Benefits of US Manufacturing
Reshoring is a hot topic due to the shocks to the supply chain over the past few years. Maybe you’re considering reshoring, but aren’t sure if it will be worth the trouble. What are the benefits of reshoring which so many people are saying you should be doing?
At Veryable, our mission is to revitalize US manufacturing. Naturally, we’re interested in evangelizing the benefits of US manufacturing to anyone who will listen and even those who won’t.
In this article, you will learn the benefits of US manufacturing, why some companies aren’t reshoring, and how you can become more competitive while you reshore production.

Top Benefits of US Manufacturing
1. Improves customer service
2. Shortens lead times
3. Reduces delivery costs
4. Engages the US workforce
5. Stimulates US economy
6. Strengthens US independence
1: US Manufacturing improves Customer Service
Dissolving dramatic differences in time zones and language barriers will improve the effectiveness of your interactions with suppliers and customers. Reshoring to the US will improve the service you can give to your customers because feedback will be quicker and is likely to have less language barriers. This makes iterating on product design faster, and improves customer satisfaction.
2: US Manufacturing Shortens Lead Times
By removing reliance on overseas shipping, reshored US manufacturers enjoy shorter lead times, allowing them to carry lower inventories and deliver faster than their competition. In a marketplace where two-day delivery has become the norm, positioning yourself against quick competitors is more feasible and profitable with a local manufacturing footprint.
3: US Manufacturing Reduces Delivery Costs
Manufacturing in the US reduces delivery costs for US manufacturers. Local production removes the reliance on freight costs, which have hit record highs in recent years.
Traveling a shorter distance from the production line to the customer will cost less than shipping the product from overseas. This comes with the added benefit of reducing the risk of goods being damaged in transit, thereby reducing the number of replacements and refunds you have to make.
4: US Manufacturing Engages the US Workforce
US Manufacturing engages the US workforce, providing meaningful work opportunities and bolstering the economy. When more local workers get involved, the money tends to stay local. This builds up communities by stimulating local economies through local spending and reinvested local taxes.
5: US Manufacturing Stimulates the US Economy
Manufacturing is good for the US economy. More workers getting involved in meaningful work with tangible outputs produces a boon to local communities and shifts tax dollars from overseas back to within US borders. With more of the results of the hard work being retained by the local community and the US as a whole, US manufacturing is an improvement for the nation’s economy and wellbeing.
6: US Manufacturing Strengthens US Independence
US manufacturing capabilities are a matter of national security. On the world stage, being able to position oneself as a nation state with strong productive capacity is not only a signal of economic strength but an indication of potential military strength. Borrowing the words of former President Theodore Roosevelt, this is one way we can “speak softly and carry a big stick.”
Why Doesn’t Every US company Manufacture in the US?
Over the past few decades, companies have overextended the globalization trend as executives sought short-term wins on their key metrics while ignoring the externalities and impacts to long-term profitability caused by offshoring key business activities.
Making things in other countries with looser regulations and cheaper labor might have worked for some companies in the short-term, but the hidden effects of this strategic blunder have reared their ugly head in the wake of the pandemic and the world’s reactions to it. The stresses of 2020 have rolled over well into 2022, revealing a fragile global supply chain that had been running hot without a safety valve for too long.
What had been swept under the rug has come to light as companies see the true costs of removing work from the US through outsourcing, offshoring, and otherwise avoiding engaging with the local workforce in a mutually beneficial arrangement.
Since companies have reduced their onshore capacity, they face large expenditures to build productive capacity onshore.
Another big reason why many US companies still aren’t reshoring is labor costs. American workers demand higher pay, so companies either have to function with less workers, raise prices, cut profit margins, or think outside the box.
One way of thinking outside the box to address the relatively high labor costs of producing in the US is an operations-focused solution like on-demand labor.
How to be More Competitive While Reshoring Production to the US
You know by now that the long term benefits of reshoring are huge, but what about the short term? It can be expensive to reshore in the worst case, and in the best case it will create some extra work across your company. But there are ways to maintain and even increase competitiveness during the transition from offshore to onshore production in the US.
When you reshore production, you will have to find a new facility locally and find local workers to meet demand. With new innovations in additive manufacturing, you might consider shifting to a decentralized production model to double down on the localization effort you’re making by reshoring.
