Theory of Constraints: Break Your Bottlenecks
Your organization likely shares a common thread with most others – the goal of making a profit. This may be your goal for its own sake, or your organization may need to generate profits to enable its pursuit of other goals. You’ve probably got things that are holding you back from this, but sometimes it’s hard to know what these constraints are and how to eliminate them.
That’s why I’m sharing a way to identify and break the constraints that are holding your operations back, so you can increase your throughput to grow profits. Working at Veryable, I help operations break bottlenecks every day through the creative application of on-demand labor. I won’t dwell on that for long here, but my experience at Veryable does give me insight into the practical application of the concepts we’ll discuss in this blog.
In this article, you will get an introduction to the Theory of Constraints (TOC) concept and find examples that will help you to apply it to both the manufacturing and logistics/distribution sectors.
What is the Theory of Constraints?
The core idea of TOC is that all organizations are a series of linked processes in which we perform value added activities to convert sales to profit. In any series, one of these processes is the weakest link in the chain and thereby the limiting factor. Improving the weakest link will increase the throughput of that process and therefore the throughput of the entire system.
This is not a new idea, but one that’s been vetted by industry leaders for years. In my early days at GE, I was required to read a book called “The Goal” by Eliyahu Goldratt, which introduces the Theory of Constraints. The book was impactful then, and even today it’s reported that Jeff Bezos has all his executives read it.
That’s because when applied to your operation, TOC is a powerful way of thinking which you can use to eliminate your bottlenecks.
Before you dive into the process of applying TOC, there are two underlying concepts we need to lay out. You need to first understand what your constraint is and then how you can measure your progress toward removing that constraint.
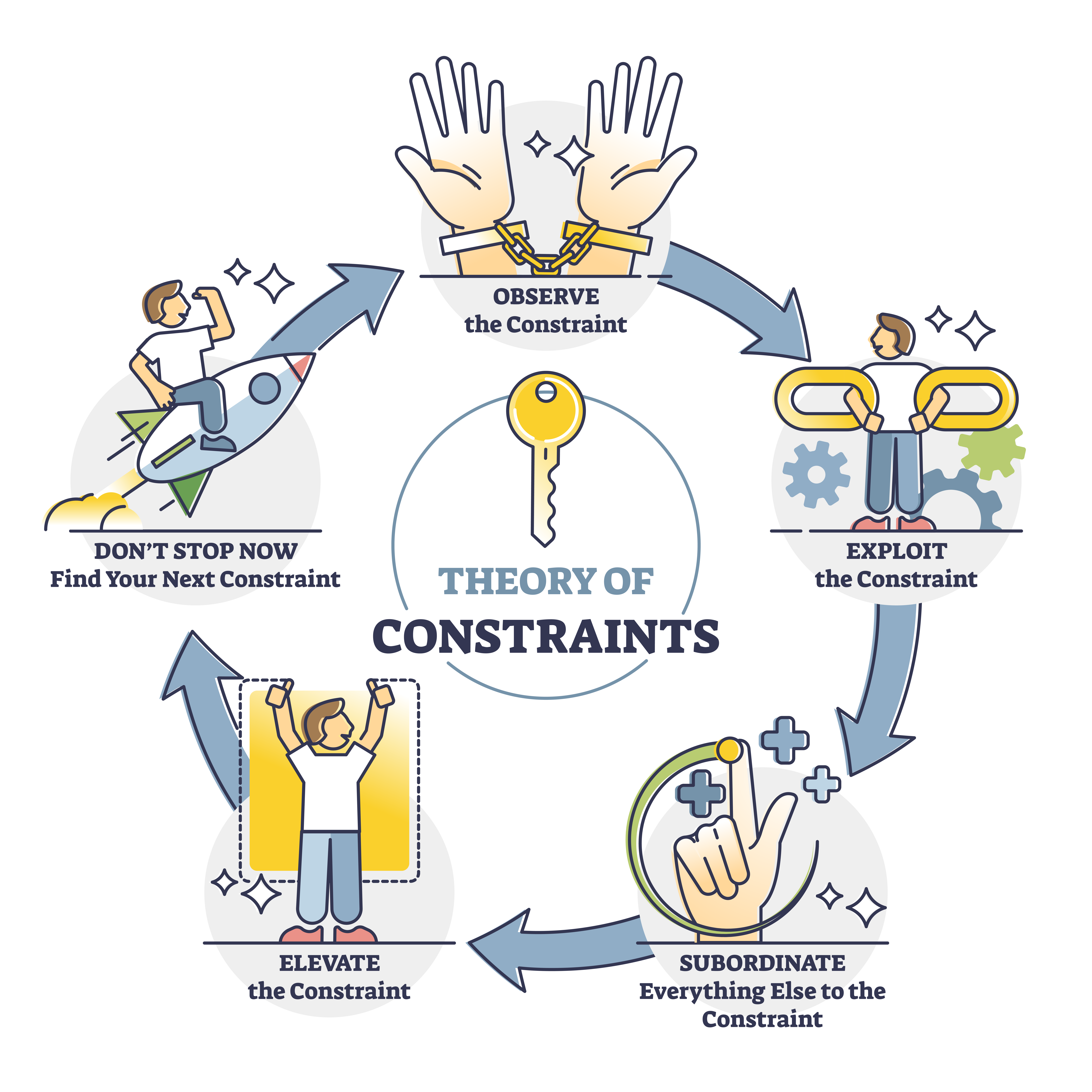
What is a constraint?
Constraints (or “bottlenecks” as typically referred to in manufacturing) are anything that keep your organization from reaching its goal. It’s easy to jump to the tangible roadblocks within your four walls, but there are many different types of constraints that might not be as obvious. I’ve categorized and briefly outlined these in the table below:

