Equipment Maintenance Best Practices
Maintenance isn’t what most people think of when they think of getting work done. It’s right up there with washing dishes, at the top of the list of things people let slide until they can’t ignore it anymore. However, savvy operations leaders know how important it is to stay on top of equipment maintenance proactively. This article isn't about our solution. However, our experience at Veryable with helping many businesses use on-demand labor to get caught up after an unforeseen setback gives us insight into the importance of solving problems before they swell. Maintenance isn’t always the cause, but it’s likely that at least a few times, companies have used on-demand labor to catch up after a maintenance issue rippled into a bigger problem.
In this article, you’ll learn why preventive equipment maintenance is important and what systems and processes you should put in place to effectively manage your maintenance.
Schedule preventive equipment maintenance
Getting ahead of equipment maintenance before it becomes a problem is a great way to save money and avoid unnecessary stress on you and your employees. Properly maintaining equipment according to each machine’s maintenance schedule can reduce costs by avoiding emergency maintenance and extending the lifetime of the machine.
If you wait until something goes wrong to perform maintenance, it’s going to cost you and create more headaches. Reactive maintenance is like fixing the roof as it’s raining: messy, more difficult, and likely to create other problems as it trickles.
Establish rotation pools, functional testing, and spare parts inventory
There are a few quick wins you can achieve when it comes to maintenance, including:
- Establishing an equipment rotation pool
- Implementing functional testing
- Stocking critical spare parts
These additional steps will set you up to keep your operation running smoothly. You'll have backup machines to reduce downtime, you'll be routinely testing equipment to identify problems early, and you'll have a stockpile of critical spare parts so that you don't get held up waiting on a part.
Decide who will manage equipment maintenance
You should identify someone to manage equipment maintenance whose KPIs are appropriately aligned with keeping equipment in working order. Commonly, a facility manager or maintenance manager would be responsible for overseeing maintenance. You wouldn’t want to have machine operators be held primarily responsible for deciding when maintenance is needed, because their performance measures might incentivize them to keep things running at all times, rather than allow for maintenance time. However, the machine operators could be involved as a first line of defense against unexpected problems if you distribute responsibility for equipment maintenance properly and appropriately align incentives.
For example, you would want a machine operator to be concerned with making sure their machine is available and in working order when needed. This could be a target such as the machine being available for 38 out of 40 hours of the week on average, so that maintenance time is built into the schedule. In addition to this, you would want the facilities manager to be responsible for the overall maintenance budget, because they will then enforce the proper maintenance of machines to reduce their overall maintenance costs. It’s important that the appropriate stakeholders have KPIs that reflect your overall business goals, and that there are no conflicting goals between machine operators and the person who manages maintenance.
Decide who will perform equipment maintenance
A crucial part of equipment maintenance is ensuring the maintenance work is performed correctly. You don’t want someone just taking their best guess at how to fix an expensive machine. The decision, then, is between hiring someone in-house to handle the maintenance or finding a contractor to handle the work. The pros of hiring someone on a contractual basis is that they often specialize in repairing the specific machines they work on, and they can free up your employees to work on other things. The cons would be that they are an extra expense, and it takes time to find the right contractor every time you want something done. The pros of using someone in-house for your maintenance needs are that they are familiar with the machine and your operations, they’d be more readily available, and they would make it easier to budget for this cost. The cons of this approach is that you would have someone on payroll throughout the year, regardless of how often repairs are actually needed. You will know what’s right for your business when you take into account what your maintenance budget is and how often you’ll need maintenance work done. Some routine maintenance won't require a full-time role or even a contractor to accomplish, but any technical work should be left to the experts.
Develop a process for requesting and tracking equipment maintenance
Once you’ve identified who should own equipment maintenance, you should establish a way for workers to request maintenance if they notice a machine is not performing optimally. With the importance of maintenance baked into their KPIs and incentives, they can be your front line of defense. It’s important that the people you trust be given a way to make maintenance requests, because you or the person managing maintenance can’t always be present and looking at the machines. A machine operator knows their machine better than most, so they will be a great front line for detecting problems.
It’s up to you whether you want them to be able to submit requests directly or if they need to go through a supervisor. Each has its pros and cons. If you’re not going to give all your machine operators a way to directly request maintenance, you should have a clearly defined process in place for them to request maintenance from their supervisors. You also need to be sure that the supervisors or manager you choose have a solid process for denying, approving, and tracking requests. This process should minimize errors and the use of discretion. Also, you need to know how you will communicate to workers when maintenance is going to happen and what they should expect during that time. They might even have new ideas for how to make the most of that time.