At first you might groan at the thought of having to staff a facility in today’s tight labor market. But this is an excellent opportunity to embrace a new, flexible labor capacity model which sidesteps the struggles of staffing and looks at labor in a new way.
An on-demand labor model will ease the transition as you reshore, while also setting you up for long-term success. With an on-demand labor model, you can hire the minimum number of full-time employees (FTEs) you need to meet demand on a slow day, then use on-demand labor to meet any daily demand that arrives over that minimum. With infinite flexible capacity, your hiring woes are gone and you can focus on achieving operational excellence.
Using flexible labor capacity, you can further leverage your shorter lead times, lower inventories, and lower cost of transportation you gained by reshoring. Get started building your flexible labor capacity today by creating a free business profile on Veryable’s on-demand labor marketplace.
Previous Posts
Trump 2.0 Week 14 Recap: Discussing The De-Escalation of the U.S-China Trade Conflict, New Deals With Key Trade Partners In The Works, and More
The Future of Manufacturing and Logistics
Create a free business profile today to explore our platform.
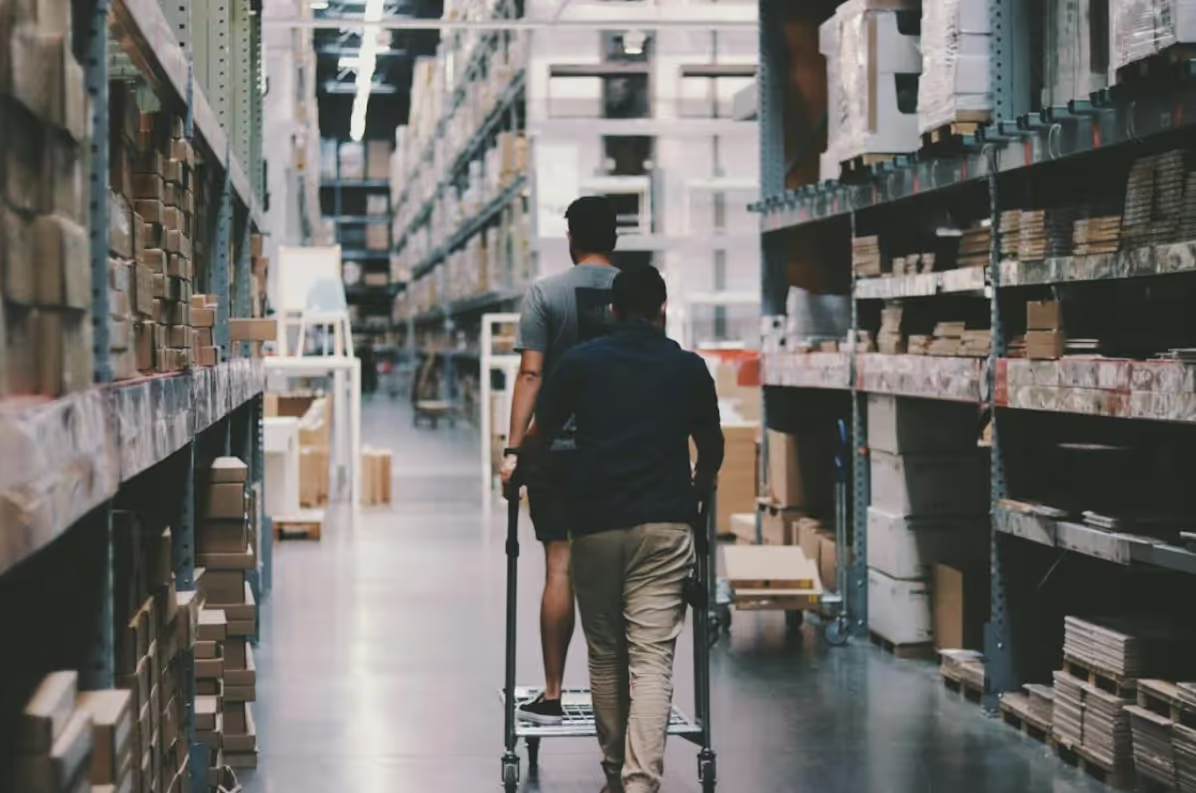