Unplanned Shutdowns: A Solutions-Based Approach
Navigating through an unplanned shutdown can feel like being lost in a complex theme park, with this looming, ominous red arrow on a demand curve map pointing right at the bottom where you stand. It reads, “You are here.” Although unsettling, it's essential to remember that this phase, though challenging, is temporary. The key is to be prepared to move forward because customer expectations and releases are not going to stop and wait.
In this article, we’ll delve into the potential of on-demand labor as a viable solution to not only recover from the current shutdown but to build operational resilience and down-cycle agility for the unforeseeable future.
Overview
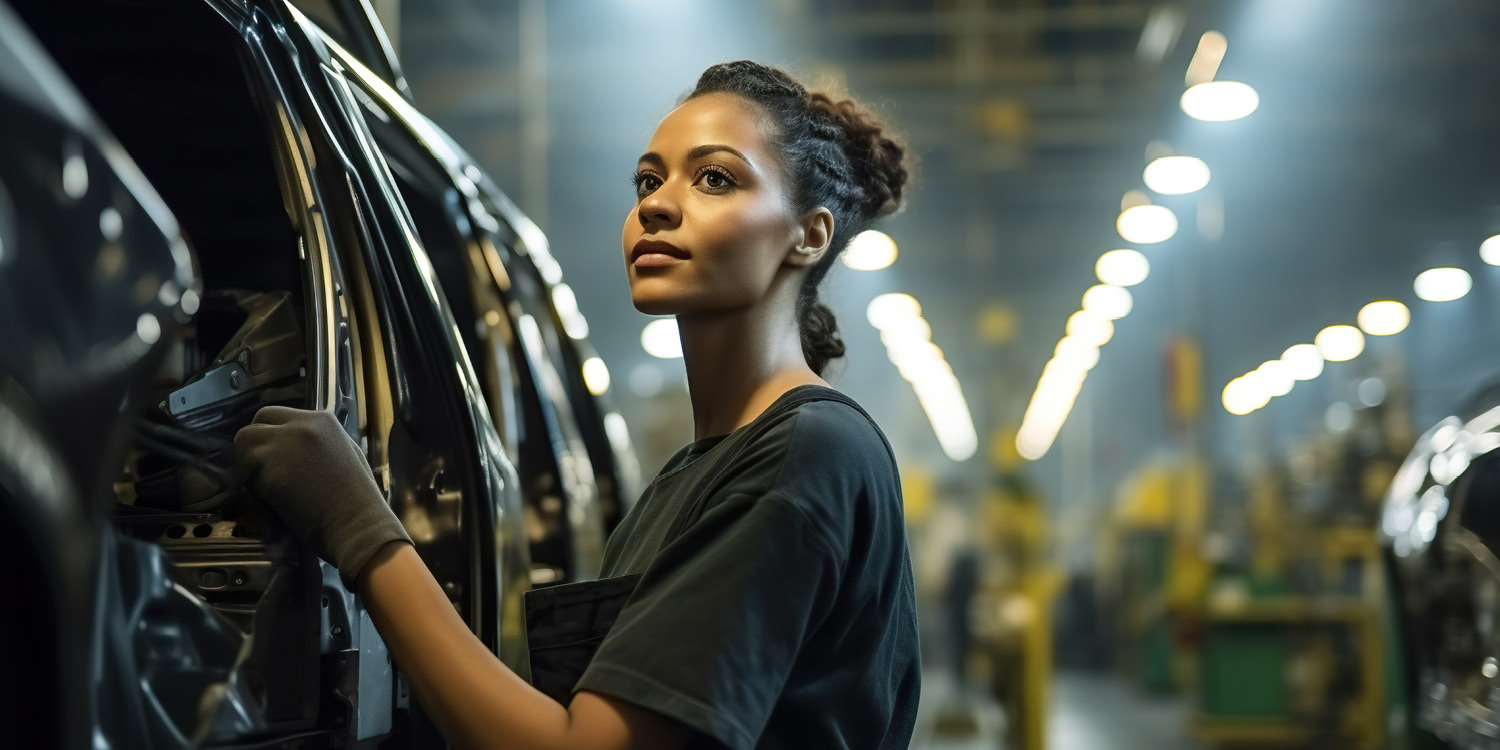
The automotive supply chain is currently navigating through a phase of unplanned shutdowns that have temporarily disrupted operations. Though we find ourselves in a tough situation, it is critical to remain forward-thinking and proactive. Soon things will be back up again and you will need to be operating at full speed.
The series of events that have gotten us here have created a domino effect, leading to a drop in releases and causing several supplier sites to stop production. Expensive machines and complex lines have been throttled or shut off. Bins and dunnage remain empty. Parts are stacking up in some places and requests for service parts in other sites are going unfilled. Releases, in many cases, have not fully stopped though.
