Capacity Constraints: Definition, Effects, and Solutions
You’ve found that some parts of your operation move more slowly than others. And you’ve done what you can to work around it. It might seem like common sense adjustments to you, but the topic goes deeper than it seems on the surface. There are entire methodologies built around getting rid of these pesky obstacles, and finding a common language for discussing these challenges can help you share your ideas and learn from others.
At Veryable, we address the capacity constraint of labor by connecting businesses to workers through our on-demand labor marketplace. This article won’t be about our solution. But we do have conversations with businesses all the time about their constraints and how they are addressing them, so we want to share what we know.
In this article, you’ll learn what capacity constraints are, the effects they have on your operation, and how to address them using a widely accepted methodology.
What are capacity constraints?
Capacity constraints, also known as bottlenecks, are steps or processes in your operation that are slower than the others. The bottleneck is a good analogy for a capacity constraint, because just like with a bottle of milk, no matter how big the rest of the bottle is, only so much milk can pass through the neck of the bottle at once.
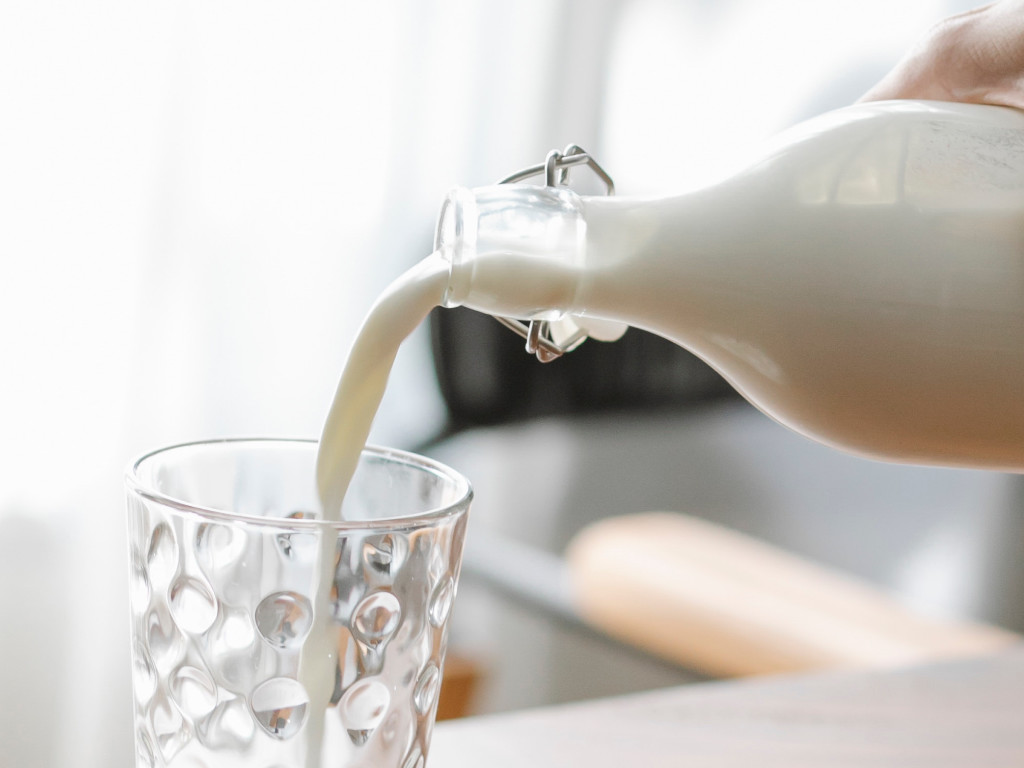
Capacity constraints can be caused by equipment, labor availability, labor productivity, material shortages, or lack of available space. It is helpful to focus on variables you have control over, which often leads to an emphasis on equipment and labor when addressing bottlenecks.
Effects of capacity constraints on your operation
Capacity constraints are always going to be there. If you ignore them, they can slow you down more than they should as the problems pile up.
Even if your whole operation is improving around the bottleneck, but you can’t figure out how to improve the bottleneck, all your improvements won’t have as great an impact as they otherwise could.
For example, let’s say you have one machine that can only output four parts every hour. The step before that machine in your process can supply the input for eight parts every hour. And the step after that machine can receive and process eight parts every hour. So you can see that the machine that outputs four parts every hour is only half as productive as the rest of your process. That machine is your bottleneck.
