Lean 4.0: How Industry 4.0 Is Evolving Lean Manufacturing Concepts
In today’s world, Lean is being challenged as never before due to higher customer requirements and the digital revolution of Industry 4.0. The challenge to keep up in the landscape leads to the questions: Are Lean principles in conflict with the digitization that is Industry 4.0? Are Lean principles in conflict with serving your customer in the manner in which they have requested? The short answer is mostly no, and we’ll dig into the alignments and variances below. But, in order to keep up in today’s world, Lean does need to evolve to match today’s quick response, digital environment.
What is Lean 4.0
The next evolution of Lean is called Lean 4.0 and focuses on bringing the time-tested Lean methodology up to date with the digital revolution that is Industry 4.0. This new Lean 4.0 is a response to rising customer demands for customization and best-in-class lead times, thanks to customer expectations aligning with the near-instant gratification enabled by competitors like Amazon and Shopify.
How Lean is aligning to the future of manufacturing
Next, we’ll uncover where Lean is aligned to the future and where it needs to evolve. The good news is that if you and your business have adopted Lean principles, then you’re set up to leverage the digital revolution of Industry 4.0 to win in the marketplace.
Ultimately, you will be better positioned to deliver customer delight by responding to their needs in real-time. We’ll cover how the following Lean concepts align to the the future:
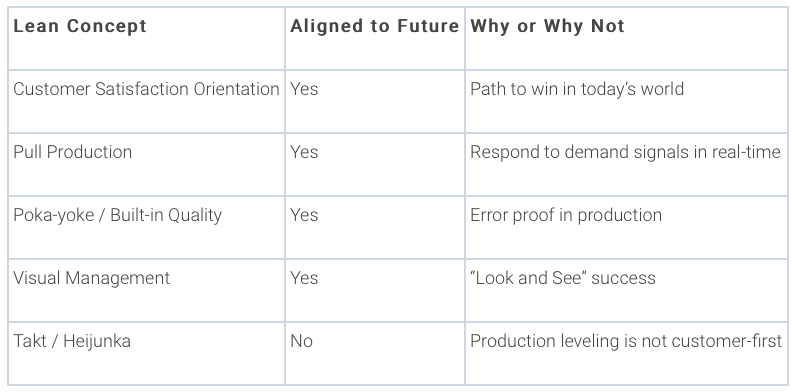
Customer satisfaction orientation
Lean is centered on delivering customer value and exceeding their expectations through developing a culture of partnership. Both internally with employees and externally with customers and suppliers in order to continuously improve the product to better meet market needs.
The customer orientation is where Lean must lead while aligning with digital transformation. Industry 4.0 does not offer the framework for customer orientation but rather it offers real-time data and analysis that enables better decision making and shorter cycle time in product development and production.
Lean creates the competitive advantage while Industry 4.0 is the path forward to improved customer experience and more robust operations by making sense of the data faster.
Pull production
The customer demand signal is the central trigger that sets a Lean production process into motion. This is the common sense approach that Lean uses to produce only what is needed when it is needed, and why driving production to one-piece flow is essential to removing wasted materials and handling time.
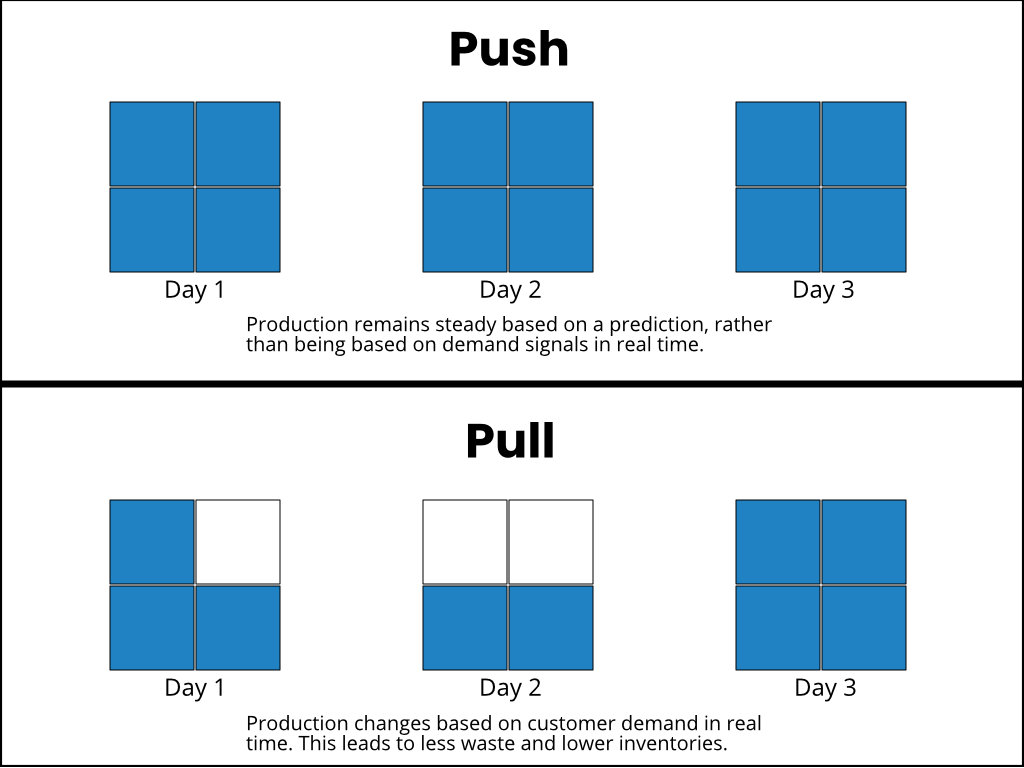
The best way to satisfy the customer is to respond to their needs in real-time, and on-demand labor is the method to unlock that potential within your operation.
