Turning Disruption into Opportunity: Navigating the Shifting Landscape of the Automotive Industry
Michigan automotive manufacturers, the heart of the American auto industry, are facing a multifaceted array of challenges that range from evolving consumer preferences and shifting market dynamics to the pressures of technological advancements and the complexities of labor and supply chain disruptions. With the increasing push toward electric vehicles (EVs) and autonomous technologies, manufacturers are required not only to retool their plants but also to develop entirely new manufacturing processes, a transition that demands substantial investment in research, development, and infrastructure; yet, as these companies grapple with the immense costs associated with these shifts, they also face the challenge of balancing innovation with profitability, all while competing with international automakers who may have more resources or better-established supply chains.
Automotive manufacturers should consider flexible workforce solutions like Veryable for several reasons that align with both operational needs and evolving industry trends.
Adaptability to Demand Fluctuations
The automotive industry often experiences fluctuations in production schedules due to market demand, supply chain disruptions, or even the introduction of new models. Flexible workforce solutions allow manufacturers to scale labor up or down as needed without the long-term commitment of permanent hires. Companies can tap into a pool of workers on-demand for specific tasks like assembly line work, quality control, or logistics, ensuring that labor is available when it's needed most.
Cost Efficiency
Flexible labor reduces the need for a fixed labor only strategy, which can lower costs related to benefits, recruitment, training, and retention. With access to a flexible workforce, manufacturers can avoid expensive overtime pay by bringing in operators during peak periods. With platforms like Veryable, manufacturers can pay workers based on the specific jobs completed, aligning labor costs directly with production output, which can help optimize financial efficiency.
Increased Speed and Agility
Manufacturers can quickly ramp up or scale down workforce levels depending on production needs, enabling faster response times to market shifts or sudden orders. Businesses can access a wide range of skilled and performance rated operators on short notice, minimizing delays and keeping production lines running smoothly.
Access to a Broader Talent Pool
Veryable provides access to a broad range of workers with different skill sets, including those specialized in automotive manufacturing tasks, such as assembly, logistics, inspection, and even robotics operation. Many of these workers are seeking flexible work schedules or gig-style opportunities, making it easier for manufacturers to tap into a diverse labor force that may not be interested in traditional full-time employment.
Improved Employee Retention and Engagement
Offering flexible workforce options can help the core team of permanent employees focus on high-value tasks, while operators handle more routine or flexible roles. This can reduce burnout and improve overall employee satisfaction. Workers on flexible platforms are typically more engaged because they have control over their schedules and can choose jobs that suit their preferences, leading to a higher quality of work.
Resilience to Labor Shortages
In times of labor shortages or tight talent markets, Veryable offers an additional layer of resilience by providing access to a wider labor pool. Manufacturers can fill critical gaps quickly without needing to wait for long traditional processes. For automotive manufacturers, which often face peaks in production demand, having a flexible workforce available ensures that they can continue meeting production quotas even when permanent employees may not be enough.
Enhanced Workforce Flexibility and Scalability
In industries like automotive manufacturing, where temporary ramp-ups in production may be required (e.g., during a new model release or major project), having access to a flexible labor force allows manufacturers to meet these needs without needing long term fixed assets. Manufacturers can engage operators for specific short-term projects, such as a factory shutdown, plant retooling, or equipment installation, without the need to hire permanent staff for tasks that might only be needed for a short period.
Improved Productivity and Efficiency
Flexible workforce solutions can optimize productivity by matching the right skill set to the task at hand. Workers on platforms like Veryable can often be selected based on experience or previous similar work, which can reduce training time and enhance output. In environments that are increasingly embracing Industry 4.0 technologies, a flexible workforce can support tasks that robots or automated systems may not fully cover—such as manual interventions or final quality checks.
Strategic Risk Management
In the face of labor shortages or other workforce disruptions, automotive manufacturers can use flexible workforce solutions to mitigate the risk of production delays or shutdowns. With a flexible labor model, manufacturers can quickly pivot if there are unforeseen changes in market conditions, supply chains, or other external factors that impact labor availability.
