ADAC
Weathering the Storm: ADAC Automotive finds new operational speed and resilience with Veryable
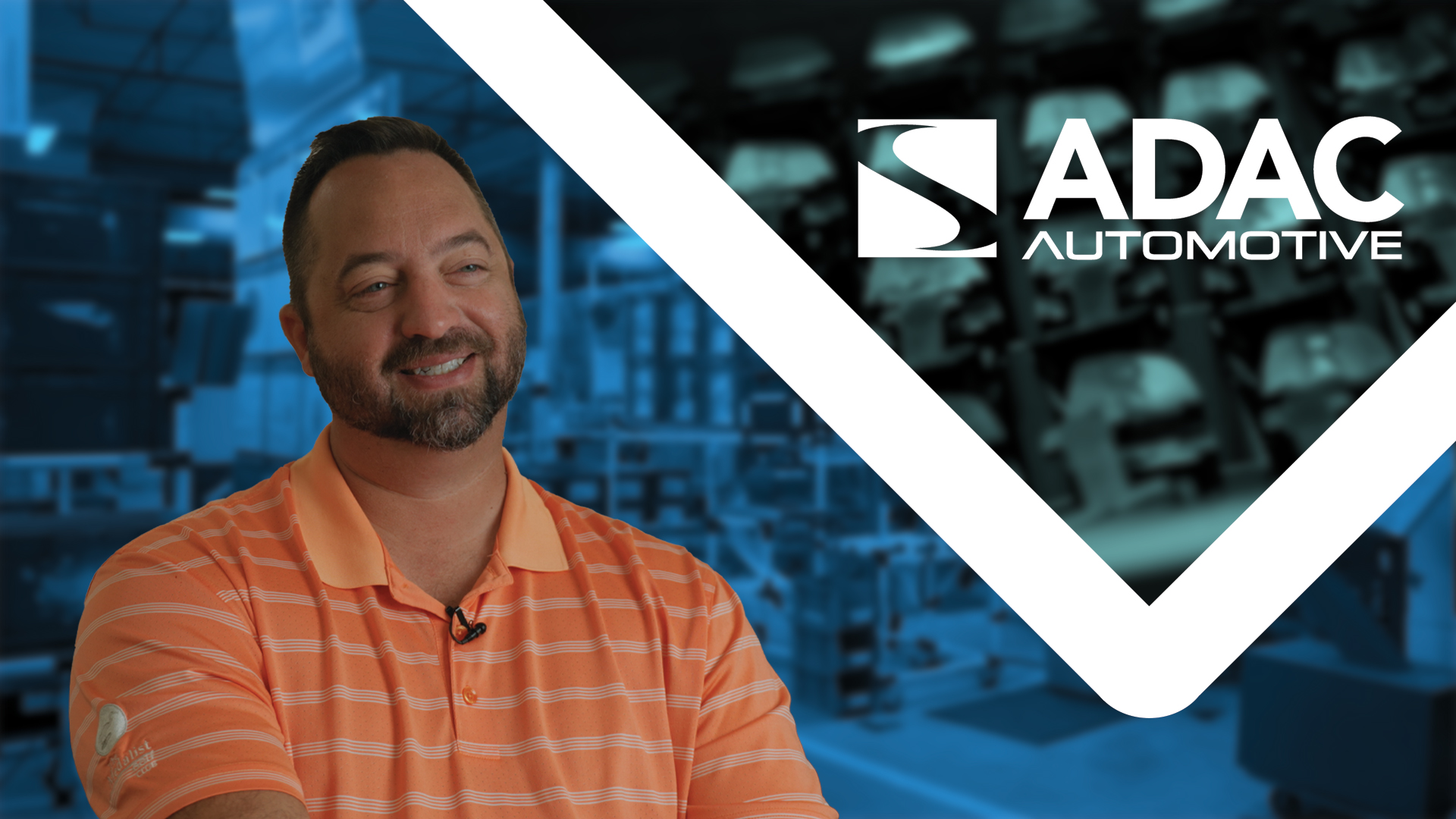
Weathering the Storm: ADAC Automotive finds new operational speed and resilience with Veryable
ADAC Automotive, one of the leading automotive parts suppliers in the industry, faced a pivotal challenge - predicting staff requirements to meet the fluctuating demands of their diverse clientele, which includes giants like Ford, Stellantis, General Motors, Honda, Nissan, Volkswagen, and BMW. The unpredictable nature of the industry made it almost impossible to accurately forecast labor needs on a weekly, monthly, or yearly basis. Over or under-staffing often led to increased overheads or missed delivery deadlines. The team at ADAC knew there had to be a better way. Enter Veryable.
