What is Kaizen?
Kaizen is a term you’ll hear thrown out casually in conversation with many manufacturing leaders. If you’ve been using context clues to get by this far, you’ve likely figured out that it has something to do with always improving. So what exactly is kaizen, and why are people talking about it?
Veryable is on a mission to revitalize US manufacturing through Lean tools like kaizen and our on-demand labor marketplace, which enables companies to flex their labor capacity in real time.
We won’t focus on our solution here. Instead, we’ll use this article to educate manufacturing companies like yours on kaizen, a time-tested Lean tool available to you for improving your operations.
In this article, you’ll learn what kaizen is, how kaizen thinking benefits your operations, and how to conduct your own kaizen events.
What is Kaizen in Lean Manufacturing?
Kaizen is the mindset of continuous improvement and the systematic identification and execution of improvements. It is commonly viewed as a commitment to making incremental improvements every day, similar to the refrain that if you get one percent better every day, soon you will be a master of your craft.
Kaizen is both a philosophy and an action plan consisting of kaizen events. Like other Lean tools, the kaizen mindset is just as important as the actions taken based on that mindset. You can read more about each aspect of kaizen below.
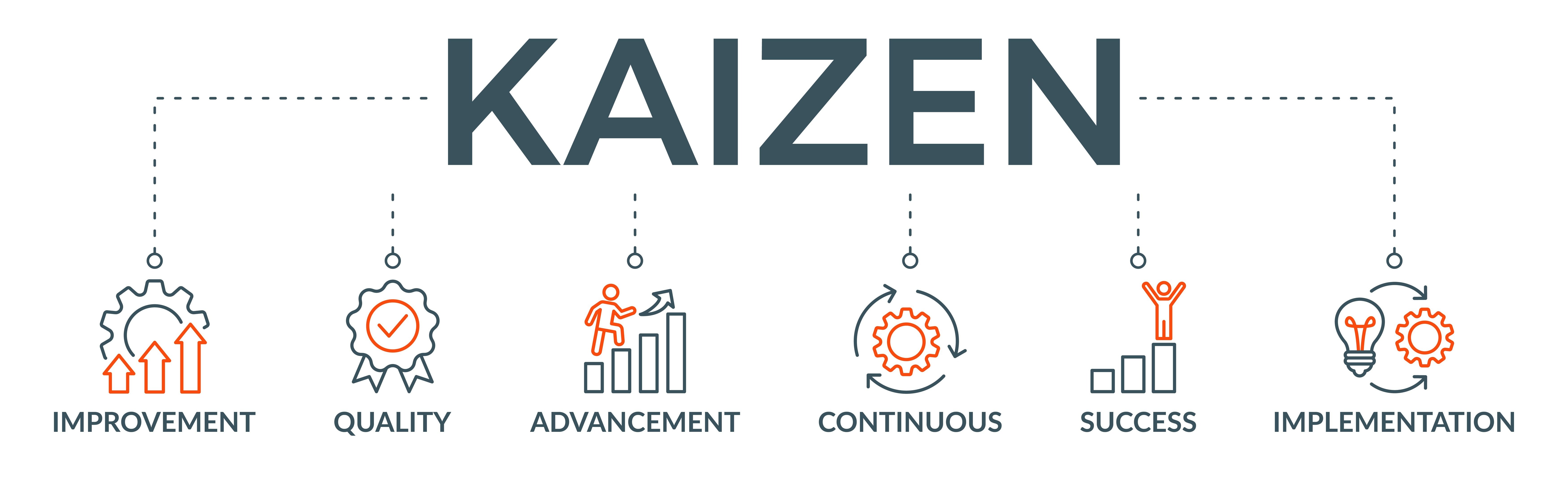
What is the Kaizen Philosophy?
The kaizen philosophy is the continuous search for opportunities to improve. The ideal end result of kaizen is the elimination of waste at its root cause whenever waste is identified.
Each kaizen practitioner (i.e. each worker in your company) must take ownership of their processes and follow a scientific method to identify, execute, and evaluate improvements in the pursuit of quality and efficiency.
Kaizen emphasizes the improvement of processes and equipment in a standardized and documented manner. Standardization and documentation enable you to compare your efforts to prior performance so you can properly evaluate the improvements you’ve attempted.
In kaizen, every improvement must be in service of the end goal of reducing various types of waste, as defined in the Lean methodology, to improve the value flowing to the customer.
What are Kaizen Events?
Kaizen events are defined periods of collaborative effort to address larger areas of needed improvement to the value stream. Because kaizen is a continuous effort, smaller improvements do not qualify as kaizen events.
During a kaizen event, your team collaborates to get to the root cause of whatever issue is preventing your team from reaching the goals you’ve set.
Common issues that are addressed during a kaizen event include:
- Cross-functional challenges that slow the flow of value
- Machine issues impacting the value stream
- Process issues impacting the value stream
- Low kaizen adherence among team members
A kaizen event typically lasts one or more days, whereas typical kaizen improvements can happen any time and take just a few minutes or hours to implement.
Steps to Implementing Kaizen Events
Kaizen events are typically one intense cycle of plan, do, check, and act (PDCA). It is a working session, not just a planning session. Kaizen events should happen on the shop floor, where the work you’re improving happens on a daily basis.