Call To Action
Adopting solutions like Veryable gives automotive manufacturers greater control over labor costs, scalability, and overall operational efficiency. In an industry increasingly defined by speed, flexibility, and innovation, being able to quickly adapt to changes in production demand, labor availability, and workforce skill sets can be a competitive advantage. By leveraging on-demand labor, manufacturers can focus more on strategic initiatives, such as improving product quality or accelerating innovation, rather than being bogged down by the limitations of traditional workforce models.
To learn more about our work in the automotive industry, check out our case study with ADAC Automotive.
Previous Posts
Trump 2.0 Week 9 Recap: What’s New, What’s Coming Up, and Why Agility Is More Important Than Ever
The Future of Manufacturing and Logistics
Create a free business profile today to explore our platform.
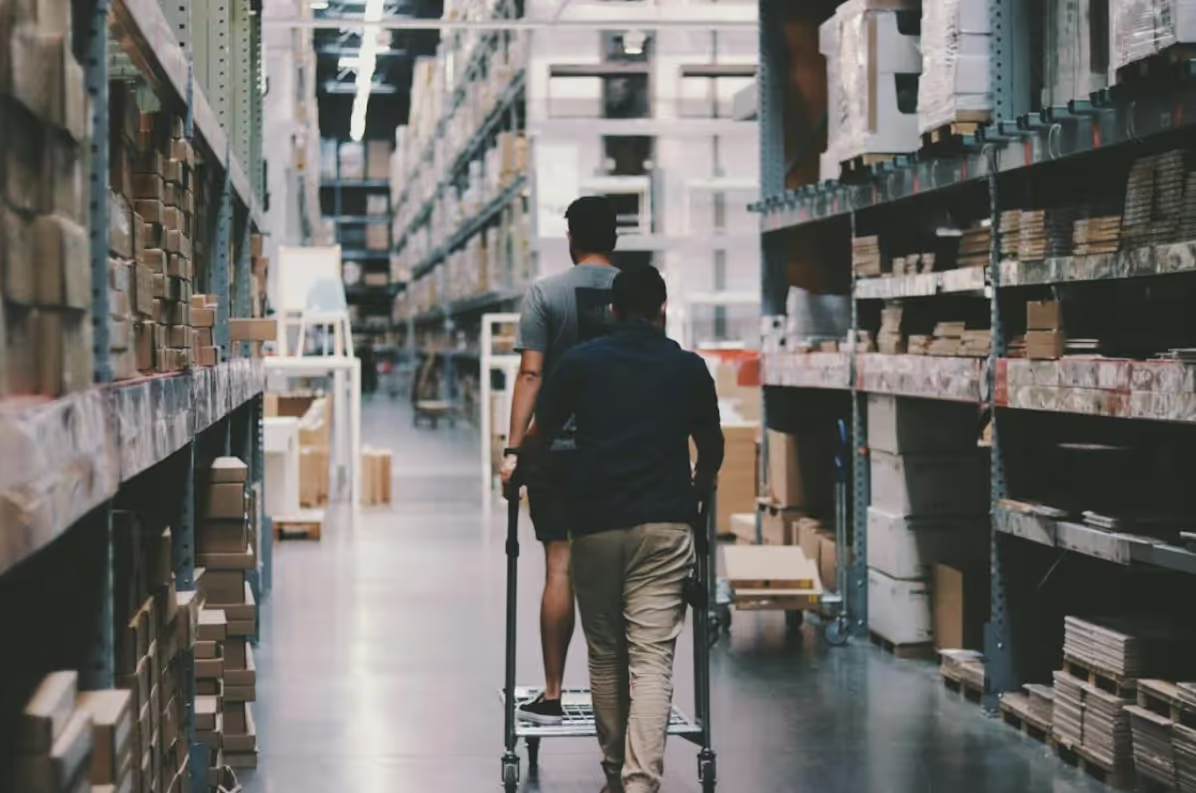