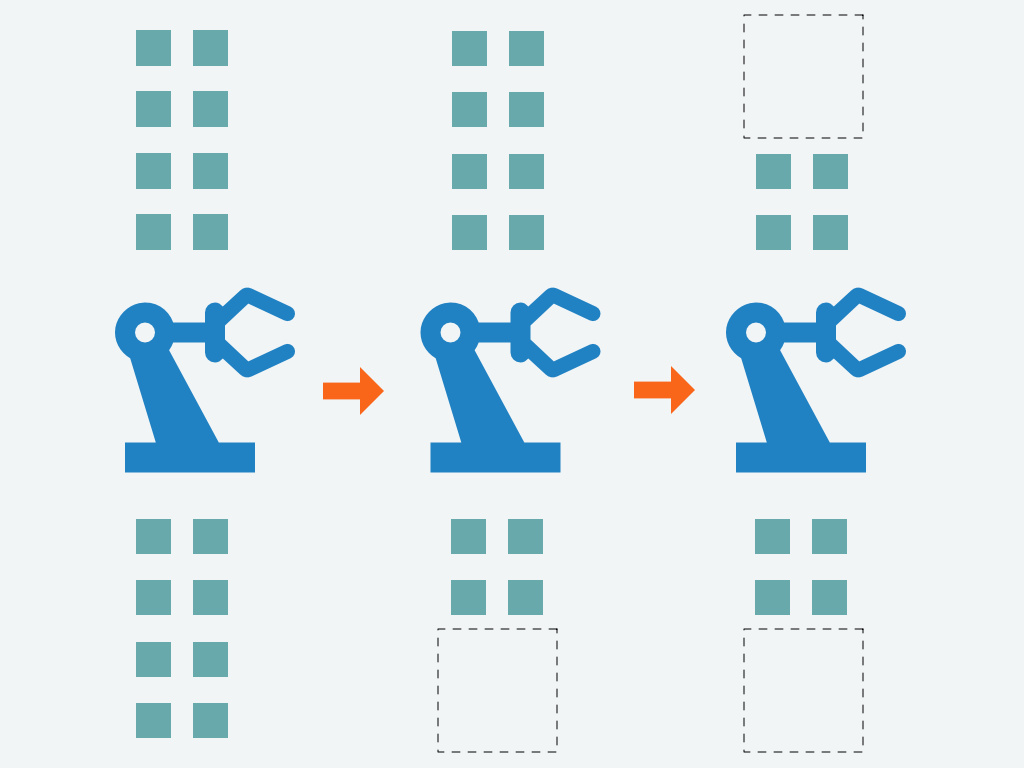
Now imagine that this bottleneck machine breaks down. You’ll have materials piled up and people standing around with nothing to do. Your operation will grind to a halt until this machine can be fixed, and it will take a long time to catch up to where you could be. That’s because your bottleneck will determine how quickly the rest of your operation will be able to process the backlog.
How to fix capacity constraints
Capacity constraints are a common problem, and there are many ways around this issue. One tried and true approach that many companies use was proposed by Eliyahu Goldratt in his book “The Goal.”
Goldratt’s Theory of Constraints outlines how to identify constraints, orient around them, make improvements, and repeat the process. To achieve this, there are five steps he proposes:
- Identify the constraint
- Exploit the constraint
- Subordinate and synchronize to the constraint
- Elevate performance of the constraint
- Repeat the process
To learn more about each of these steps, read our in-depth guide to breaking bottlenecks by applying the Theory of Constraints.
To learn more about how the Veryable solution can help you eliminate capacity constraints, check out our most recent article: Taking Control of Your Daily Capacity Challenges
Previous Posts
Hidden Inefficiencies in American Manufacturing and How that Impacts Capacity & Consumer Prices
The Future of Manufacturing and Logistics
Create a free business profile today to explore our platform.
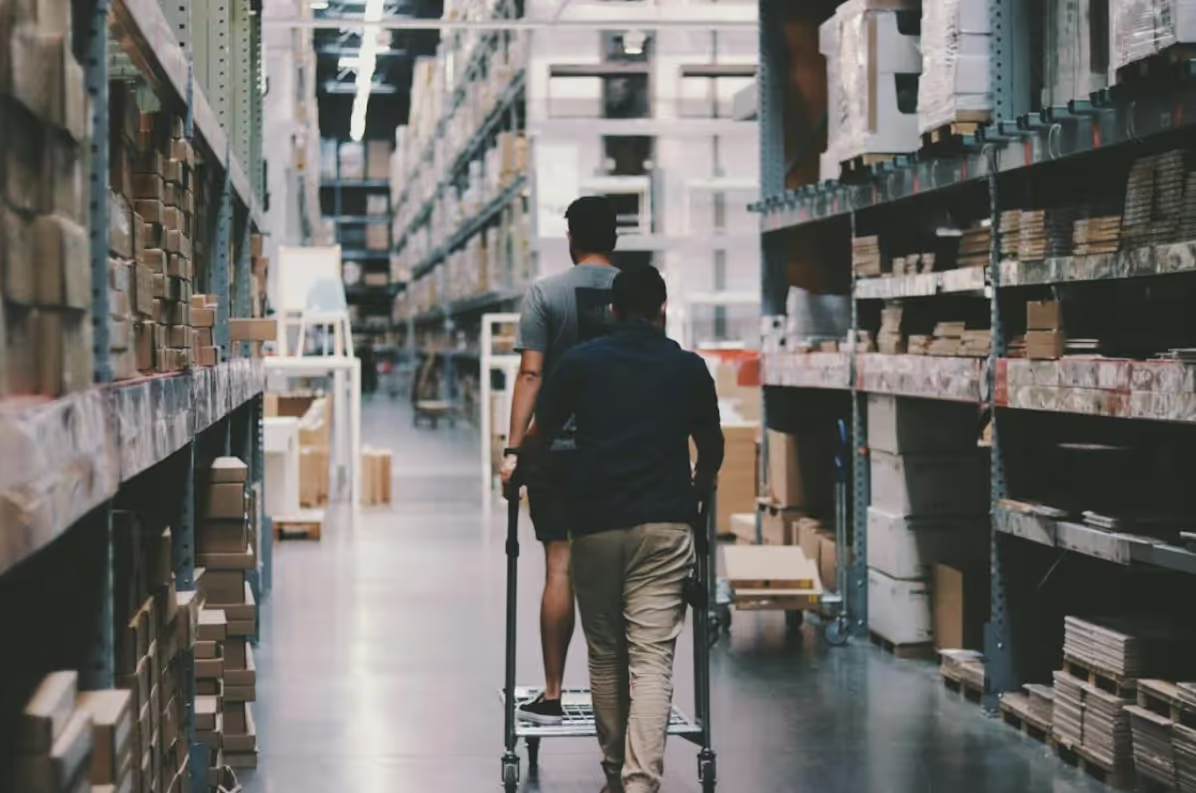