The Problem with Heijunka Production Leveling
Implementing heijunka to level your production is a longstanding approach to manufacturing. However, it can bog down your business when it is used as a self-imposed, artificial constraint on production.
You might not realize that sticking to your smoothed schedule is holding you back. We’ll admit, the reasoning is solid if you have truly immovable capacity constraints limiting the takt time you can achieve.
But we argue that you should not just accept your constraints as immovable. What if you could remove your biggest constraint; would heijunka still be useful to you, or would it hold you back?
Heijunka accepts constraints and only patches the problem
Heijunka is a reaction to unpredictable demand that takes the approach of leveling out production over a time horizon, ranging from a few weeks to a few months, based on forecasts from your customers. The underlying assumption is that you cannot quickly ramp up production to meet unexpected demand from customers, thus the emphasis on smoothing over the timeline of months. In theory, this gives you time to solve your constraints and would still create less excess inventory than if you didn’t plan ahead at all. However, this is a stopgap, not an ultimate solution. Heijunka requires accepting your constraints as a fact of life, and submitting your production to this self-imposed constraint. Remove one major constraint, and you no longer have to rely on production smoothing to meet increased demand.
Removing labor constraints eliminates the need for leveling
Labor is the number one constraint holding manufacturing companies back. Without this constraint, your only limitations would be equipment, space, or availability of materials. This is important because these limitations are why leaders in operational excellence say you should optimize “within your four walls” to get the most out of what you already have. The availability of materials is a problem for procurement to solve, while additional equipment and space are just expensive ways to amplify existing inefficiencies. Therefore the first operational improvement you should make would be adding labor capacity to your operation. Add workstations, add support workers, and add extra hours to your uptime before you consider buying more machinery or moving to a bigger facility. When you can add instant labor capacity to your operation any time you need, you can scale to meet increased demand one week and then scale back down the next week. This way you can avoid creating excess inventory and keep cost per unit where you need it. You won’t need to plan months in advance and slowly ramp up production over the course of months, creating excess inventory based on what’s likely an inaccurate projection from your customer.
Why you should ditch heijunka and adopt a flexible approach
The essence of what's wrong is this: heijunka relies on an (often inaccurate) forecast from your customer, and just smooths out your production. It is only slightly better than outright rejecting new business, delaying lead times, or keeping huge piles of inventory just in case someone makes a bigger order than usual. Instant, flexible capacity will enable you to escape the reliance on forecasts and smoothing. You will be able to respond accurately to customer demands, just in time and with confidence. Keep in mind that while you might adopt a flexible approach, it doesn’t mean your supplier will at the same time. This can cause some friction if your order size fluctuates because your matching demand more precisely, but they keep shipping the same amount consistently. As you think holistically about your operation, you might need to find a new supplier or help the one you have adopt a flexible approach like yours.
Learn how to gain flexibility for true response to demand with on-demand labor on our blog.
For more information, visit our Lean Center of Excellence Homepage or our homepage for Continuous Improvement, Operational Excellence, and Lean Professionals.
Previous Posts
Trump 2.0 Week 13 Recap: Discussing Ongoing Negotiations With Key Trade Partners, A Potential Deal With China On The Horizon, and More
The Future of Manufacturing and Logistics
Create a free business profile today to explore our platform.
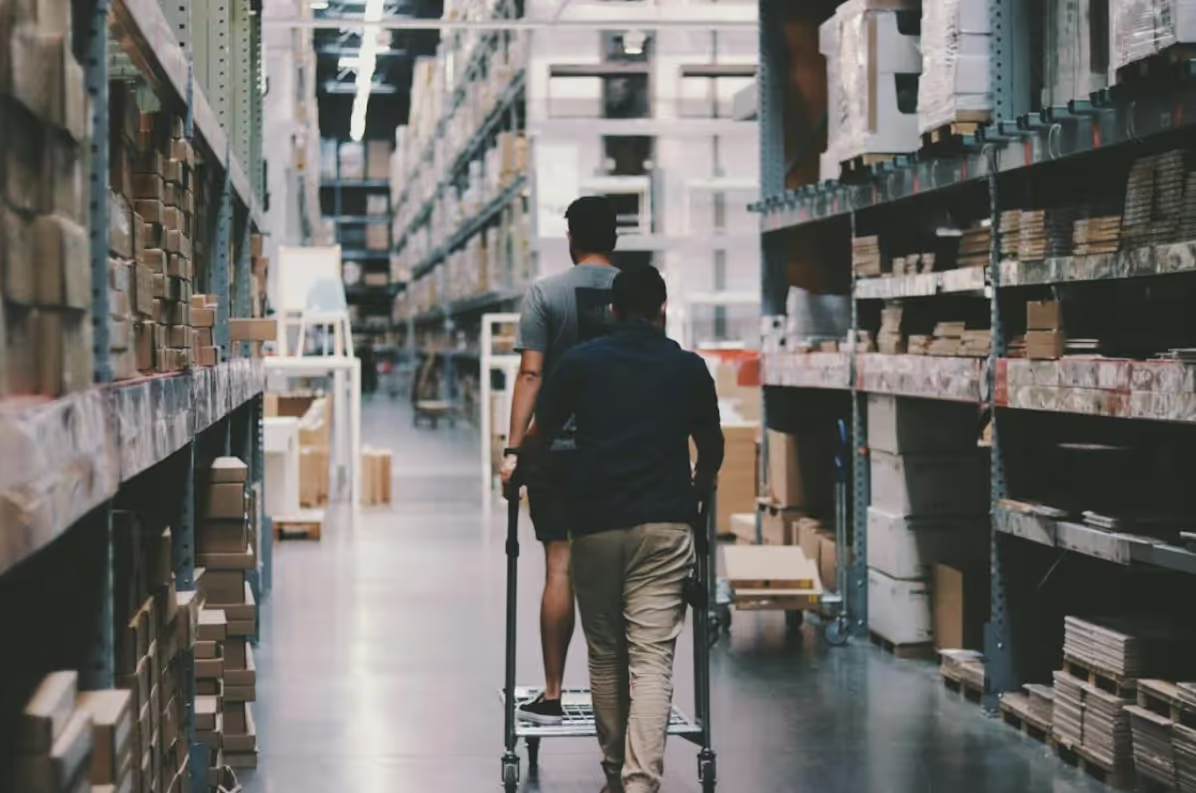