POV: Automation – The Right Solution for the Right Reasons
Growing up in the “City of Firsts,” the manufacturing roots run deep in my family. Essentially every relative, coach, and adult I knew as a child worked in one of Kokomo, IN large factories on an assembly line or in skilled trades dating back to Haynes-Apperson, the first profitable American automobile manufacturer. From an early age, my plan was to get a degree (that my parents never had the opportunity at) and then follow them both into the factories for the next 30 years. That was until the 2008 Recession hit and changed those manufacturing sites completely. Needing to pivot directions, I spent the majority of the next 10 years in industrial project management working inside some of the Midwest’s largest manufacturing and distribution centers.
Project Management in the Systems Integration industry is a bit like baptism by fire, over and over again. Each facility is unique and presents their own set of challenges to ensure the most efficient operations and quick cycle times. Every city, county, and state have different regulations and requirements for permitting and they’re continuously changing. Would this facility optimize their processes with drive-in racking rather than pushback racks, would AGVs (automated guided vehicles) or AMRs (autonomous mobile robots) be the best option, should we maximize the space with wire guided VNA lift trucks or go with standard lifts and much less storage capacity – the options are endless while working through new facility designs but the level of automation for each facility always come down to 1. Cost and 2. Workforce.
These type of equipment improvements and projects take a great amount of time to complete. Due to engineering designs, long material lead times, permitting, etc., it’s not uncommon to have projects that last 6-12 months to complete. Most facilities would plan for their worst-case scenario meaning millions of dollars wrapped up in equipment that won’t be used until the business grows. With volumes constantly changing, you have to plan for the highest number of products and the heaviest products the facility would ever need to produce or store to ensure the safety of the systems. With the ever-changing technology, you could be implementing an automation solution that has outdated software almost immediately, but it was typically the best option many of these sites had due to inconsistent and unreliable workforce options in their area. Take a minute to read through some of the Pros and Cons of Automation to flush out some of the different considerations you should think through.
Automation makes our lives easier - whether it’s on an assembly line, self-driving car, or speakers making your home “smart”. But if you’ve ever told your Amazon device to turn on the lights and have been left standing in the dark, you know there can be issues, and it’s the same with your robotics along the assembly lines or automated storage and retrieval systems (ASRS). When working as designed, these automated systems can be incredible and cut down on cycle times, but there is still a human element to each of these setups. While fully automated facilities are fascinating to see and talk about, with over 95% of US Manufacturers considered small to mid-sized, the majority of these sites cannot expend the capital to go full automation.
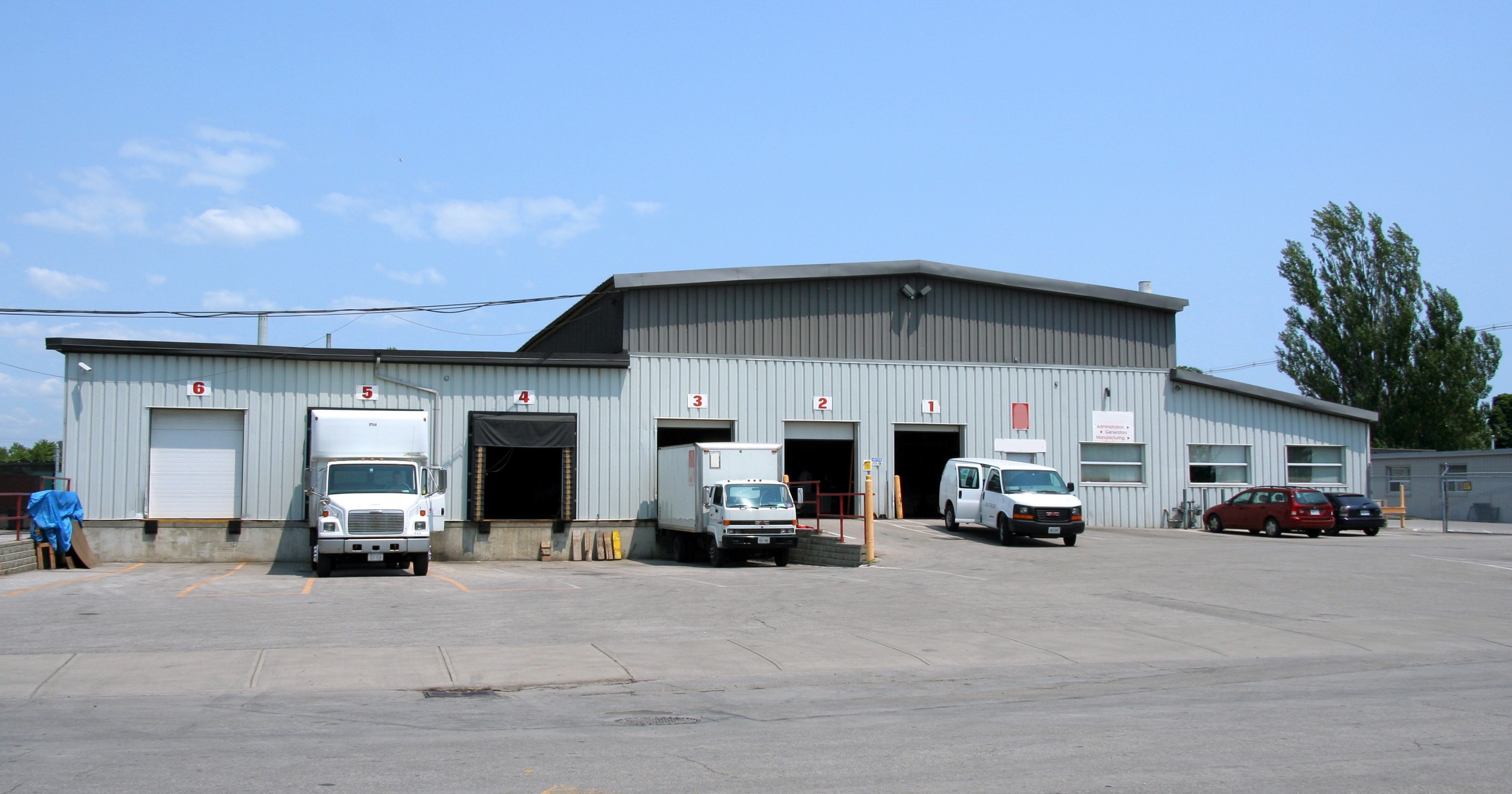
When I found Veryable, I was on-site for the install and implementation of a large project. This 3PL was expanding to a new industry and was introducing a line of robotics because they could barely keep up with their legacy clients demands and knew they could not hire enough people for the new industry introduction. I started floating the concept to my contacts to just see why this would not work, but all of the responses I received were telling me how transformable it would be for their specific facility. The ability to match their labor capacity to the changing client demands would eliminate unfathomable wasted costs. Solving the labor issue would give them time to analyze where automation should go and design a better solution. Veryable would also give them incremental flexible labor to bridge the long lead times until that automation was installed and in use.
