Customized Distribution Services
Esteemed 3PL provider Customized Distribution Services increases speed & efficiency while cutting costs with an on-demand labor pool
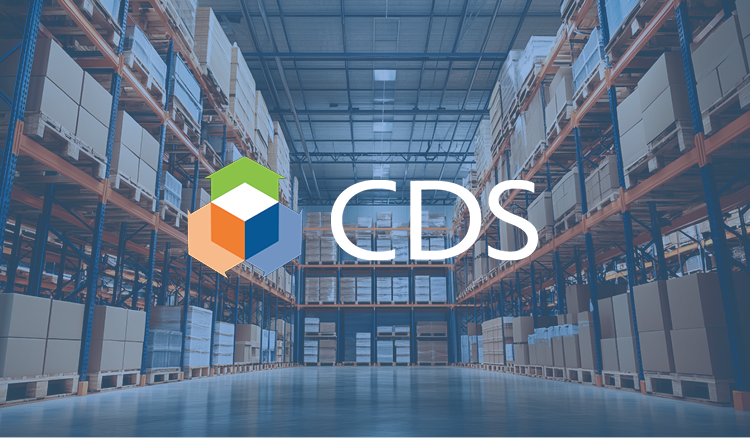
Customized Distribution Services (CDS) Increases Inbound Receiving Speed While Reducing Overtime Expenses With Veryable
"Veryable gave the operation more flexibility and has allowed us to be able to react to demand more efficiently"
-Christopher Couture, GM, Customized Distribution Services
Setting the Stage
Back in early 2022, the world was dealing with the lingering effects of the COVID pandemic and a rapidly accelerating supply chain crisis. As a result, companies across the logistics industry were forced adapt to a new set of challenges.
Customized Distribution Services, a 3PL provider for Henkel, Pepsico, Westrock, and many other big names around the country was dealing with a significant backlog of over 100 trailers in the yard at one of their St. Louis, MO area distribution centers. Their ability to tackle this challenge was inhibited by the tough labor market in the area, and they were having to rely heavily on expensive overtime and temp labor to keep up.
In February 2022, Edwardsville Distribution Center GM Chris Couture met with the Veryable team to address some of these issues.
Solution
CDS began posting ops to address their inbound trailer backlog, and within just a couple of days, Veryable operators had alleviated this issue, allowing the CDS team to begin tackling other inefficiencies within their operations.
After developing a procedure and solid rhythm with the Veryable platform, the CDS team began posting weekend ops, and soon after that, the team started using Veryable operators for night shifts as well. By May, CDS had assembled a “sideline bench” of roughly 50 trained operators that had worked in the facility and could be flexed in as needed.
