November 2023 Automotive Update: Navigating The Post-Strike Landscape and Ongoing Chip Challenges
Welcome to our latest update on the automotive industry for November 2023. In this blog, we delve into critical developments, from the tentative resolution of the UAW strike to the persistent challenges in semiconductor supply chains and pertinent market trends.
UAW Strike Resolutions: Tentative Deals and Implications
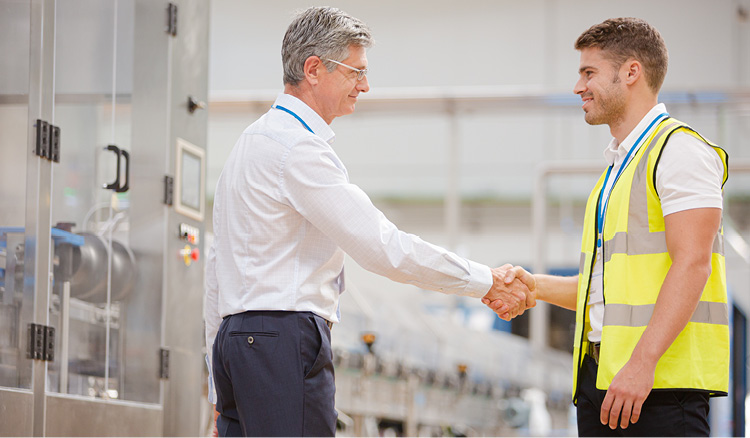
UAW Strikes End with Tentative Agreements
In a significant turn of events, General Motors (GM), Stellantis, and Ford have reached tentative contract agreements with the United Auto Workers (UAW), potentially marking the conclusion of a six-week strike. The coordinated effort by the UAW to negotiate with all three automakers simultaneously proved successful, yielding seemingly robust agreements across the board.
Higher Labor Costs on the Horizon
Under the tentative deal, Ford and Stellantis employees are set to receive an immediate 11% pay increase. Hourly pay at Ford is expected to rise from $32.05 to $42.60 for assembly-line workers and from $36.96 to $50.57 for skilled trades employees. Similarly, GM employees will see a 25% hike, reaching over $42 an hour, with the starting wage exceeding $30, including the cost of living adjustment. Notably, the two-tier wage system, in place since 2007, is set to be abolished.
Ratification Uncertainties Loom
While the agreements signal positive strides, there is no guarantee of ratification by UAW members. Recent events, including the rejection of a tentative deal with Mack Trucks, highlight the uncertainty. Other votes at individual plants, such as GM's Flint assembly plant (Silverado heavy duty pickup truck manufacturer) and Ford's Chicago assembly plant, provide a mixed outlook, emphasizing the tentative nature of the agreements.
Staggering Costs of UAW Strike
When UAW President Shawn Fain halted the strike following the tentative agreement with the major Detroit automakers, the financial repercussions amounted to billions. As per the assessments by Anderson Economic Group, LLC., the expenses incurred during the UAW strike reached $10.4 billion by the end of its sixth week. The breakdown of losses until October 26, concluding the sixth full week of the strike, is as follows:
- Wages of OEM Workers: $650 million.
- Losses to the Detroit 3 Manufacturers: $4.3 billion.
- Lost Wages and Earnings to Supplier Companies and Workers: $3.3 billion.
- Losses to Dealers, Customers, and Ancillary Auto Industry Workers: $2.0 billion.
Moreover, the economic group predicts that the overall cost of the strike will exceed the initial six-week estimate, even if the agreements receive swift approval and ratification. This is attributed to additional production losses, allowances for potential ratification bonuses, adjustments based on plant reopening dates, the impact of delayed or deferred investments, and corrections for strike-related costs from October 27 onward.
Ongoing Semiconductor Supply Chain Challenges
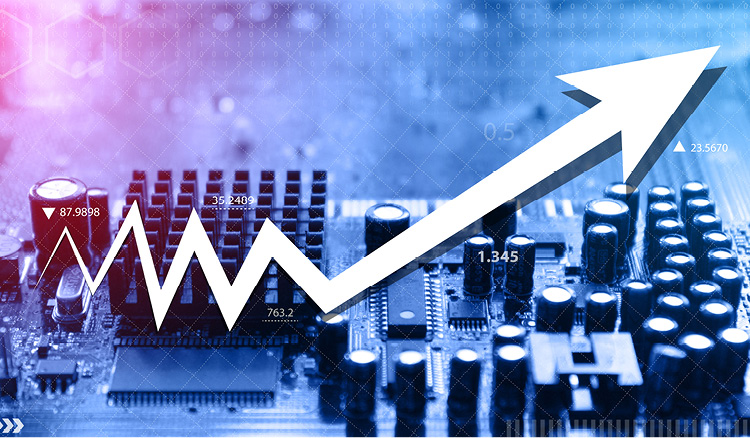
Chips Shortage: Slow Recovery and Lingering Concerns
According to most evaluations, the existing chip shortage remains a concern but is gradually progressing towards recovery. As we reach the final quarter of 2023, automakers are experiencing fewer disruptions in production. However, the unexpected nature of the current chip shortage caught the industry off guard, implying that another one could occur without warning. Is the auto industry adequately prepared?
In 2023, semiconductor manufacturers are not just striving to meet current demand; they are also working to fulfill backorders resulting from the challenges of the past several years. Despite increased investment and capacity, tackling both aspects simultaneously poses a significant challenge. Essentially, one of the primary obstacles to overcoming the supply chain shortage is the shortage itself. Jennifer Strawn, an executive Vice President for a leading global sourcing and supply chain solutions company stated, "I anticipate that some companies will spend a considerable part of the year absorbing or selling surplus supply while seeking essential parts to finalize the manufacturing process."