To succeed, kaizen events require planning and coordination. Some kaizen practitioners advise that a majority of the time spent on a major kaizen event be spent preparing and then reviewing the effects of the kaizen event. One example is the nine-week cycle, which consists of four weeks of preparation done by the facilitator, one week conducting the kaizen event itself, and then four weeks of monitoring the impact.
The main steps of planning for a kaizen event are as follows:
- Appoint a leader for the kaizen event
- Determine the scope of the kaizen event
- Strategically construct a team for the kaizen event
- Define your goals for the event
- Outline the event schedule
Once you have planned your kaizen event, you are ready to perform your PDCA cycle. You will follow these four steps if you are using the PDCA cycle:
- Plan - Identify the problem, measure your baseline, and establish a goal for your improvement to accomplish.
- Do - Execute your solution that addresses the root cause of the problem you identified during planning.
- Check - Compare the results of your solution with the results you were aiming for.
- Act - If the changes produced the desired results, standardize the changes across your company to reap the rewards. This will serve as your new baseline for the next PDCA cycle.
Another way to organize your event would be a six-step process consisting of the following:
- See and quantify the waste
- Analyze the potential for improvement
- Identify and rank ideas for improvement
- Perform rapid experiments to help with implementation (these could be small-scale, rapid PDCA cycles like the above)
- Implement and measure outcomes
- Create standards
This repeatable process will form the basis of your kaizen events, and should also be ingrained in the culture of your workplace so that workers use the PDCA method daily. Remember, kaizen should be happening all the time, not just when you’re holding a kaizen event.
Supercharge Continuous Improvement with On-Demand Labor
When you’re conducting a kaizen event, you have to pull workers off the line to participate. On-demand labor can support your workers during kaizen events so that you can stay productive. Or, you could add a swing shift and pull from your on-demand labor pool to make up for lost time.
Plus, matching your labor capacity to demand is a way to continuously improve in its own right. You know how tough it is to keep the right number of people in the building, and you know the consequences of having too few or too many.
With on-demand labor, you can make incremental adjustments to take on incremental work.
For more information, visit our Lean Center of Excellence Homepage or our homepage for Continuous Improvement, Operational Excellence, and Lean Professionals.
Previous Posts
Trump 2.0 Week 13 Recap: Discussing Ongoing Negotiations With Key Trade Partners, A Potential Deal With China On The Horizon, and More
The Future of Manufacturing and Logistics
Create a free business profile today to explore our platform.
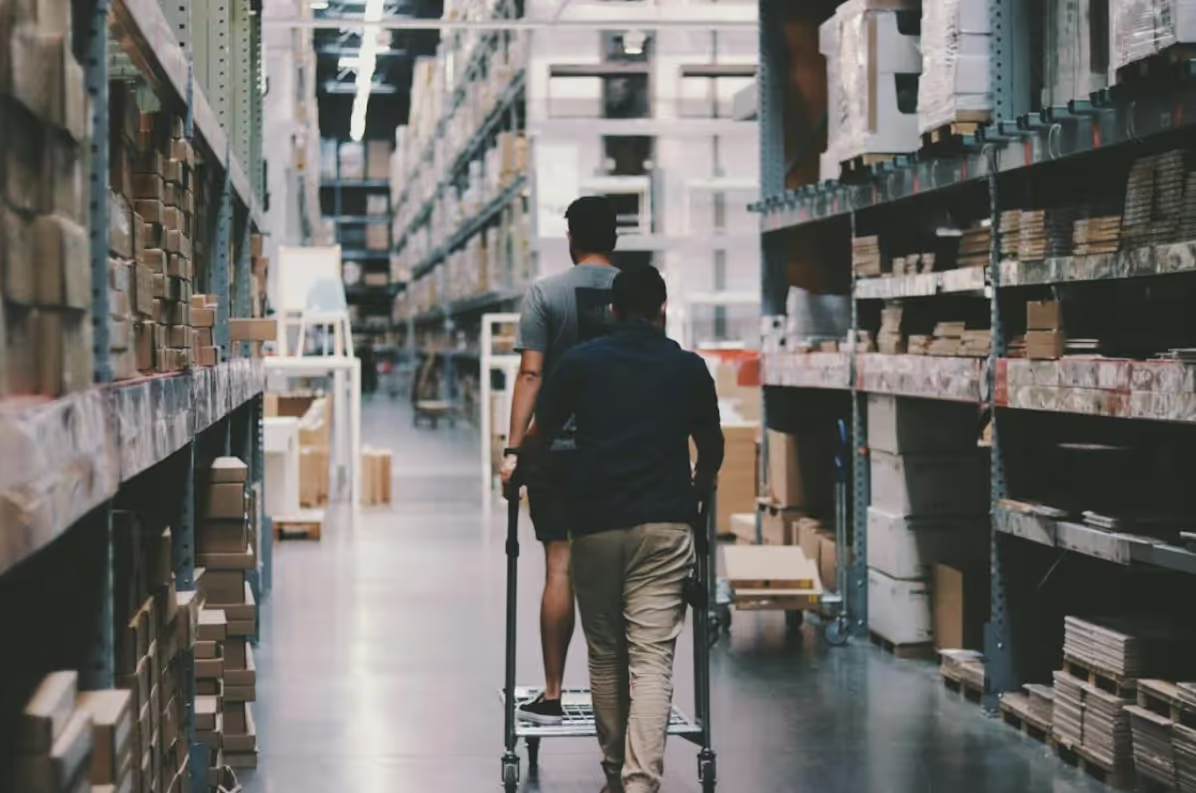