In the real world, we’ve seen companies struggle with this because their workforce is the limiting factor to adding more capacity to maintain competitive lead times and not their process or machine capacities. The tough question has been how to add a swing or second shift efficiently to meet this incremental demand that could be temporary or lasting step change.
This incremental approach aligns well with an on-demand labor model because it’s about matching the labor to what you need when you need it. On-demand labor frees the business to pursue new orders while remaining competitive by creating a method to match the labor to the work.
Poka-yoke / built-in quality
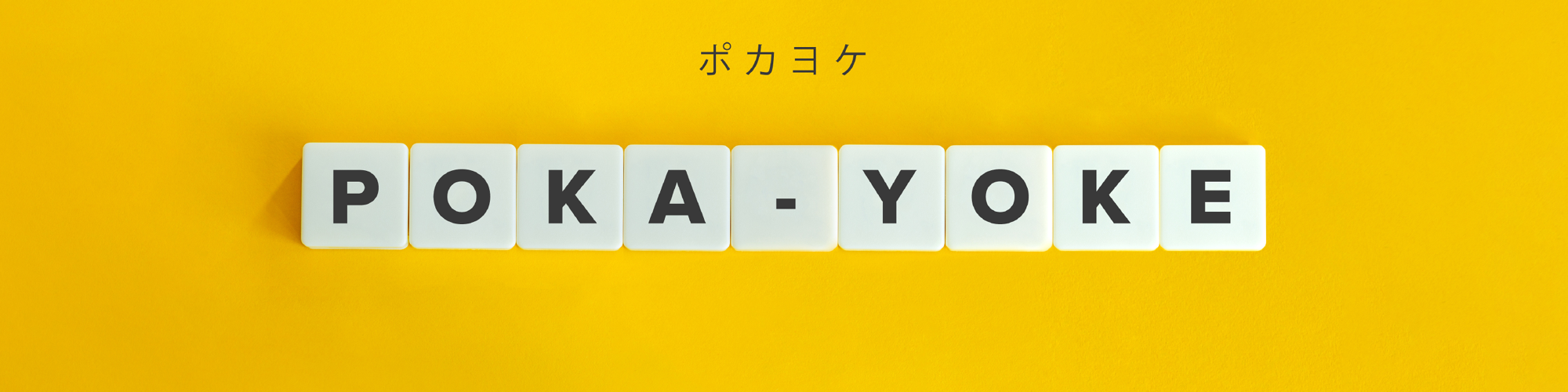
The House of Toyota is built up to deliver the highest quality, lowest cost, and shortest lead time possible. The goal of Lean manufacturing is oriented to delivering customer value with no waste, and this is accomplished by designing the workflow to synchronize people with machine operations to efficiently develop, create, and execute products as demanded by the market.
To accomplish alignment, Lean will have you design your process to add value at each step and setup each step to be error-proof. These two things embed quality in the process, which allows the process to run smoothly at a high yield. Monitoring the process is then the intersection with Industry 4.0.
The technology to manage the sensors and process the information in real-time to detect process performance and to enable machines to intervene or determine if human assistance is required.
Visual Management
This element is where Lean and Industry 4.0 combine to empower the next generation of manufacturing through production and management dashboards. The data that is available via the industrial IoT powers a wide range of analysis to direct on-going maintenance and improve the allocation of people across departments and work areas.
Leading industrial IoT companies are embracing the available data to drive new levels of operational transparency and contract models. The Industry 4.0 data has led the way to drive control limits ever tighter and enable six sigma results for all levels of business sophistication from fully integrated to manual quality assurance production lines.
The accessibility of the data also drives real-time feedback to support friendly competition between production lines or shifts to compare production numbers, yields, or even error rates. This lets management select leading priorities to focus production workers’ attention to push quality rates or production targets.
