Robotics Asset vs Labor Pool Asset
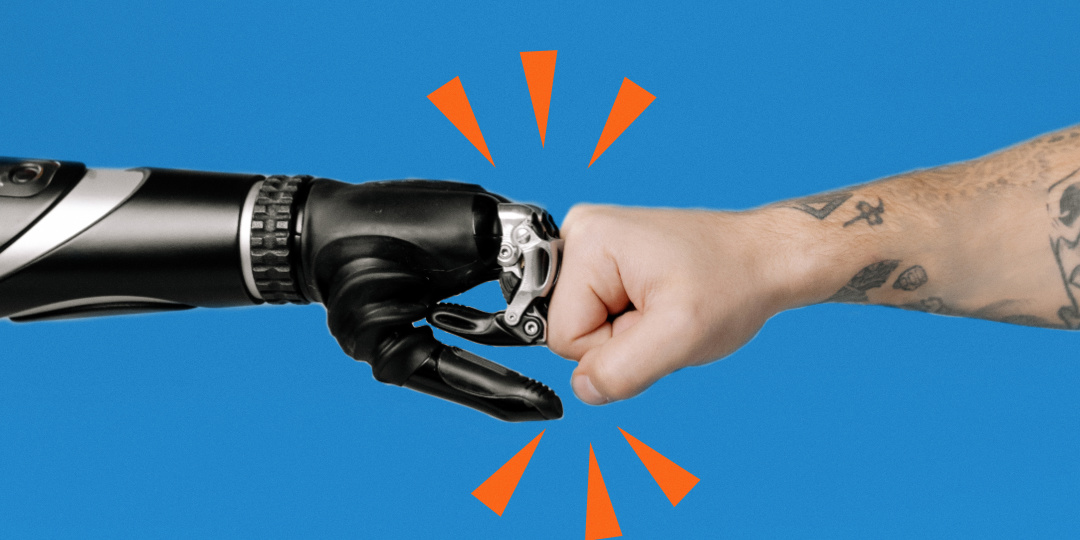
Automation, whether robots or co-bots, are drawing a lot of attention these days with the 43.7% growth of e-commerce and the increasing fulfillment needs across a number of industries and consumer categories. We’ve all heard the familiar refrain that automation is taking over in manufacturing and logistics, but that has not been the case due to offshoring versus automation.
At Veryable, we believe that automation is a job creator, not a job destroyer. The automation consumes the work that is typically deemed dull, dangerous, or dirty, which then enables people to move towards higher value-add work. The big target in manufacturing and supply chain is minimizing travel time for the workers, as they are simply moving materials from one place to another and not engaging in value creation activities that the customer is willing to pay for.
In this article, you will learn the differences between a robotics asset vs labor pool asset and how a labor pool can create value for your operation. To start, let’s analyze the key differences between robotics and labor pool assets, and their respective impact on operations.
Robotics asset vs labor pool asset
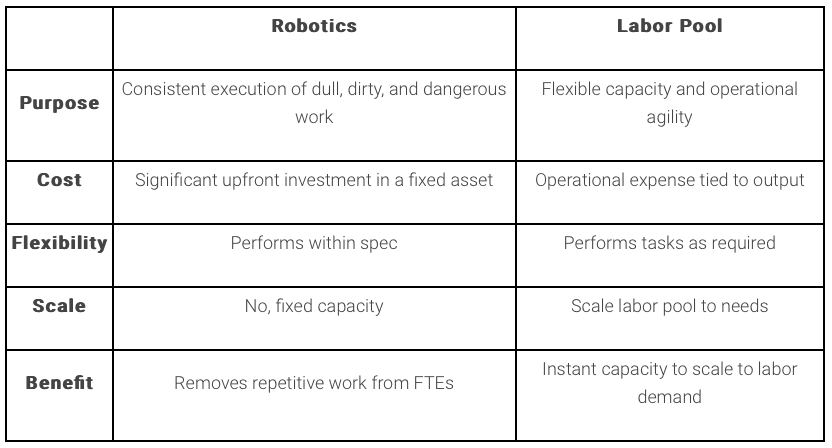
Deploying automation vs building a labor pool
When implementing automation, the goal for the automation is to execute highly repeatable tasks as part of the value chain. The outcome of a correct deployment of automation is that people are freed up to execute work that requires flexibility and thoughtfulness that adds to the product value attracting paying customers.
As a business is developing their labor pool, the goal is to provide flexibility around operational labor, and the outcome is increasing on-time in-full delivery and maintaining low lead times. These outcomes differentiate the business in the marketplace through delivering on the promise extended to the customer. This demonstrated operational excellence will increase customer retention and provide the foundation to attract new customers.
Employee engagement and retention will increase when automation is executed correctly because people will not have to suffer through the monotonous part of their job. The people experience from having to manage through different and unique problems help bring the best out of your employees, instead of them working the same tasks over and over again.
Automation cost vs labor expense
The expense of automation makes sense when the business has enough sustaining volume within the specification of the automation tolerance. Otherwise, the business will have an expensive floor decoration available for everyone to admire.
Purchasing automation is a big decision because it’s a capital asset, and one that will require booking depreciation and on-going maintenance. This is why identifying the payback period is essential, which is to drive certainty that the investment will be recouped over a short time horizon.
When building out a labor pool, this activity is an operational expense, and one that is tied to order execution. On-demand labor is deployed within the business as the company demand profile requires. With the labor being an operational expense, the business does not have to worry about booking depreciation or justifying a large capital investment. As labor is needed, the operational labor is deployed against meeting customer demand, so the labor is scheduled against customer orders. Delivering on these customer orders captures revenue and grows the business.