Layoffs are currently happening, some temporary and some permanent. This situation has expanded beyond expectations and anticipated levels. Even when things return to normal, not everyone will be coming back. The ripple effect of these shutdowns are significant, impacting every aspect of the supply chain. To get caught back up, releases are likely to exceed normal levels and suppliers need to be ready for the next phase.
What Comes Next
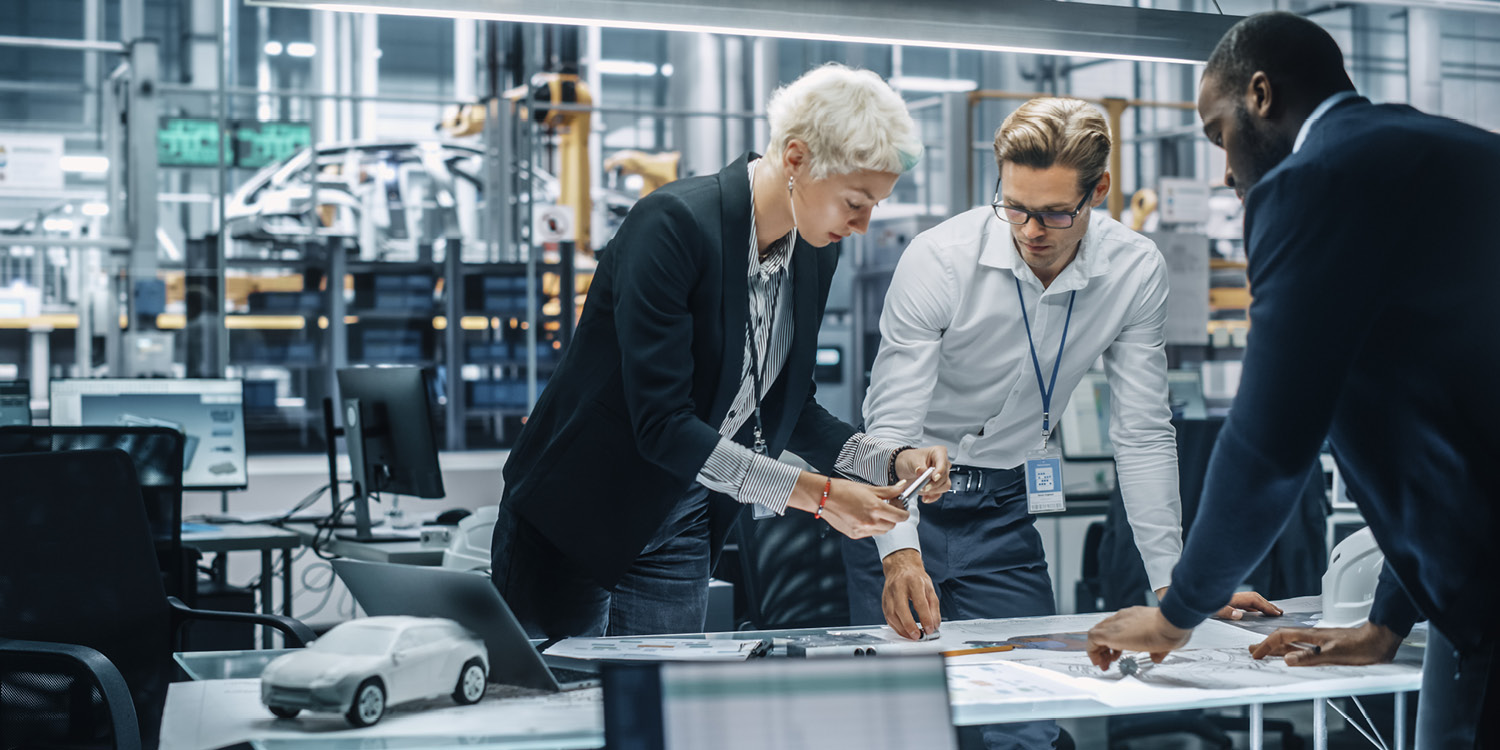
As things eventually come back online, releases will re-materialize and most likely surpass normal levels in the short term. There will then be a dash to get back up to full speed again. Slack will not be given for free. This will pose challenges for your organization. For example:
- Supply Chain - Difficulty aligning with other key players in the supply chain, e.g., manufacturers, suppliers, warehouses, and logistics. The shutdown may have resulted in altered delivery schedules, which require adjustments in production scheduling.
- Raw Material & Parts - Shortages of essential materials and parts. This can halt a production line or potentially shut down an OEM.