The month of June saw a considerable boost in Veryable usage. Demand spiked towards the end of Q2, and the facility went from needing an average of 15 operators per day to over 40. Higher volume persisted throughout the month of July, and their labor pool soon reached over 100 operators. CDS's Operation Managers shared with the Veryable team that without their labor pool, they wouldn’t have been able to keep up with higher demand.
One of the main advantages of the Veryable model is having the ability to scale down instantly as needed. In August, volume at the Edwardsville facility dropped significantly. With Veryable however, CDS was able to scale down instantly to protect profit margins without the need for any layoffs.
Results
Speeding Up Inbound Receiving
One of the key issues CDS was dealing with prior to using Veryable was their inability to receive and process inbound shipments on time. Prior to building a labor pool, the rate of inbound trailers received on time was just 44.3%. Now the rate is sitting at around 80%, a 35.7% increase.
Dwell Time Reduction
One of the other core issues impacting CDS’ success was high dwell times. Prior to building a labor pool, there was an average of over 62 times a week when drivers had to wait more than two hours or more to unload their trailers. Now with the ability to scale each day to the precise level of support required, dwell time has dropped by roughly 38%.
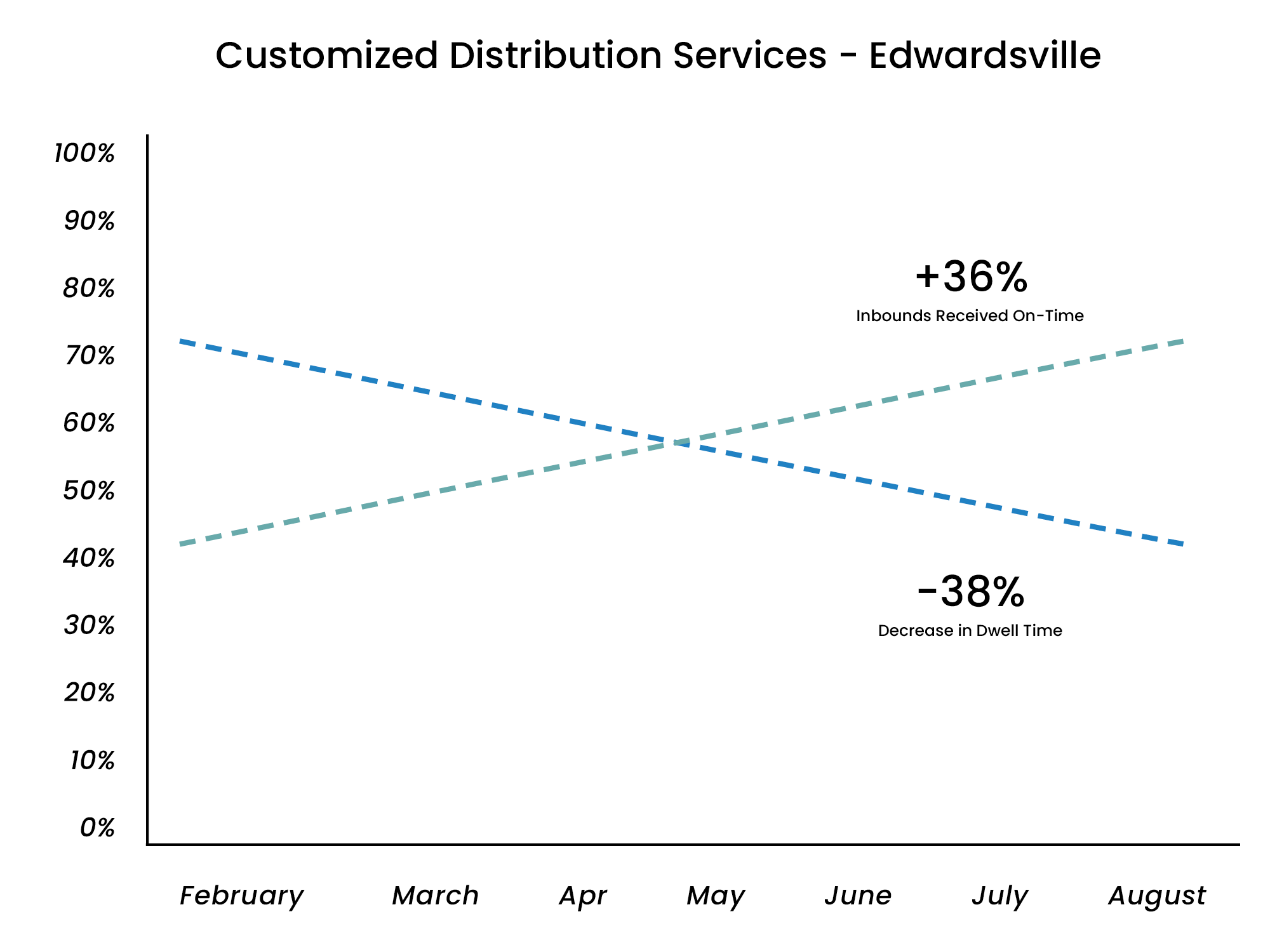
See Veryable for Yourself
Create a free business profile today to explore our platform.
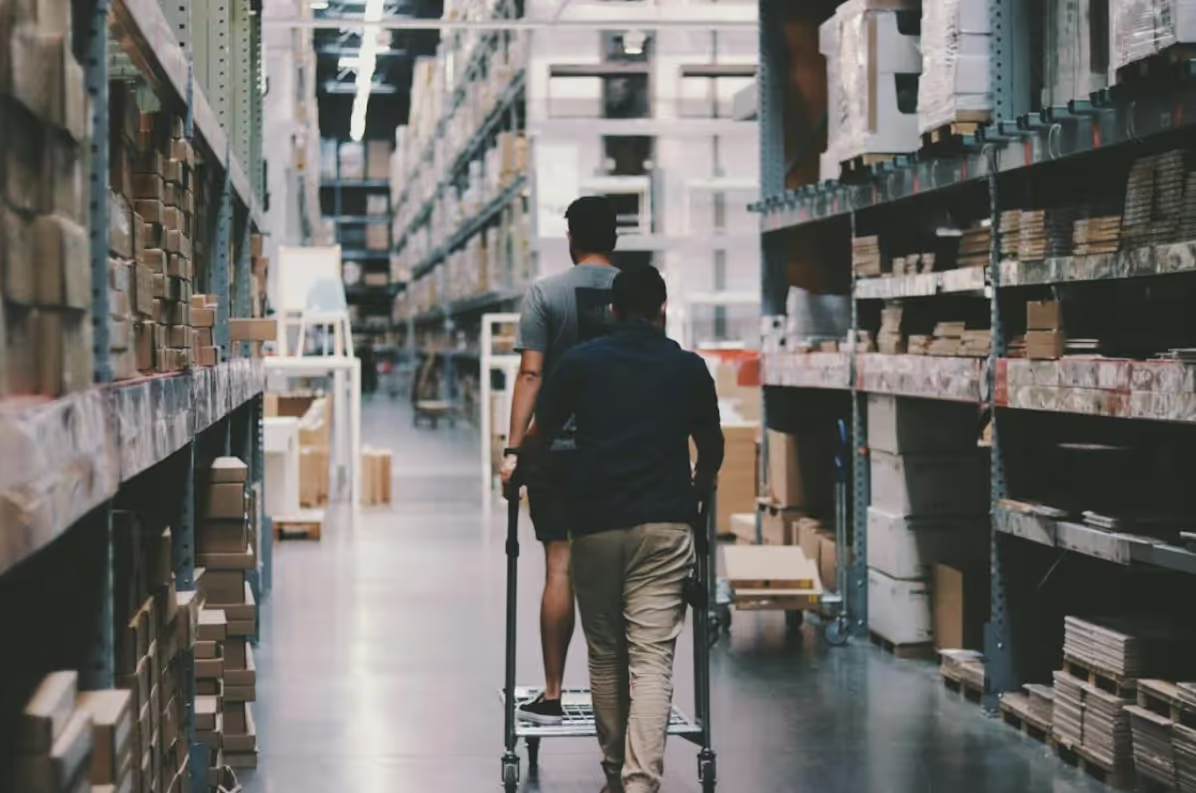