How to Build Quality into Your Process
Having on-demand labor at your fingertips is a great competitive advantage, but many businesses have questions about how bringing in new operators might affect quality.
Quality is a valid concern whether you’re using on-demand labor or not
The distinct advantage of our Veryable platform is “Your Labor Pool”: a group of operators that have worked at your operations before and therefore provide reliable and predictable extra capacity. This goes a long way toward addressing those concerns, but whether you are using a conventional staffing model or you’re scaling labor to match actual demand with a Veryable labor pool, quality remains a priority for any business. You must realize that defects stemming from human error create a problem to be addressed at the root. If your quality depends on the presence of experienced workers, you should be worried! Why? Because your quality is not assured. It’s a fact that to err is human, and therefore you need a system that builds quality into your processes if you don’t want the errors that will happen to cause defective products.
The Japanese way of looking at quality is that the only acceptable outcome is zero defect. A lot of people will read this and immediately dismiss it as totally unrealistic. In fact, the Japanese are very practical and so is this approach. It’s not really about achieving true zero defect status, because after all the world is very complex and always changing (even the best companies can maintain “zero internal defects” for at most a few months, but the key is that by constantly pursuing this goal they achieve amazing levels of quality). If you set your expectations low, you’ll get correspondingly low success. By adopting the zero-defect mindset, you will not waste time trying to reduce defects. You will instead concentrate on ways to eliminate defects, focusing on the process rather than on the workers.
Dr. Edwards W. Deming said it first: 6% of the problems are caused by the workers, 94% are caused by the system. Knowing where to focus is key to success.
If there’s only one book you must read about built-in quality, read Shingo’s Poka Yoke, A Revolution in Manufacturing. Shingo is an impressive industrial engineer who was the first to introduce to western audiences some of the most useful tools in the lean toolbox: SMED (rapid changeovers) and Poka Yoke. There are some other books on poka yoke that will mainly provide dozens of examples and open your mind to how creative operators are. Because, yes, the best poka yoke devices are created by the people who work in the process every day.
So what’s a poka yoke?
A poka yoke (po-kah yo-kay) is a device that:
- Is cheap
- Automatically checks every part to detect if a defect or error of a certain type is present
- Doesn’t require any human help (i.e. it consumes no labor)
- Does something when the defect or error is present.
That’s it! To further understand how poka yokes are used, you need to know about the process of building quality into the process. If you’ve heard about jidoka and wonder what it’s about, that process is a good description.
We’ll do another blog on poka yoke later, given the complexity of the subject, but a good place to start is here.
The process of built-in quality
The process starts by understanding your quality landscape: where are your most hurtful quality problems? Analyze customer complaints to get the picture from an external perspective, and inspection data to get it from the internal perspective. Start from the general and dive into the specific. The Pareto analysis is a simple but powerful tool to avoid getting overwhelmed by the sheer mass of data. A Pareto diagram ranks quality problems caused by sources of defects. Initially, you may want to know which products have the highest quality costs. Typically, you’ll select the roughly 20% that have 80% of the costs. Depending on the resources at your disposal, you may proceed one product/product family at a time, starting with the one associated with the biggest quality costs, or you may be able to work on more simultaneously. Your level 2 Pareto may rank work centers and your level 3 may finally rank and select defect types. The important thing is to keep your focus on what you can handle until you have achieved the prevention poka yoke stage. In effect, stay on it until you’ve practically eliminated the defect(s) you’re working on. Then, go back to your Paretos and pick the next target.
So, let’s say you’ve identified part mix-up as your target. For example, maybe your biggest problem is that some parts are assembled using a wrong component, leading to failure. In some cases, like this mix-up example, you may find a poka yoke fairly quickly because mixed parts are typically due to a lack of 5S standards. For example, if the various components are always within reach of the assembler, it is almost inevitable that at some point the person will reach for the wrong part, especially if they’re visually hard to tell apart. A common poka yoke in this case is to make access to the wrong part impossible. For example, when producing for a given product, only the components listed on the Bill Of Materials should be accessible. This could be achieved with a physical barrier (remove the unused bins or cover them) or an electronic barrier (a sensor detects the operator’s hand reaching into the wrong bin and sounds an alarm until the right component is picked). Of course, it could be more complicated than that. Maybe the mixed parts occur upstream, during handling or even at the supplier’s facility. Another poka yoke might therefore be to source components that cannot be mistakenly picked (say, a different color) or assembled (a different shape). But, because this requires changing the design, it should be attempted only if the simpler solution fails to eliminate the problem. Having the zero-defect mindset would in fact tell you that changing the design is wrong, because it’s not addressing the root cause, at the actual point of occurrence of the mix-up.
Then you have more complex problems. If the cause of the defect is unknown, or occurs so rarely that you don’t really understand how it happens, a simple detection poka yoke would be your first stage. This poka yoke doesn’t prevent the defect, it simply exists to automatically detect it, and then to stop the process or machine and give out an alarm so that investigation of the conditions causing the defect can be initiated immediately. Then, having discovered the root cause, a prevention poka yoke can be devised that will take care of the problem once and for all.
Having been involved in dozens of poka yoke efforts over a period of 15+ years, here are a few things I’ve learned and want to share with you:
- You must observe what really happens. Discard anything that is based on assumptions until you can observe it. This is why you may need to use a detection poka yoke initially.
- Understand the real point of occurrence, and always work there, not downstream (even if downstream was where you started the effort).
- The best ideas are more likely to come from operators than from engineers. The operators have an intimate knowledge of the process and know its realities better than anyone. Engineers tend to go for solutions that involve technology and are therefore more expensive and more fragile.