Factors Influencing Chip Supply Chain Resilience
The concept of just-in-time (JIT) manufacturing, also known as lean manufacturing, originated in the 1950s and gained prominence in the 1980s. By 2019, it had become the standard operating method for auto manufacturers. Instead of producing a surplus and hoping to sell the units, the JIT model aims to align production with demand, only manufacturing products that have already been ordered. This approach is designed to minimize waste and enhance manufacturing efficiency.
While successful under normal circumstances, the JIT model faced challenges when global closures due to the pandemic left companies without a robust reserve stock. This particularly impacted the auto supply chain, including semiconductor manufacturing.
Manufacturers in the automotive industry have recognized the need to reevaluate their semiconductor supply chains. Initiatives such as securing substantial contracts with producers and transitioning to domestic producers aim to reduce variables in the chain. These changes are expected to minimize the impact of future disruptions to production or logistics.
However, the semiconductor supply chain remains susceptible to external factors beyond manufacturers' control. Escalating trade tensions between the U.S. and China, the rapid growth of the EV sector, and manufacturers rushing to secure semiconductor supplies may affect the flexibility of the semiconductor supply chain in the future.
The shortage underscored the crucial role of semiconductors in the modern automotive industry and exposed vulnerabilities in the supply chain. Persistent challenges, coupled with emerging ones, underscore the necessity for the auto industry to continuously enhance the resilience of the chip supply chain in anticipation of future unpredictable events.
Market Trends and Regulatory
National Association of Manufacturers (NAM) Policy Update
NAM has provided insights into policy actions related to new fuel standards and regulations for light vehicles. Harmonizing standards and establishing realistic targets are key focuses, considering multiple standards and compliance timelines from various regulatory bodies.
Aftermarket Parts and Labor Costs Trends
Transport Topics reports a slight decline in costs for aftermarket parts and labor in the second quarter, following a period of rising prices. However, rates are expected to remain elevated until inflationary pressures recede, emphasizing the need for strategic planning.
Learn More:
Previous Posts
Trump 2.0 Week 9 Recap: What’s New, What’s Coming Up, and Why Agility Is More Important Than Ever
The Future of Manufacturing and Logistics
Create a free business profile today to explore our platform.
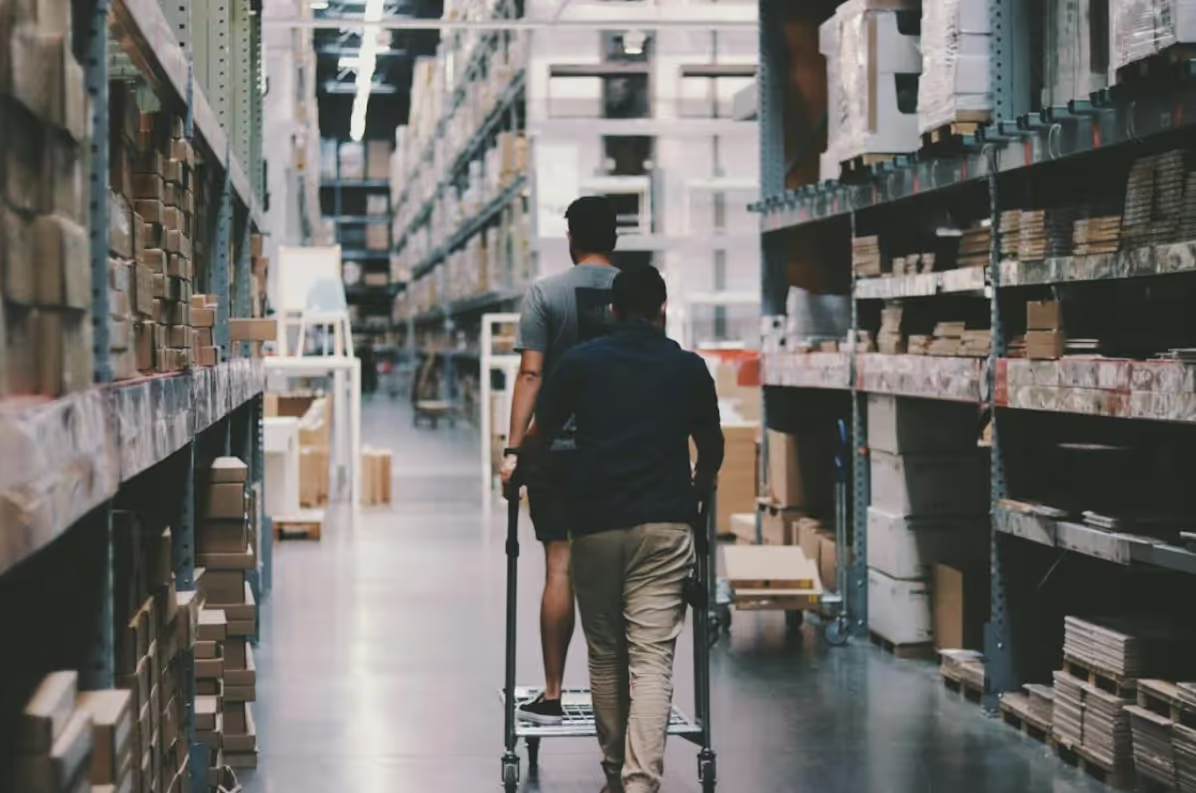