Three Steps to Improving Quality in Manufacturing
Quality is a qualifier for keeping business. The balancing act between cost, speed, and quality isn’t easy. Luckily, you still have control of your situation and can take action to save your operation from quality issues.
At Veryable, we work with companies that use on-demand labor to make operational improvements. This often means making changes that result in more consistent quality.
In this article, you will learn the steps needed to improve your quality metrics, and how on-demand labor can help you do that.
Step 1: Understand your customer returns and defects
The first step is to find out why customers are returning products. To do this, you should assign workers to examining returns for a while to find out what the defects are. Then, you need to figure out how often the defects are happening and search for any commonalities in what might be causing them.
Step 2: Identify the causes of defects in your operation
As you analyze the defects and observe patterns, you should think of what could be causing them to occur. There are a couple questions you can ask yourself that will help find out.
Do the defects tend to coincide with a certain shift/schedule? That would signal that it could be operator error.
Does a certain part of the product almost always seem to be defective? This could signal that you are working with bad materials or that there is a step in your process causing the defect.
Once you have a hunch as to what causes the defects, you will have to physically observe the production process to identify where the defects occur. Monitor the production at each process until you find where the defects are occurring, taking note of where action is needed.
Step 3: Address the root causes of defects in your operation
Once you know where the defects are, you can make the necessary changes to the processes or sourcing causing them. Your goal is to bake quality assurance into your process, so that defects are caught as early as possible.
Implement standardized work
You should find a way to design the work being done so that it leaves less up to discretion. For example, this could mean using a jig for cutting edges that makes it easy to repeatedly produce an even cut. The more standardized you can make the work, the easier it is for workers to be consistent.
Implement a rework line
A common way to address defects is making it standard practice at each workstation that the worker will not accept a defective item to work on. Instead, they will set it aside in a rework bin for pickup by someone else who handles the rework. That way the line workers can keep working, and the defect doesn’t move down the line to end up in the final product. The rework is taken to a separate line, where it is fixed and put back into the main line where appropriate.
Perform routine machine maintenance
You should routinely inspect and perform maintenance on your machines to ensure that the machines don’t start causing defects. Train your operators to do these tasks and make it part of their routine. It’s also important to have a way to keep operators accountable for maintaining their machines, whether that’s tying a metric to it by requiring a certain amount of machine uptime, or enforcing a schedule and checking whether they’ve kept up with it.
How to support your quality improvement initiatives
When you’re making changes to your process, fixing machines, or retraining workers, you might need some extra help to keep up with demand during all of the disruption.
On-demand labor can help you by supporting these transitions, and when you’re done making the necessary improvements to eliminate defects, the people you brought in will still be available in your labor pool.
Now that you have solid processes in place and a lower defect rate, you can start taking on more orders confidently. This creates a need for more workers to increase throughput while keeping cost per unit under control.
Your labor pool will then be a source of people who are already trained on your operations who are available on demand whenever you have a need above your operational baseline.
For more information, visit our Lean Center of Excellence Homepage or our homepage for Continuous Improvement, Operational Excellence, and Lean Professionals.
Previous Posts
Breaking Down Trump’s New Reciprocal Tariffs, The De Minimis Loophole Closure, and The New Tariff On Beer Imports
The Future of Manufacturing and Logistics
Create a free business profile today to explore our platform.
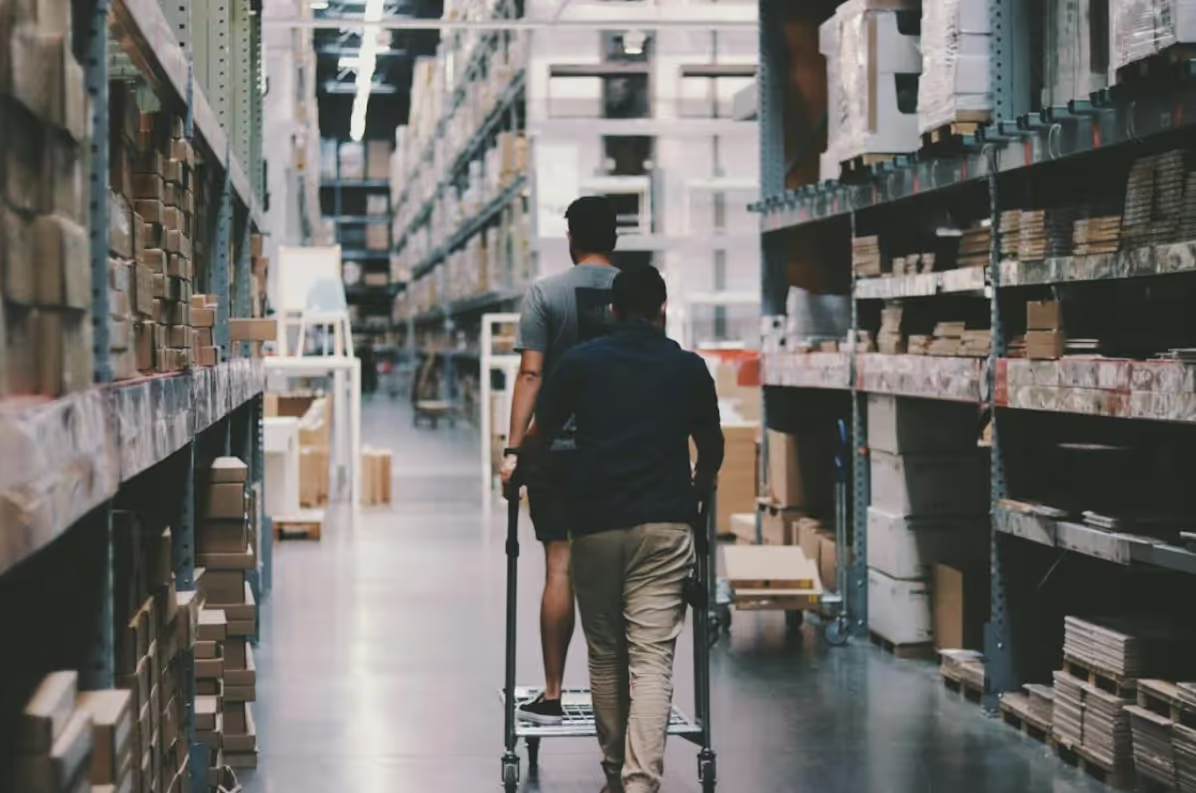