- Don’t rush it. It’s unlikely that you can get anything good in one day. Give people time to ruminate on the problem.
- Don’t rush to implement the first idea that is accepted by the team. The more ideas you have, the better the end result.
- Every idea can typically be cheaply tested. Make a cardboard model before asking your maintenance team to fabricate a device. This may make you see something new and save you a lot of money. One of the best piece of advice on this subject came from a Toyota coach, Mike Takahashi: “Why weld when you can bolt? Why bolt when you can tape? Why tape when you can hold with your hands?”
- Give everyone an actual good part and one that has the defect you’re trying to error-proof. Then make a list of every single difference they can identify between the two. Do they have a different weight? Dimensions? Center of mass? Conductivity? This is where having an engineer is going to be helpful. For every differentiating characteristic you find, there is at least one new way to create a poka yoke.
Pragmatism combined with idealism wins the day
In the jidoka approach, you start by putting in place a way to understand when something abnormal happens. This is typically a detection poka yoke coupled with a quick reaction team that immediately investigates until they’ve figured out the root cause. Sometimes, instead of a poka yoke, the alarm is sounded by an operator pulling on a cord or pushing a button (I don’t recommend this approach as there is just too much production pressure in most places to make this a reliable detection mechanism, but it might be something you do for a limited time and with clear support from above). Either way, once you’ve understood the root cause, you can move to the prevention poka yoke stage, and eliminate the defect.
The next stage is, once you’ve proven to yourself that the quality is built-in and that the defect is truly eliminated, to remove the corresponding inspection. Inspections don’t just cost money—they are sometimes wrong, and they always lengthen and complexify the process.
Now, start again, picking your next priority defect. As you can see, it’s very pragmatic. It uses the know-how of the people who work on the shop floor. But it’s also based on idealism: you just don’t accept anything other than total elimination of the defect. If you’re not into long Six Sigma projects or expensive engineering fixes that generate unwanted side-effects, try this approach. But be aware, like all lean solutions, it requires a mindset of respect for the expertise of your operators.
For more information, visit our Lean Center of Excellence Homepage or our homepage for Continuous Improvement, Operational Excellence, and Lean Professionals.
Previous Posts
Make The Most of The 100 Days of Summer With Veryable
The Future of Manufacturing and Logistics
Create a free business profile today to explore our platform.
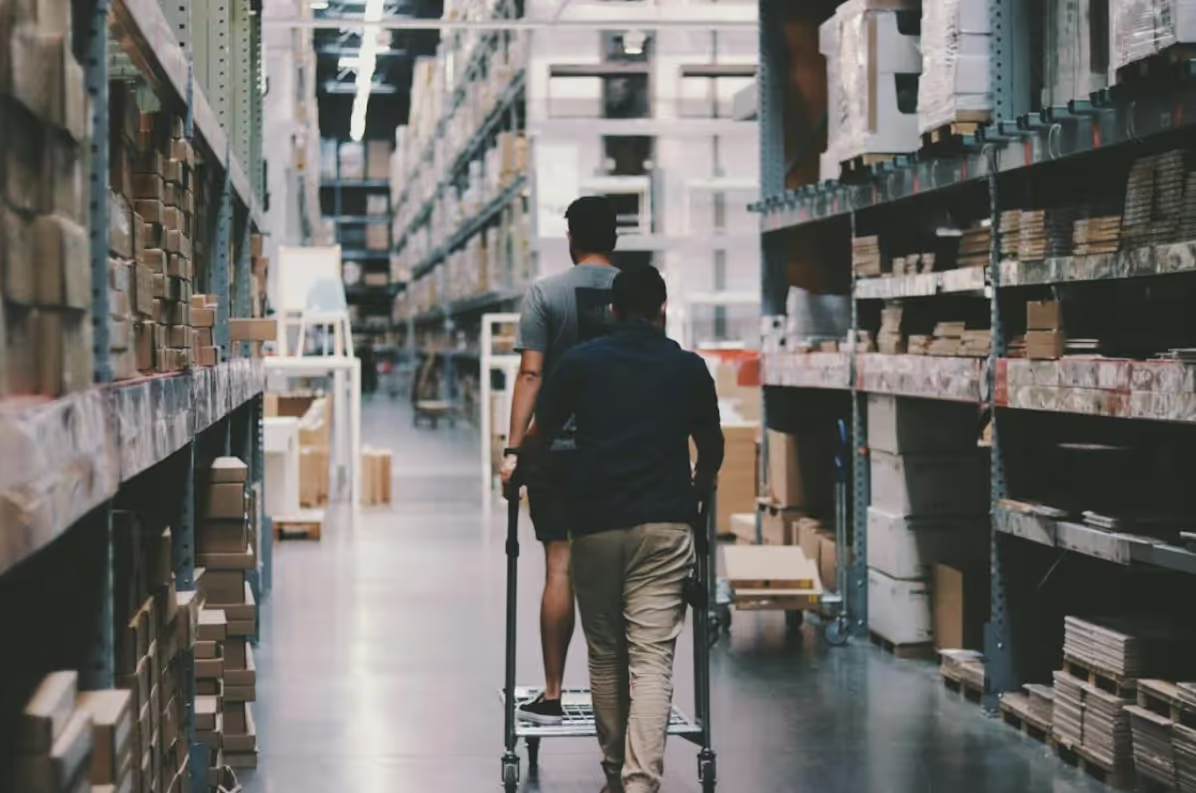