- Production - Rebooting production lines and reinstating operational processes is not always an easy thing to do. This process includes making sure machines are in working order, addressing maintenance issues, and training personnel on updated protocols or new equipment.
- Workforce - Challenges associated with hiring, re-hiring, training, and ensuring the safety of employees. The unexpected downtime might also affect morale and retention, requiring additional efforts to re-engage full time employees.
Resolving all of these points doesn't factor in time lost for upcoming launches. Before launching a new program, a supplier needs to undertake a meticulous capacity assessment to ensure existing infrastructure, machinery, and human resources are adequate, or identify if additional investments are necessary. Recruiting, onboarding, and training times will be considerable bottlenecks to execute this properly.
OEMs will be putting pressure on their supply base to perform. It is not uncommon for those struggling to not want to bring a challenge to the OEM because they are worried about garnering extra, negative attention. Communication will be key and hiding things will not help.
Solutions
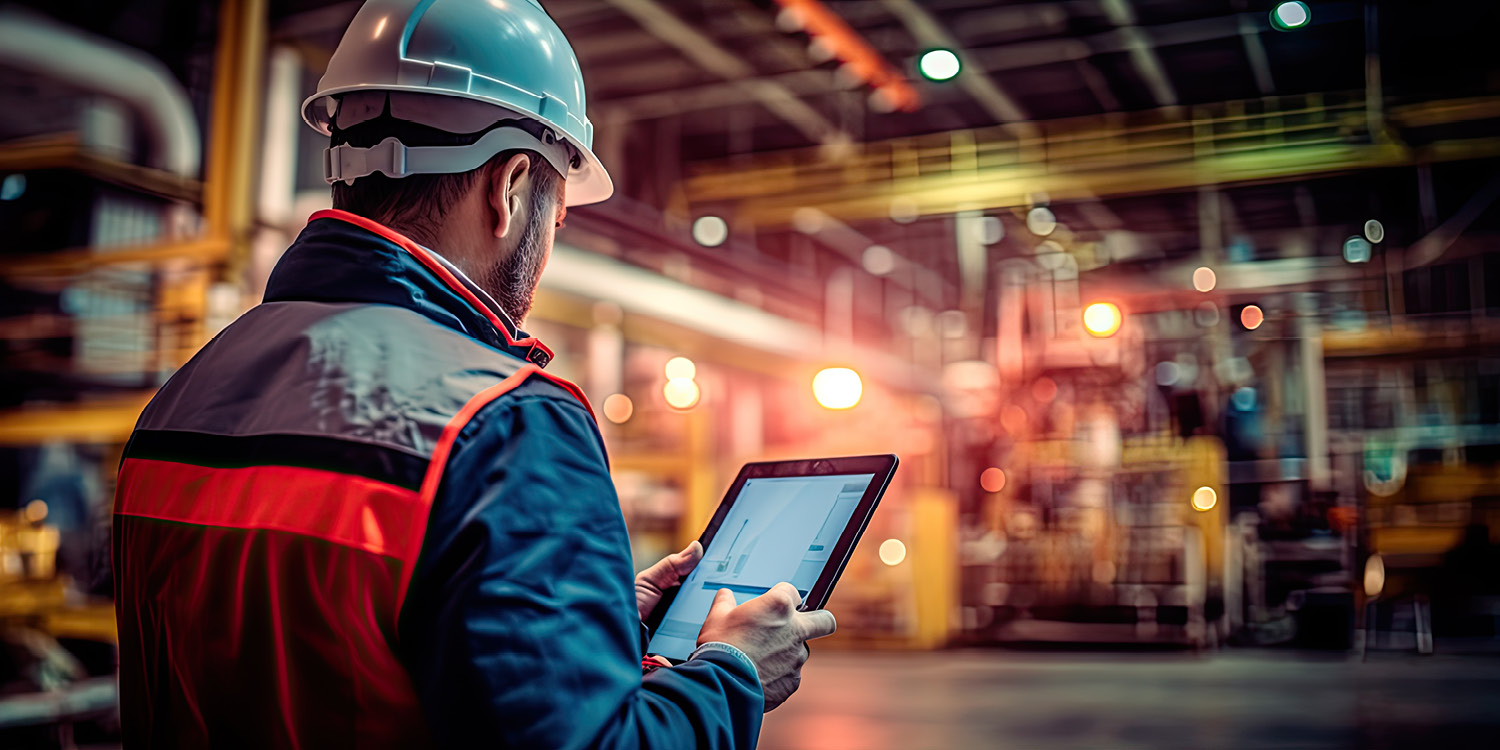
Taking all of these factors into account, suppliers need to respond as quickly and as cost-effectively as possible to scale back up from a downcycle period. Veryable has several options to look to drive operational excellence.
