Digital Manufacturing
The last few years may have introduced more new capabilities into the manufacturing sector than most manufacturing practitioners will see in a lifetime. Many industry experts expect, as a result, that manufacturing will change more in the next five years than it has over the last 20 years. The change is being driven by a suite of new technology innovation from the Internet of Things to robotics to wearables. We refer to the use cases for this suite of enabling technology as Digital Manufacturing.
What is digital manufacturing
Here we will dig into the implications of technological breakthroughs on manufacturing labor, and what these breakthroughs are and how they are impacting the industrial environment.
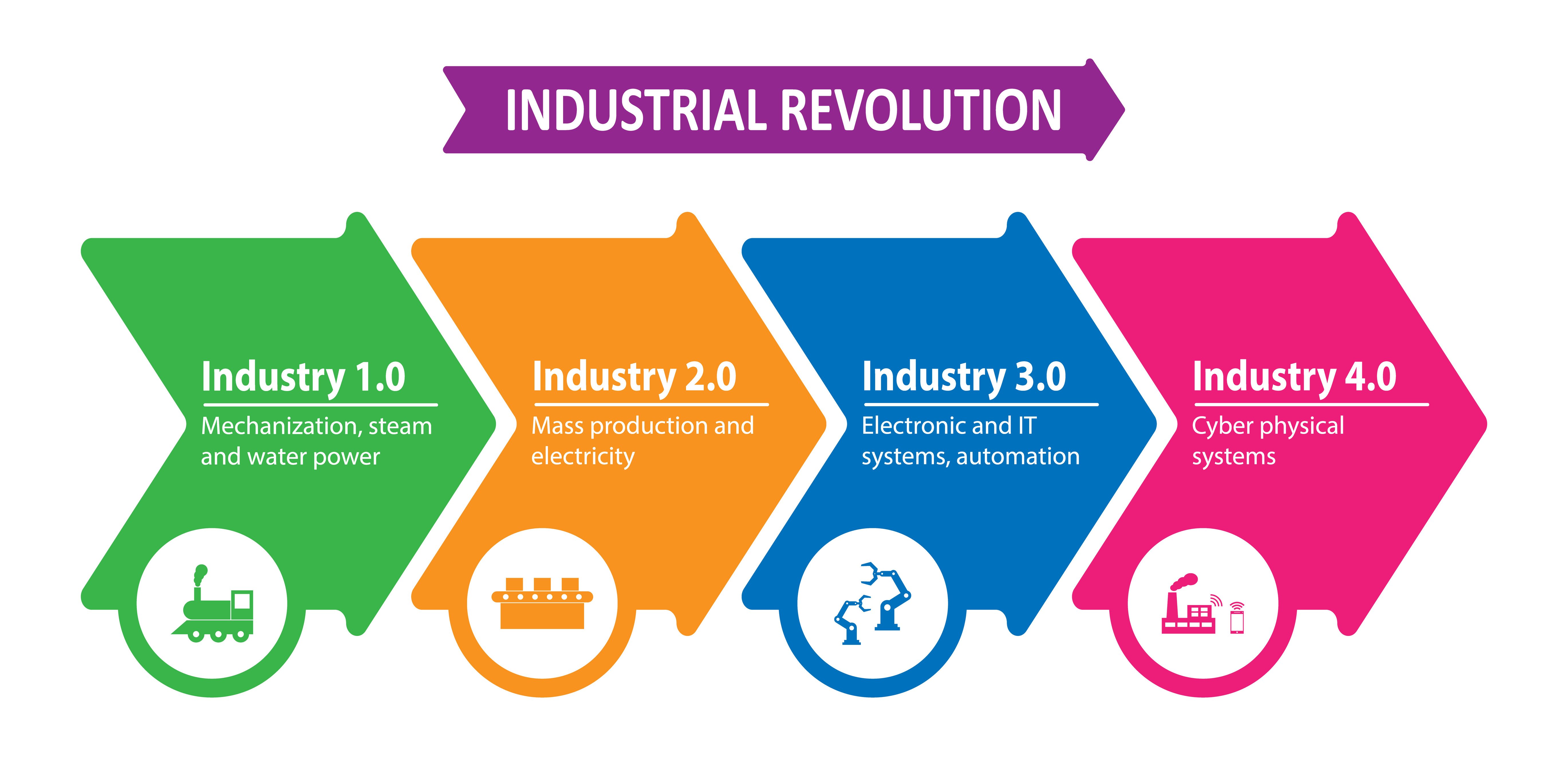
Undoubtedly you have heard a recent increase in the use of terms such as Internet of Things, the industrial internet, Industry 4.0, or simply digitization. These are all being thrown around to describe the overall emerging technology being adopted by companies to enhance product portfolios, provide new or better services, and/or improve internal operations. Buried within this landscape are specific capabilities that are converging to form the Digital Manufacturing category of use cases. As shown in the figure below, the spectrum of Digital Manufacturing elements can be broken down into four groups from broadest implications to narrowest: Connected Factory, Automation and Robotics, Additive Manufacturing, and Man-Machine Interaction.
.png)
In theory, a complete Digital Manufacturing solution would include aspects of all four of these elements, and many companies will be heading down this path within the next five years.
Which elements are having the biggest impact?
While much of the recent discussion out of Silicon Valley has focused on the implications of robotics, our experience and analysis points to Connected Factory as the biggest game changer. The Connected Factory essentially represents a controlled application of the Internet of Things within the four walls of the plant or across a network of plants.