Heijunka
Now this is where Lean needs to start moving forward from its legacy of great results in driving manufacturing excellence to date. To meet the customer demands of today, the production smoothing of Heijunka is not compatible with meeting customer timelines - deliver my product now or at least respond to the customer business needs.
The impact for businesses is that prioritizing production optimization is no longer an acceptable answer to winning new customers. The pushing out of lead times or sacrificing profitability is not the path forward to victory out there in the evolving operational landscape. Consumer expectations have changed with the digital revolution due to the instant gratification available on the Internet powered by Amazon and Shopify.
The root of this is that businesses must drive to one-piece and execute on demand with the shortest possible lead time to capture as much customer demand as possible.
The evolution of Lean meets on-demand labor
The operational digital revolution is here, and it’s happening at the intersection of Lean and Industry 4.0.
The primary change that must happen in Lean is a move away from production smoothing, which you can only address if you are able to adequately respond to demand as it changes. That is why on-demand labor is an important part of the evolution of Lean — it enables you to match your capacity to demand in real time by finding workers only when you need them. With this ability to flex capacity to match demand in real time, you can keep lead times low while responding to customer requirements such as customization and quick delivery.
At Veryable, we are helping businesses evolve Lean practices through on-demand labor.
For more information, visit our Lean Center of Excellence Homepage or our homepage for Continuous Improvement, Operational Excellence, and Lean Professionals.
Previous Posts
“Weather The Storm” With The Help of Veryable
The Future of Manufacturing and Logistics
Create a free business profile today to explore our platform.
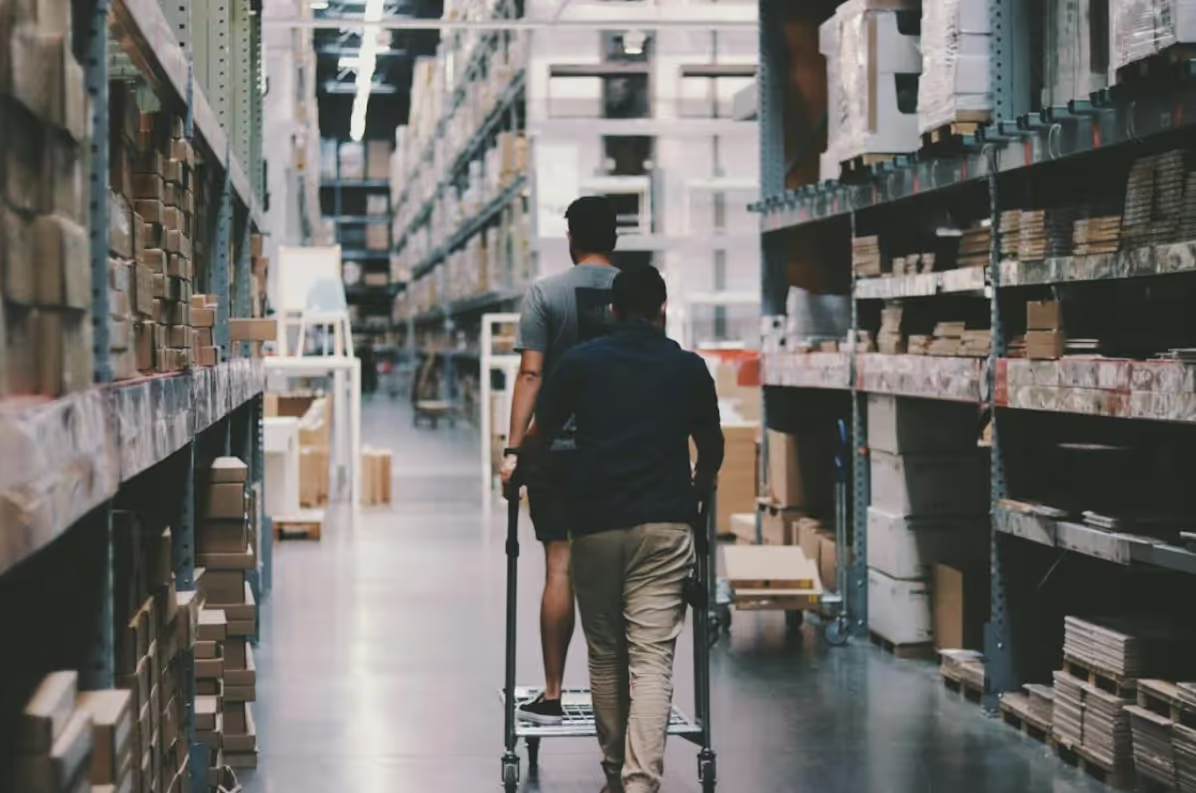