I started to realize the impact this type of platform could have on specific industries and economies. We all strive to do work that is meaningful and that makes a difference, and that’s what I found intriguing about Veryable. I’m never going to save lives as a doctor, and my church may kick me off the stage if I ever tried to preach, but Veryable lets me impact my community and the lives of my neighbors every single day. Veryable is in 45 major metropolitan markets helping manufacturers and distributors across the country. Check out how Gilster Mary Lee found success in a more rural area and the impact that it had on their operations. While our Kokomo, IN market hasn’t quite launched, I’ll know it’s come full circle the day a Veryable operator is in one of the factories I’d long ago planned to spend 30+ years at.
For more on this topic, check out our more recent article.
To learn more about how Veryable makes it easier to reach your goals, visit our info for your role page.
Previous Posts
Trump 2.0 Week 25 In Review: July Deadline Extended, 50% Copper Tariff Announced, and Higher Tariffs for Canada, Brazil, and BRICS
The Future of Manufacturing and Logistics
Create a free business profile today to explore our platform.
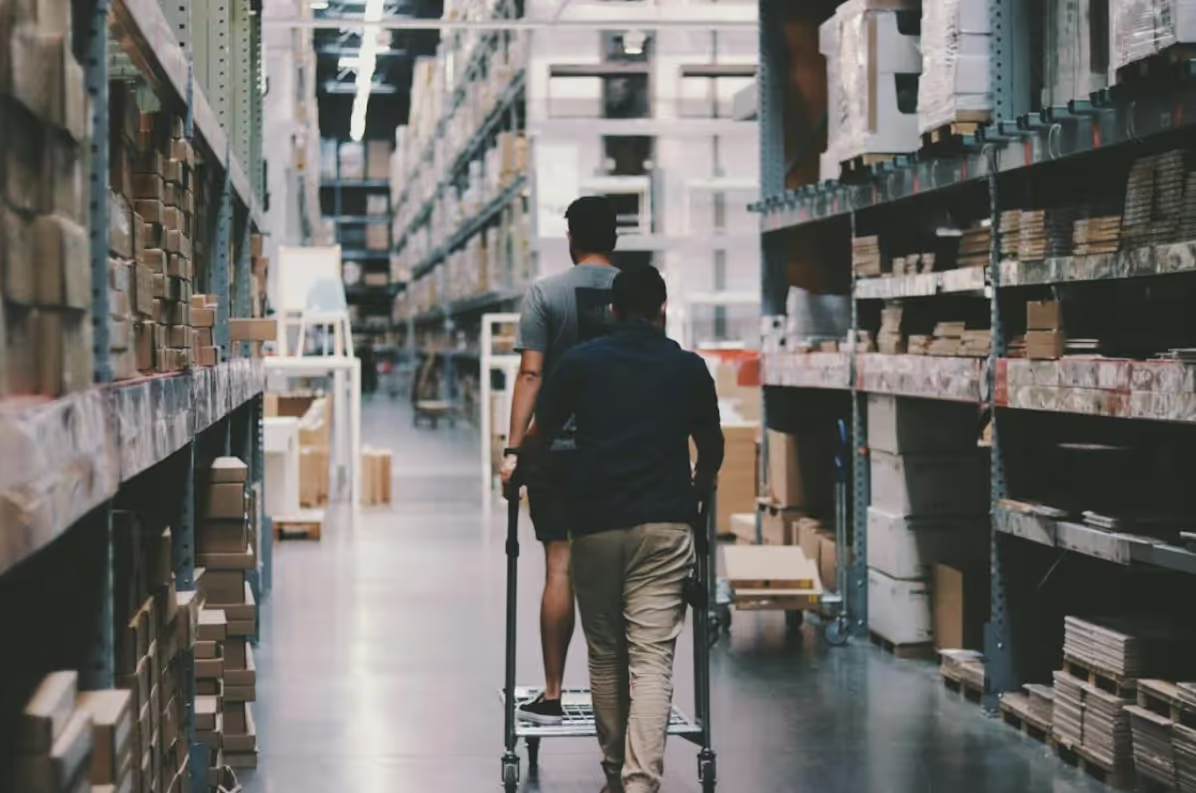