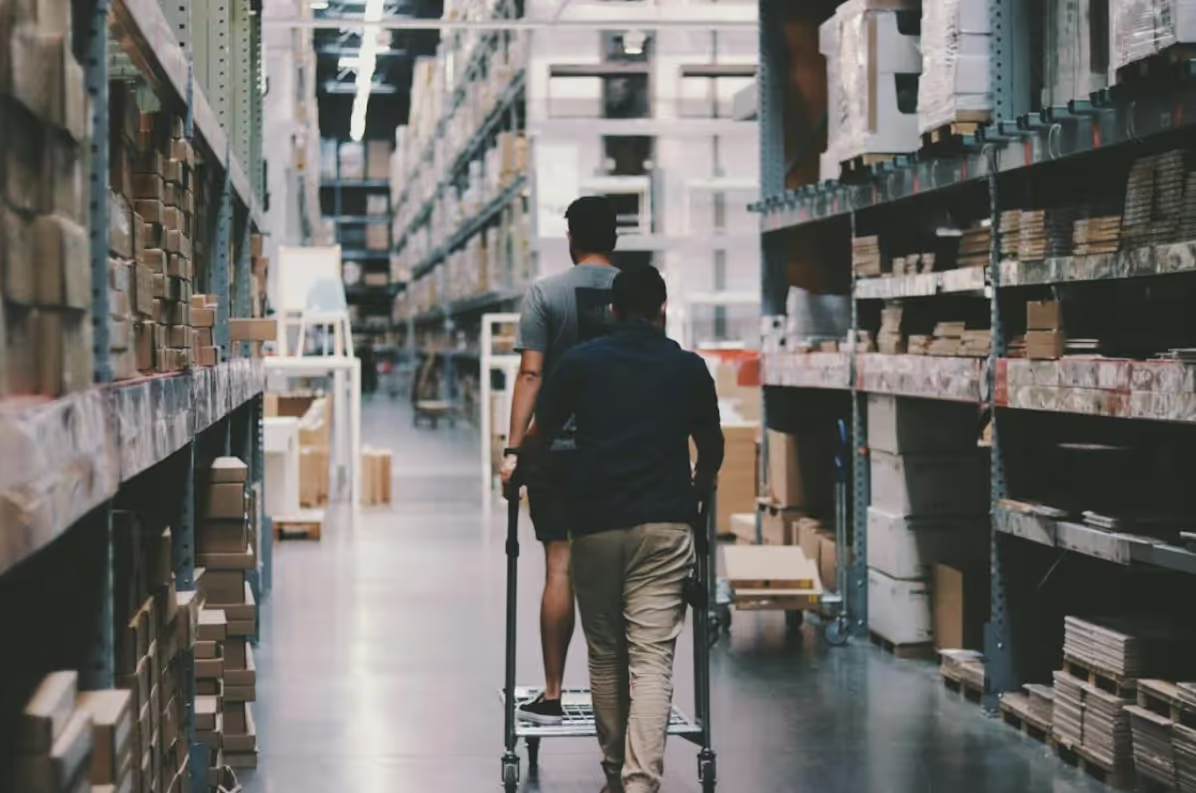