Effectiveness and Efficiency in Operations
The first formal program with the title “Engineering Management” originated at the University of Missouri-Rolla (now Missouri S&T) sometime in the 1960s. The University of Missouri describes Engineering Management as the art and science of planning, organizing, allocating resources, and directing and controlling engineering activities. Many other colleges have been focused on the same foundational concepts of Engineering Management for a long time. The principles have been practiced in manufacturing and even military operations for hundreds, if not thousands, of years.
Effectiveness vs. Efficiency
In his book Management: Tasks, Responsibilities, Practices, Peter Drucker states “effectiveness is the foundation of success - efficiency is a minimum condition for survival after success has been achieved. Efficiency is concerned with doing things right. Effectiveness is doing the right things.” Efficiency and Effectiveness are part of the basic pillars of Engineering Management. The principles can be applied to most situations involving the pursuit of goals and the use/preservation of resources.
Outside of educational theory, how can manufacturing and distribution business leaders use effectiveness and efficiency to win in their respective markets?
- Effectiveness = Delight the customer (give them what they want when they want it)
- Efficiency = Achieve the effectiveness described above with little to no wasted resources (optimize inputs versus outputs, aka productivity)
When the Veryable team initially meets with a business, it’s common for the evaluation to first focus on Effectiveness.
Increasing Effectiveness typically represents the largest source of value, since it will often lead to revenue growth for the business and has significant upside. Due to labor and supply chain challenges, businesses have struggled with the service levels of their current contracts for the last few years, which has limited their ability to grow and capture additional market share when the market is favorable.
After a business has service levels under control and starts seeing revenue growth potential forming, the focus typically shifts to achieving maximum Efficiency.
In most cases, there is an opportunity to drive out labor wastes such as overstaffing, overtime, and employee turnover costs. If a business can perfectly match their labor inputs to demand on every single day, their model can be optimized. Having a completely flexible labor asset enables a Just-In-Time workforce model which supports Just-in-Time production (Lean) and healthy inventory levels.
Real World Example
Customized Distribution Services is a great example of a company that found a way to win using the Veryable strategy. Effectiveness was the first order of businesses for CDS. They needed to get service levels under control by rapidly deploying labor resources to process their backlog of trailer unloading. Along the way, they deployed 30,000+ labor hours and built a 100+ person Labor Pool of skilled and highly rated workers. As service levels improved, the focus gradually shifted more to Efficiency, which involved deploying their Labor Pool to quickly react and match labor inputs to fluctuating daily demands. Veryable has a Workforce Management tool that can be used to help organize this process and make the “perfect” scheduling of labor easier. Read the full case study here.
Veryable is a new operational strategy focused on helping businesses achieve higher levels of Effectiveness and Efficiency within their operations. This requires thinking outside of the box to gain a competitive advantage. Please contact the Veryable Team if you’d like to further evaluate if the model is right for your business.
Previous Posts
Trump 2.0 Week 13 Recap: Discussing Ongoing Negotiations With Key Trade Partners, A Potential Deal With China On The Horizon, and More
The Future of Manufacturing and Logistics
Create a free business profile today to explore our platform.
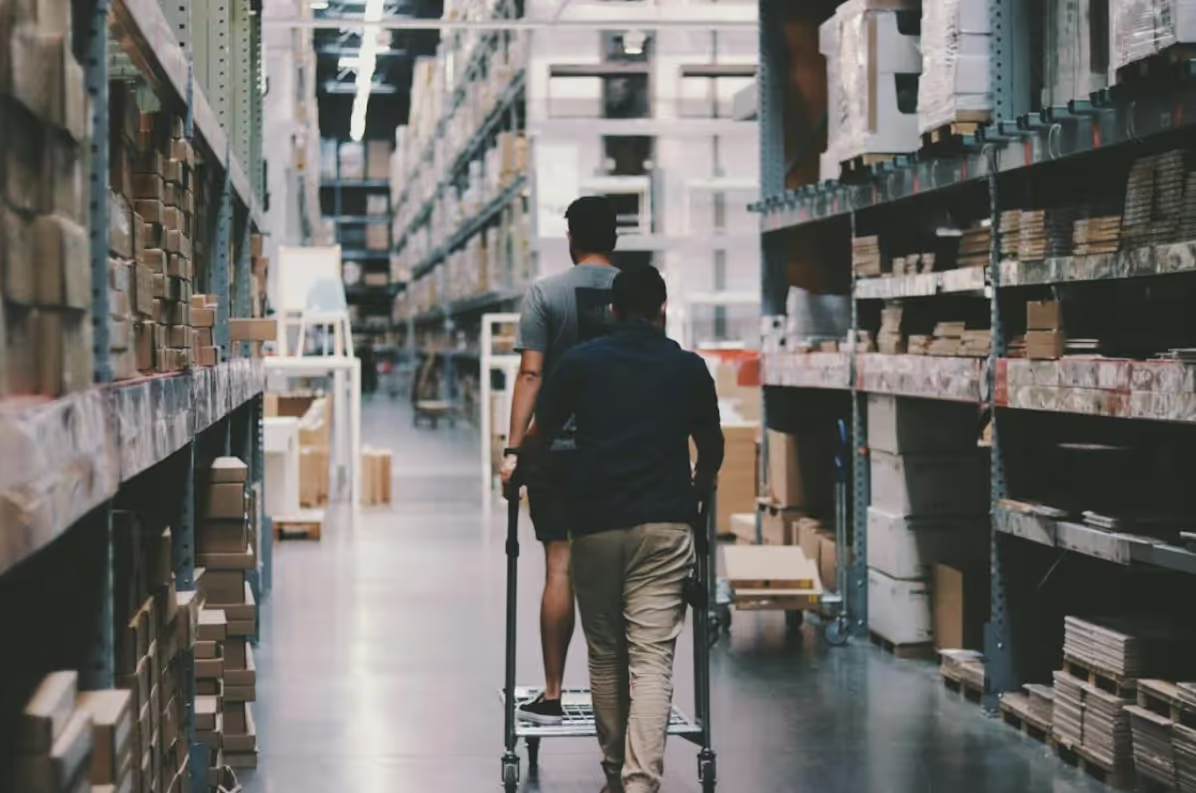