Automation specifications vs operational flexibility
Machines are designed and built to execute around a certain set of criteria. This criteria then creates the bounds by which the automation will be useful or not. Defining the operational specs for the equipment is the most important task upfront and requires buy-in across the organization, as this will impact cost and lead time. Going the route of automation will not be a quick process that leads to value.
Once a business has signed the contract, then they have immediately lost their leverage because they have now made a commitment to a particular solution and committed funding. This is a big risk factor that creates unease when going down the automation path.
Operational labor creates flexibility. Instead of anchoring the business around a defined set of criteria, the operational labor opens opportunities for the business to experiment with projects that would expand the scope and capabilities of the business. This in-turn opens up growth opportunities, which is a big contrast to automation that makes it possible to do more of the same thing faster.
Scale: fixed capacity or flexible capacity
When the automation solution was purchased, one of the specifications was a run rate for throughput. This key design criteria then sets the rhythm for the organization, which can likely be out of step with takt time and heijunka, and this problem then creates its own issues of overproduction and wasted movement. If the business is in a time of lower demand, then the automation can be throttled, but no one ever wants to see automation running at less than its design capacity.
The flexible capacity of operational labor allows the business to scale as necessary. If the business is on the doorstep of adding automation, then they can use operational labor as bridge capacity to build sustainable volume to make the automation decision an economical one with a short payback period on the investment.
Benefits of automation and operational labor
The big benefit of automation is that it enables people to do higher value work, which is what people are more suited for versus doing repetitive tasks. Innovation is not something to be feared. Society has not advanced to this point without innovation and automation. Starting with the first looms of the industrial revolution, innovation has been critical to raising the standard of living for everyone. Embracing the false thinking of luddites will not do anyone any good moving forward.
Operational labor benefits the business by creating flexibility with no upfront investment. This is a big strategic lever that lets the business pursue new business to grow without overextending a current FTE base of adding new employees prior to receiving the next big customer order that will grow the business.
To learn more about operational labor, you can read more on our blog about building a labor pool. The operational benefits to scale without upfront investment will enable the business to grow and take advantage of the next opportunity around the corner.
Previous Posts
Trump 2.0 Week 25 In Review: July Deadline Extended, 50% Copper Tariff Announced, and Higher Tariffs for Canada, Brazil, and BRICS
The Future of Manufacturing and Logistics
Create a free business profile today to explore our platform.
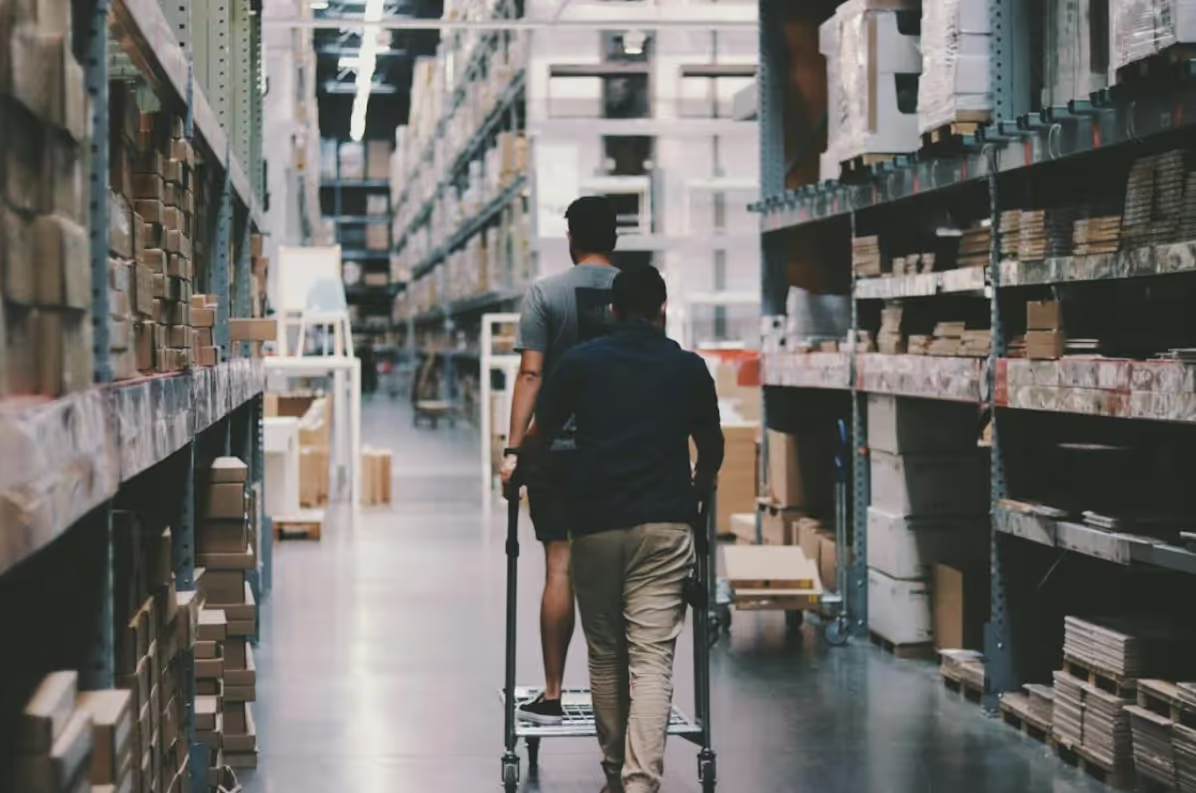