- On-Demand Labor - Utilizing a flexible labor pool will enable swift response to match capacity to demand. Quality Operators (workers on the platform) can quickly be upskilled and deployed to other parts of the facility. This allows for additional efficiency and a greater ROI. As Veryable is a non-fixed cost, this allows suppliers strapped for cash after a long shutdown period to boost productivity at zero cost to scale
- Standard Work (SW) - Employing SW protocols will facilitate streamlined operations, reduce inefficiencies, and expedite the process to full operational capabilities. This can more quickly curate a labor pool and allow for it to be deployed more efficiently. All of this can be handled through the platform and attached to the appropriate work opportunity (Op).
- Workforce Management (WFM) - Balancing capacity and productivity is essential. Integrating the WFM tool will balance full-time employees and a labor pool to ensure your workforce is where it needs to be and is the most optimized. This aligns operational output with releases. Learn more.
Conclusion
Though we are in the midst of challenging times, the industry is prepared to move forward and recover. The wants and needs of your customer are changing though. We need to become agile. Preparing for the upswing and new business opportunities is crucial. Developing a labor pool through on-demand labor will not only allow for a swift recovery but protect against future instances. It makes a site more resilient, ready to embrace challenges and opportunities in the future. Build this asset to not only protect what you have now but provide a long-term solution and a competitive advantage to see that your organization continues to thrive.
Previous Posts
Trump 2.0 Week 13 Recap: Discussing Ongoing Negotiations With Key Trade Partners, A Potential Deal With China On The Horizon, and More
The Future of Manufacturing and Logistics
Create a free business profile today to explore our platform.
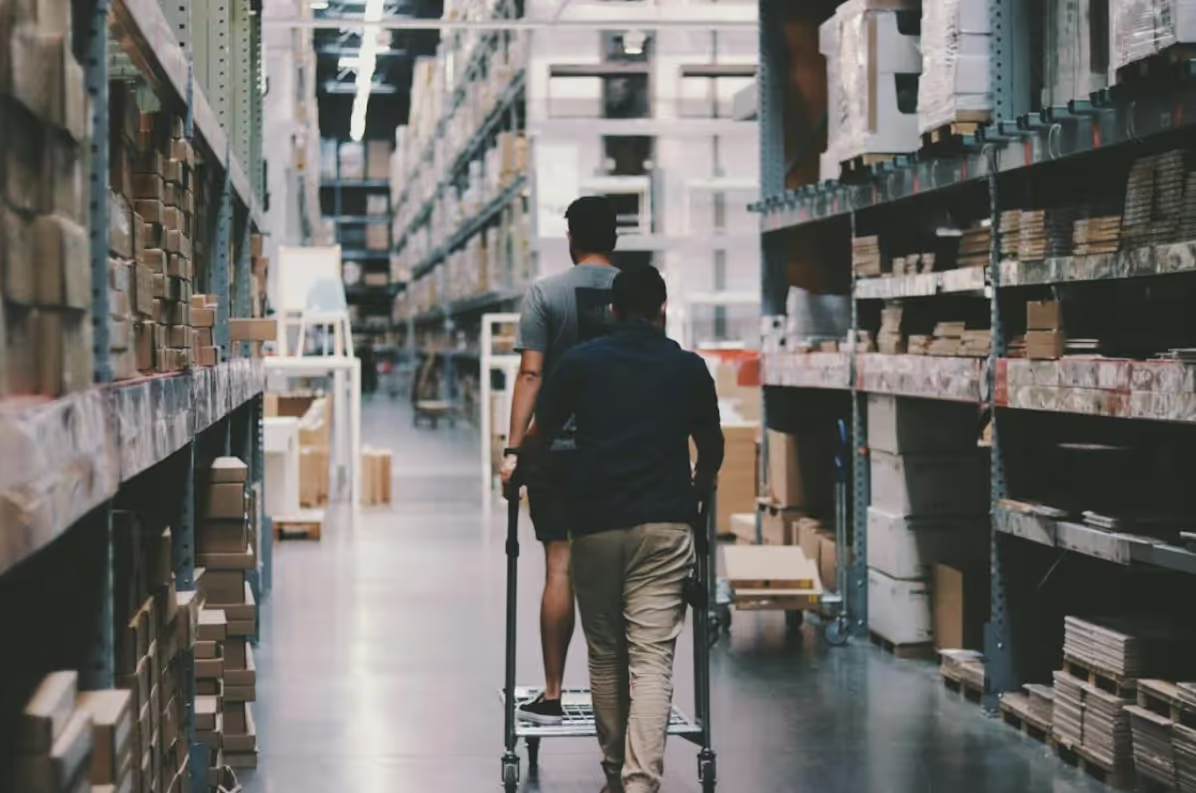