As you solve issues and mature in your use of TOC, you will encounter the need to question and address the self-imposed ideological constraints of your operation. There are some limitations that can be removed if you just know how to get rid of them.
To remove your bottlenecks, you need to understand what to change, why to change it, what it should look like after, and how to make the changes.
Of course, you’ll need a way of measuring your progress along the way as well. We’ll cover that in the next section.
How do you measure progress?
One of the key premises of the Theory of Constraints is to improve profits by optimizing in the three key areas outlined below:
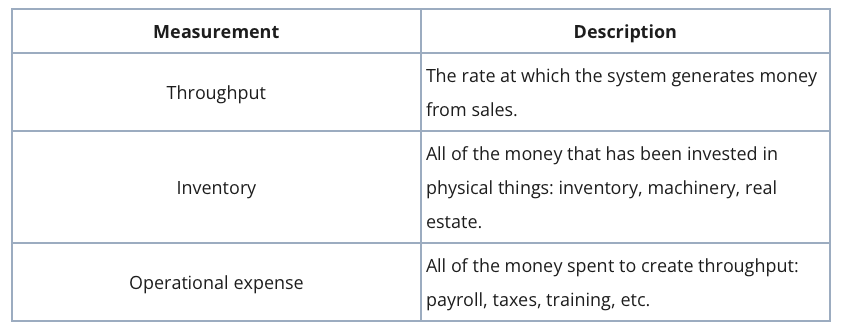
You will improve profit if you increase throughput and reduce investment and operating expense. Throughput accounting, a method proposed by Goldratt as an alternative to cost accounting, is preferred for evaluating the effectiveness of targeted TOC efforts. Because throughput accounting focuses more on throughput, you would know your efforts are successful if you see improvements in investment turns, return on investment, productivity, and net profit.
Five focusing steps for applying the Theory of Constraints
The Theory of Constraints uses a five-step process to eliminate constraints. This section will outline and explain what the five steps are in this continuous process for eliminating constraints.
- Identify the Constraint: Walk around your facility looking for some of these common indicators and understand the entire process. One indicator is work in process, which usually builds up before the constraint. Other indicators could be those processes or equipment with the longest cycle times, those areas that constantly need expediting, or steps preceding areas that run out of material often. It will help if you capture all the potential constraints and leverage available data to slim down the list.
- Exploit the Constraint: The idea of exploiting the constraint is to attack the low hanging fruit and get the most throughput improvement out of the bottleneck with your current available resources. Keep this asset operating 24/7, offload volume to other equipment if you can. Focus should be taken to ensure maintenance is performed to drive uptime and that only quality parts are being processed so as not to waste that time.