Budget for routine maintenance of equipment
It would be a mistake not to budget for routine preventive maintenance, and an even bigger mistake not to budget for maintenance at all. The return on the investment in maintenance shows not only in the hard costs but in the avoided stress that an unexpected equipment shutdown can put on you and your workers. You can create this budget by pricing out the work that the routine maintenance of each machine will cost in an average year. Then add to the budget based on the expected likelihood that unexpected repairs are needed. You can do this by assuming the highest repair cost you would expect in the case of a total failure of the machine, and then divide this cost over the expected lifespan of the machine as stated by the manufacturer. That way you are ready for anything.
How on-demand labor can help with equipment maintenance
On-demand labor can help you with equipment maintenance by supporting the lead technician. With the support of the on-demand worker, your technician could finish the work more quickly and you would reduce the time required to complete maintenance and get back into your rhythm.
To learn more about on-demand labor, read our blog on what on-demand labor is and how your business could benefit from it.
Previous Posts
Trump 2.0 Week 14 Recap: Discussing The De-Escalation of the U.S-China Trade Conflict, New Deals With Key Trade Partners In The Works, and More
The Future of Manufacturing and Logistics
Create a free business profile today to explore our platform.
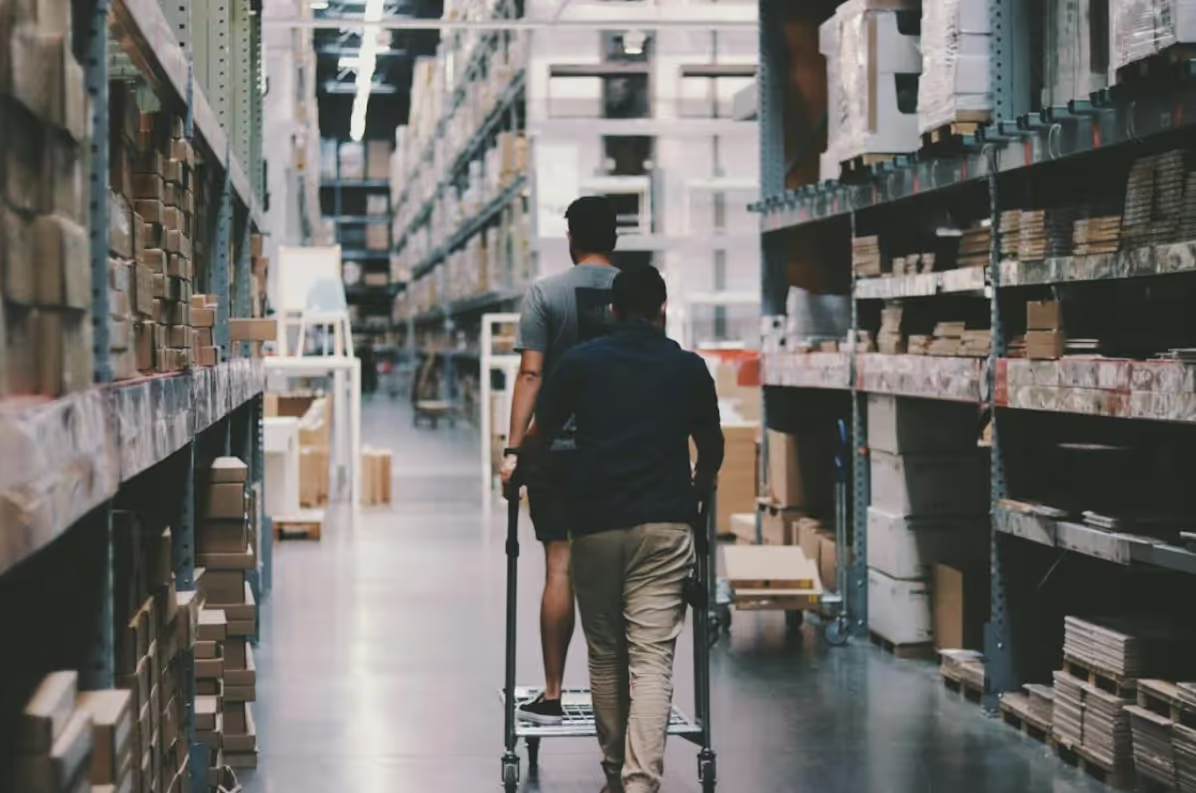