Building the Operational Arc
Understanding the need to adopt a different labor strategy to overcome automotive industry challenges, Veryable had already become a name synonymous with operational excellence in short notice scalability. ADAC had a relationship with Kendrick Plastics who we had just completed the News Nation video with Veryable and used their experience as the credibility they needed to launch with Veryable. ADAC found exceptional value in using Veryable to manage varying labor demands with ease. ADAC jumped head first into building their labor pool by utilizing the platform at 3 different manufacturing plants in many different work areas, developing a dynamic labor pool in about 2 months. They could schedule operators precisely when needed, avoiding unnecessary overtime costs and improving staff retention by preventing burnout from continuous long-hour shifts. "We still have to get parts out the door and meet our commitment to the customers. And that's where right now we see the most value with Veryable is closing that gap," said Jake Rupert, ADAC's Head of HR.
Just In Time Scalability
Veryable's value became exceptionally clear when ADAC found itself in dire need of additional labor. Faced with the challenge of needing additional staff for a shift starting as early as 7 am, ADAC turned to Veryable. "If we start the day at seven am, and we realize that we don't have enough labor on first shift to to get parts out the door, that means we need to try to reinforce second or third shift, that traditionally you don't have those opportunities to bring in talent on a same basis, we did it with Veryable the first time we tried it," said Jake. ADAC gained the ability to quickly find skilled operators, often with just a three to four-hour lead time, and became a lifeline for ADAC, ensuring smooth, uninterrupted operations, and more importantly, enabling them to meet customer delivery deadlines.
Leveraging Advanced Tools for Optimal Efficiency
In addition to flexibility, Veryable also offered a pool of experienced manufacturing workers ready to integrate seamlessly into the ADAC team. The platform's advanced tagging and filter system enabled ADAC to quickly identify and choose individuals with specific skills or prior experience in certain departments. This feature amplified efficiency, as workers could get straight into the job with minimal training, ensuring optimum productivity levels. "it's been pretty smooth on transition, and they've gotten along really well with the, I guess, full-time operators that we have on staff. There are a couple of them that I've actually worked here before," said Jared McFarland, Team Lead at ADAC.
Furthermore, the Veryable platform provided insightful performance metrics. This data empowered ADAC to understand the real impact of their investment in the platform, providing clear visibility of savings and other operational enhancements achieved. "Having that baseline data can tell me as a business professional, what's my impact, what's my savings, and how else are we providing value," said Jake.
Weathering the Storm: Minimizing Strike Disruptions
Since then, they have had the benefit of a highly-skilled, repeat operator base that has given them the ability to mitigate some of the impacts from the 7-week UAW strike and maintain the flexibility to scale back quickly when work resumed with OEMs. Due to the changing nature of automotive platforms, especially as technology develops, having the ability to accommodate shifting customer requirements is critical to being a preferred manufacturer. Veryable has enabled them to move forward no matter the work knowing they have skilled operators available for any of those challenges.
ADAC's experience with Veryable truly underscores its versatility and flexibility in meeting labor needs in a tough, unpredictable industry. Any business grappling with similar labor challenges can consider giving Veryable a try. As in ADAC's case, you might find it to be the perfect solution to bolster your labor force efficiency and productivity, thereby ensuring a successful business operation.