- Subordinate and Synchronize to the Constraint: All other non-constraint processes are less important, and because they are not the limiting factor, they therefore have excess capacity. Build processes around inventory in front of and immediately after the constraint to make sure that it is not starved or blocked. There are a variety of techniques that can be used to protect the constraint while minimizing the cost of incremental inventory.
- Elevate Performance of the Constraint: In this step you go deeper to look at ways to improve the throughput of the machine. At this stage, you might need better overall Equipment Effectiveness, setup or cycle time improvements, externalizing in cycle work content, or additional capital. Since you could invest significant time and money here, you need to evaluate those decisions based on their impact to Investment Turns, Return on Investment, Productivity, and Net Profit.
- Repeat the Process: The goal of these steps is to break the constraint, meaning that after some of these improvement actions are taken, the targeted process is no longer the limiting factor and the constraint moves somewhere else. As soon as that happens, stop where you are and begin back at step one on the new constraint.
Each plant, product, process, supply chain, system, method is unique. In using TOC methodology your team will undoubtedly encounter every type of constraint and will need to work through creative solutions that can quickly impact your immediate and long-term initiatives.
Applying the Theory of Constraints using on-demand labor
One of the four types of constraints we listed above is people. Often, not having enough labor is a big bottleneck that businesses just accept. Maybe you’ve been in their shoes, so rather than hire more full-time workers you’ll have to fire later, you just hold your headcount at a constant level the best you can and plan around this bottleneck.
This is like getting stuck at step three of the five steps above. You’ve identified labor as the constraint and worked around it. However, to proceed, you will need to elevate the performance of this constraint. In this case, that means adding workers to take on additional work or to increase the throughput of your system as a whole.
To support your efforts in breaking bottlenecks related to people constraints, as well as the other types of constraints, we have outlined in the table below where and how an on-demand labor platform can be most effective.
Using on-demand labor to address different types of constraints
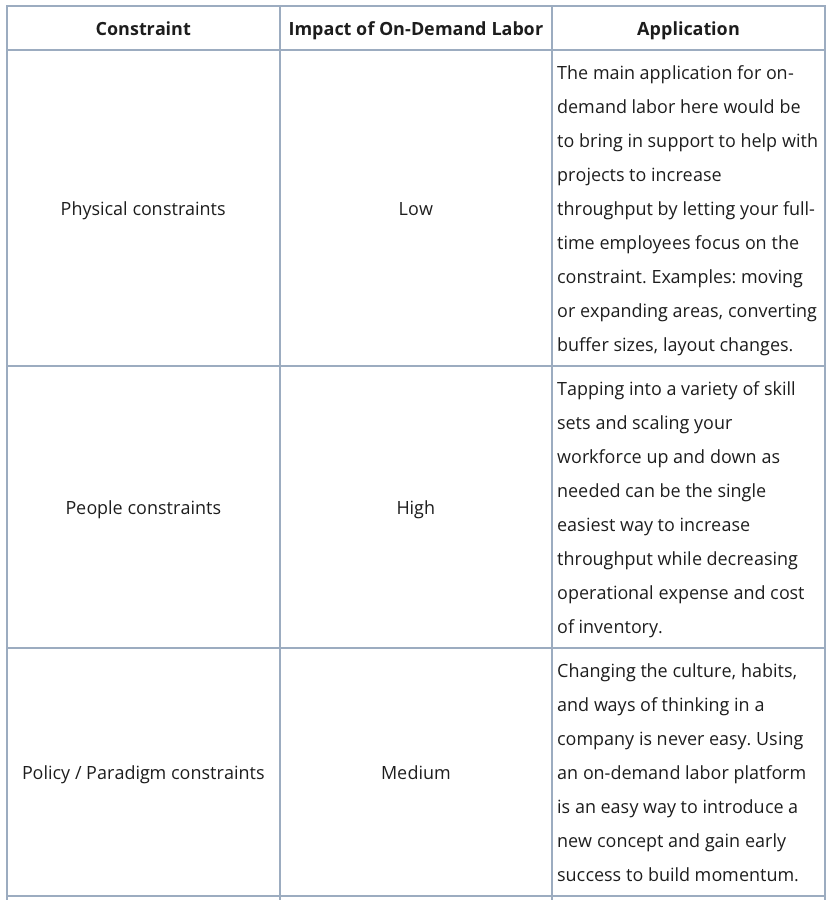
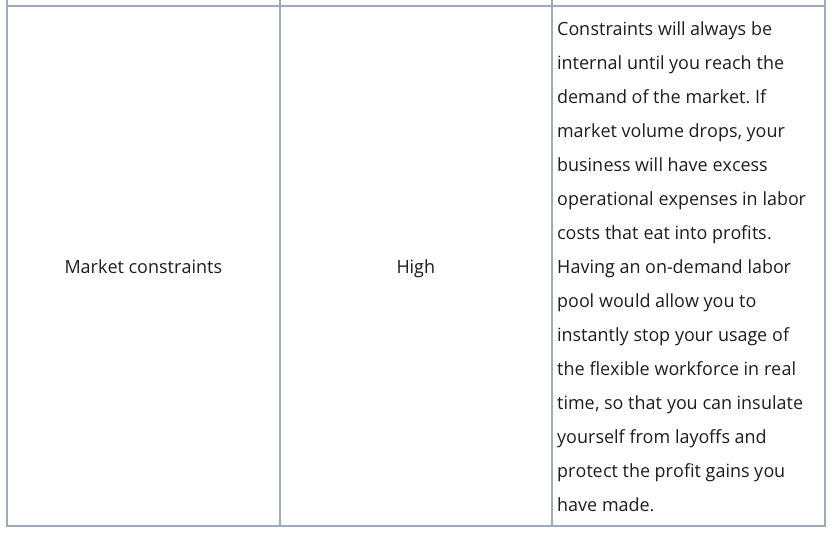
Using on-demand labor for the five focusing steps
In the below table, we summarize the impact of on-demand labor in each of the five focusing steps of implementing TOC on any one constraint:
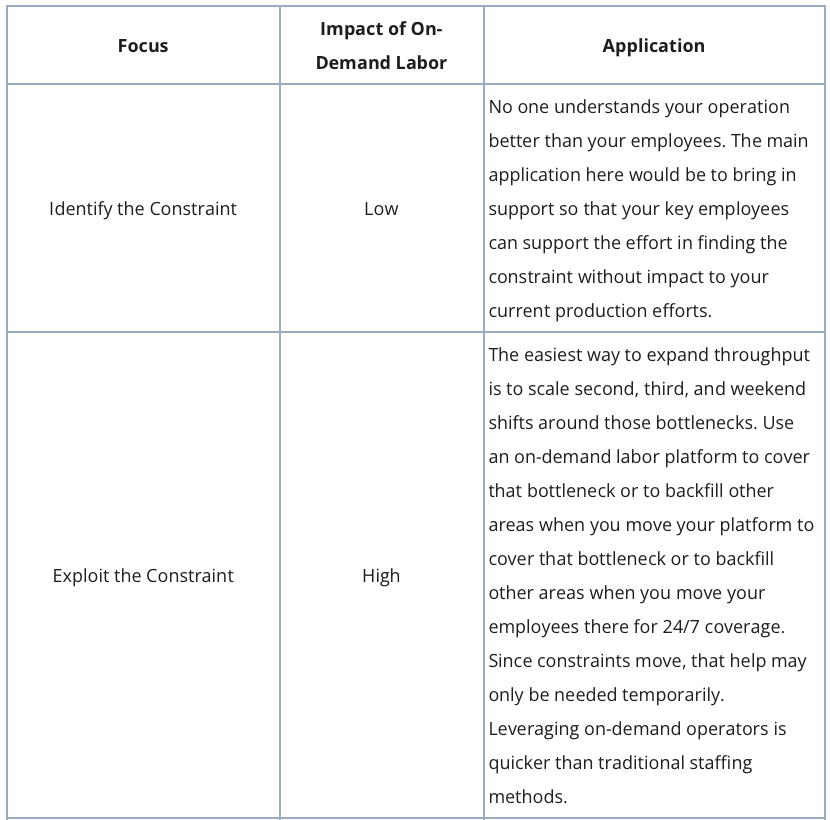

Key takeaways for manufacturing and logistics
The Theory of Constraints has been a popular continuous improvement strategy for nearly 40 years, and it has many similarities to Lean concepts and tools. You can apply TOC successfully in distribution/logistics or manufacturing operations to bring you fast improvements, reduced lead times, reduced inventory, improved capacity, and increased profits.