With the emergence of cheaper sensing technology, data storage, track and trace capabilities, and data analytics, sites can have the ability to establish operational intelligence platforms that house and analyze all aspects of the manufacturing process in real time. The days of disparate and disconnected specialized systems (e.g., MES, WMS, CRM, etc.) are numbered. While these systems may still serve a purpose in the future architecture, they will merely be feeders into the operational intelligence backbone.
The number of specific use cases and value creation opportunities stemming from the Connected Factory are endless. With this comes the ability for operations managers to have real-time visibility to material flow, worker movements, inventory transactions, and machine performance. In addition, the machine learning capabilities will be able to reprioritize production sequences, send alerts to operators, digitally deploy work instructions, and proactively identify potential bottlenecks or quality issues before they arise without management intervention. These use cases all stem from the operational intelligence within the Connected Factory.
What is the value creation opportunity?
The Connected Factory is ushering in something unprecedented in the history of manufacturing: a large-scale redistribution of operational intelligence. Even in most of today’s production environments, much of the operational intelligence still resides with the individual operator. This is why training and structured onboarding processes are still high priorities for most businesses. The inefficiency with this historical paradigm is that individual operators only have a small amount of influence over the overall site operations, i.e., they can only optimize the variables that are within their control.
A recent study of ours concluded that the amount of non-value added labor activity at most sites is greater than 50% of total labor cost. Only a small portion of the non-value added cost is typically related to anything performance based – the real efficiency barrier is the inability to coordinate all the variables in the production environment to keep operators working efficiently. More often than not, they have to devote valuable time to find material, locate tools, re-sequence work orders, or consult with engineering. The Connected Factory directly addresses this overall coordination of all of these variables.
Now back to the redistribution of operational intelligence. Along with the capability to coordinate activities, the operational intelligence backbone becomes a massive repository for company intellectual property. It contains all product and production information, measures and analyzes performance, and deploys the information as designed. The implication is that harnessing and deploying this IP appropriately will enable a future state where individual experience and expertise are redundant, and potentially even counter-productive. This will have an enormous impact on how we manage manufacturing labor in the near future.
We will explore the labor implications, specifically, in the next blog in the Digital Manufacturing series.
Previous Posts
The Labor Crisis No One’s Talking About: Wasted Skill, Not Missing People
The Future of Manufacturing and Logistics
Create a free business profile today to explore our platform.
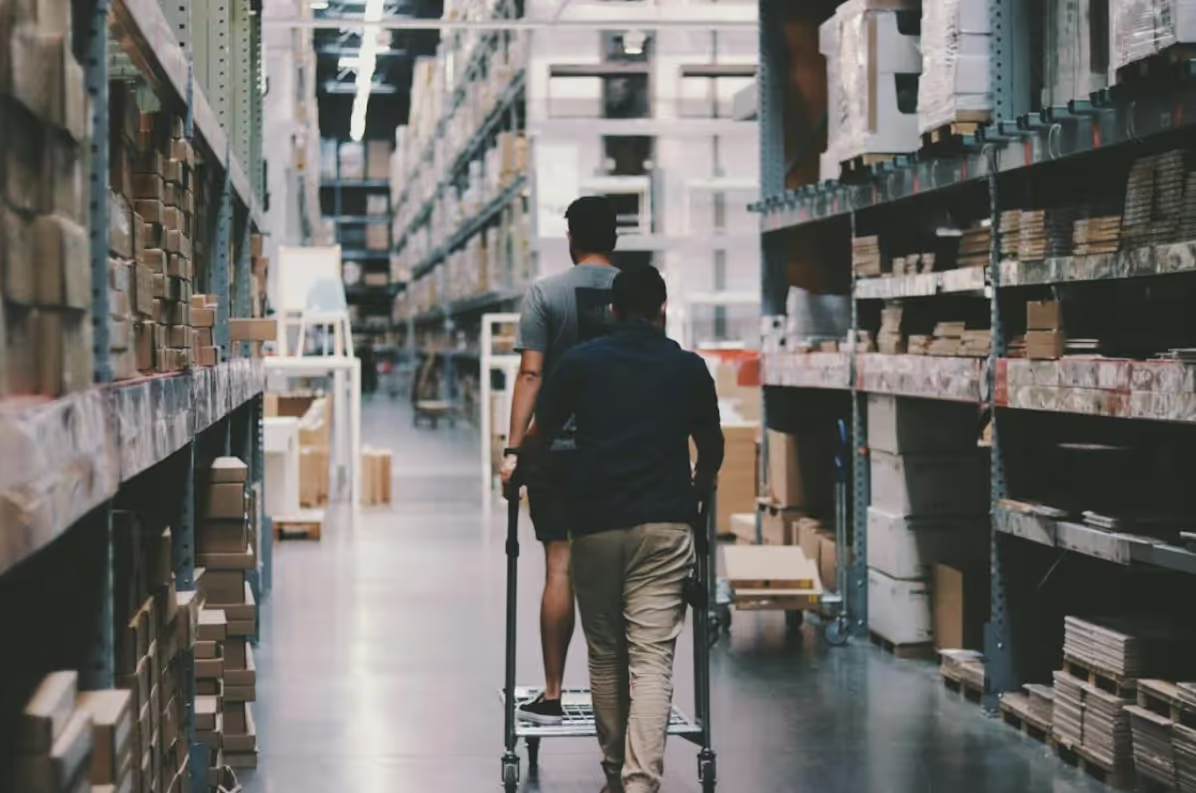