Veryable Receives Innovation Award at ADAC Automotive Partner Day
In May 2024, ADAC hosted their annual Partner Day Event where they recognized more than 75 different suppliers they work with. Veryable received the Innovation Award for helping ADAC to mitigate $400k in automation costs and achieve $1.6M in total cost avoidance throughout the length of the UAW strike. Measuring this impact was made possible by the insightful performance metrics provided by the Veryable platform. To read more about this, click here.
A Closer Look: Scaling with Demand
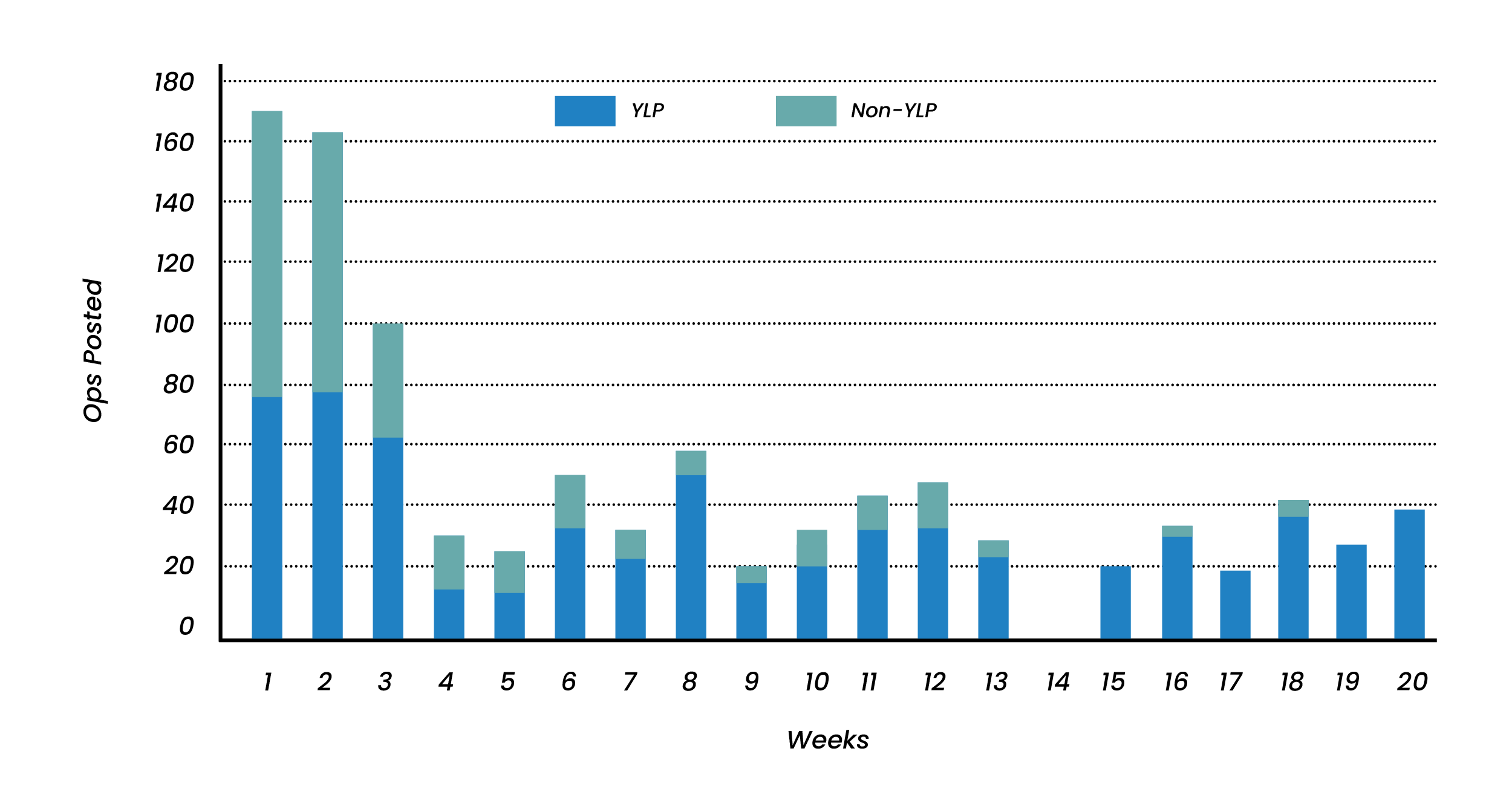
See Veryable for Yourself
Create a free business profile today to explore our platform.