Although not easy to attain, these results can turn your business around or make your business more competitive in the market.
Learn where you can make the biggest impact in your operation by reading our guides to metrics you can improve in manufacturing and logistics with on-demand labor.
For more information, visit our Lean Center of Excellence Homepage or our homepage for Continuous Improvement, Operational Excellence, and Lean Professionals.
Previous Posts
Trump 2.0 Week 9 Recap: What’s New, What’s Coming Up, and Why Agility Is More Important Than Ever
The Future of Manufacturing and Logistics
Create a free business profile today to explore our platform.
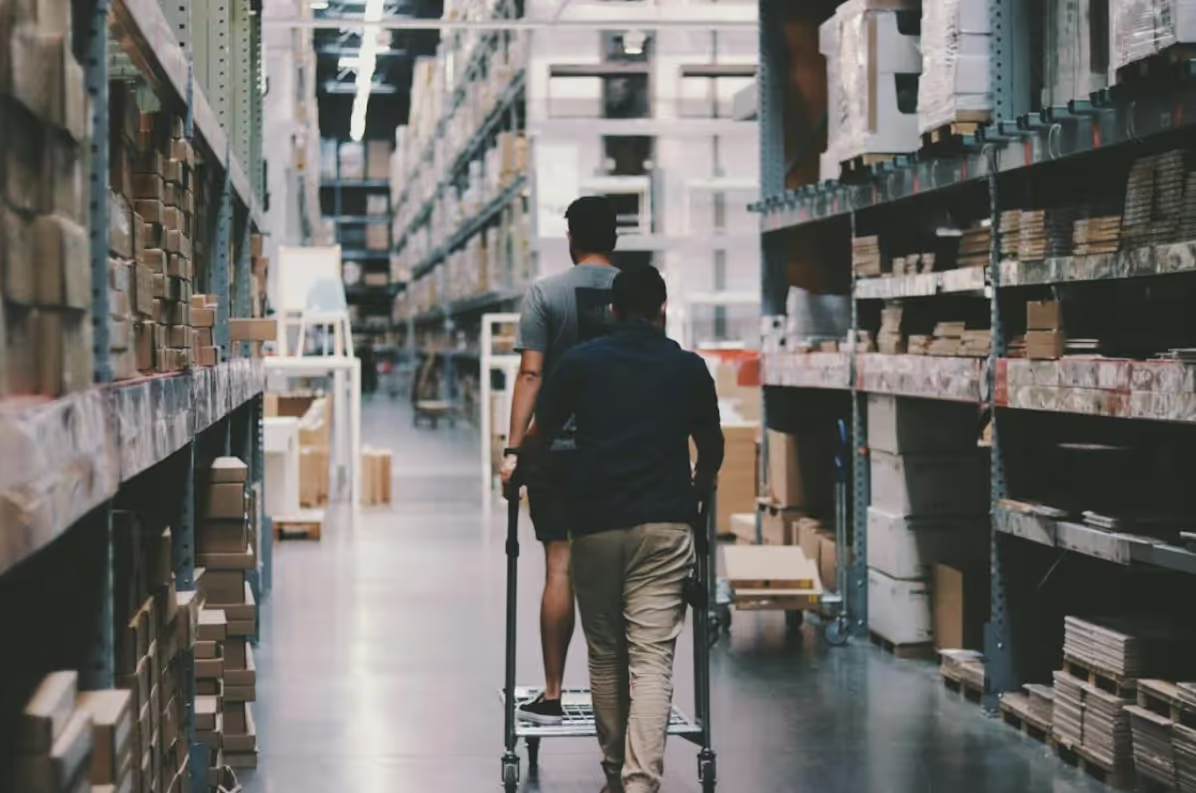