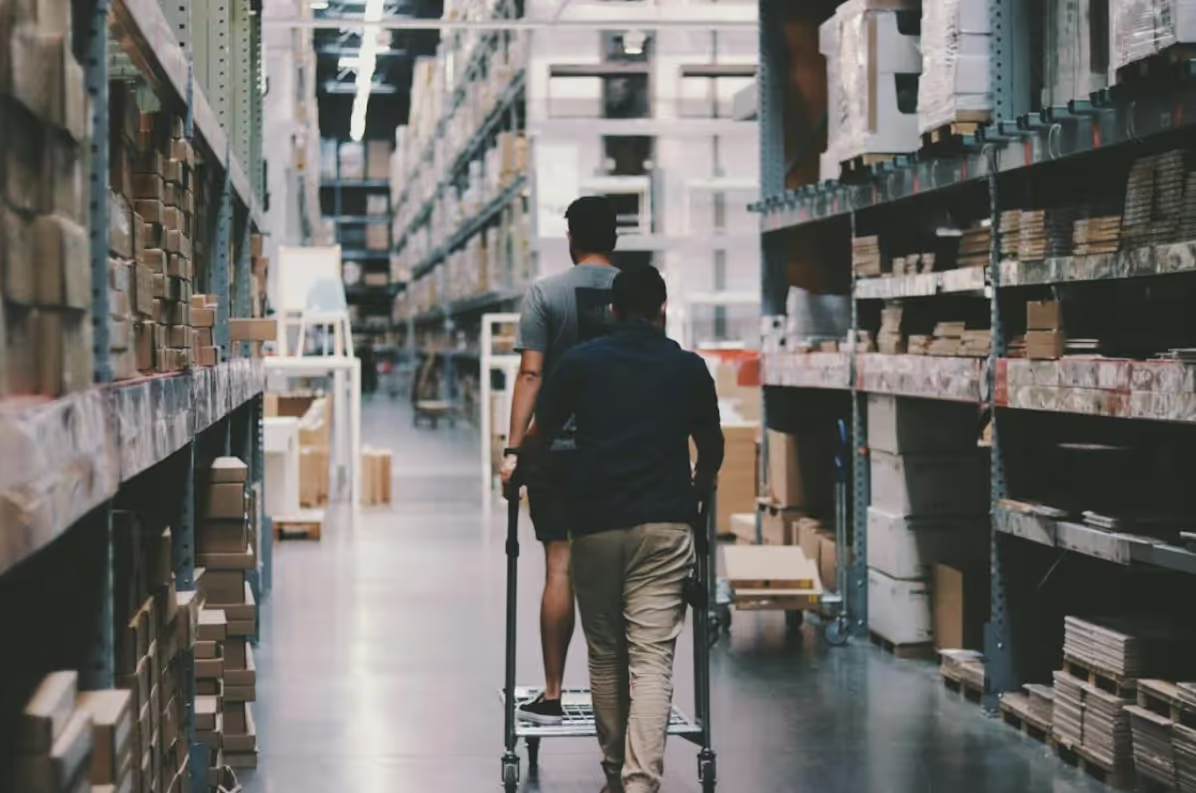