Don’t Ditch the Lean Supply Chain
In recent months, some supply chain thinkers have all but blamed lean inventory levels for the challenges and delays the world has faced in 2020 and 2021. However, the lean supply chain is just one wind in the storm that swept the supply chain off track this year. Let’s not forget the outsourcing, offshoring, bullwhip effect, unpredictability of human behavior in a crisis, and political posturing that have contributed to the supply chain issues of the past year and a half.
In this article, we will outline the main arguments against the lean supply chain, respond to each in turn, and offer our suggestion on the way forward in revitalizing US manufacturing.
The argument against the lean supply chain
The primary argument against maintaining a lean supply chain in the future is that low inventory levels do not provide enough of a buffer for when unplanned events (like a global pandemic) cause demand to change drastically or disrupt supply in some way. Then there is the argument applied up and down the chain. It is commonly levied against lean manufacturing that it simply moves inventory up the supply chain. This is because a producer practicing lean will want to be able to pull raw materials as quickly as possible. The argument continues that the lean supply chain is incentivizing upstream suppliers to compete by having inventory on hand to ship ASAP.
The first argument claims that by not having sufficient inventory to respond to a crisis, the lean supply chain has failed. Supporters of this argument would say that instead, companies should aim to have enough stock to respond to unpredictable demand for an unpredictable amount of goods, all of which could be needed at any moment.
The gist of the second argument, in which the lean supply chain is accused of shifting inventory upstream, seems to be that more inventory at every step of the supply chain would be better. To support this claim, one would have to calculate the total benefit of producing and maintaining this crisis stock at all times and determine if that would outweigh the costs to the business and its customers over the long term.
The rebuttal for the lean supply chain
We will go point by point here and address the argument that maintaining lean levels of inventory throughout the supply chain is a flawed approach, before moving onto the broader context surrounding the supply chain issues of 2020 and 2021 that prompted this reflection in the first place.
One thing worth clarifying before addressing these points is that the goal of a lean supply chain is to optimize inventory, not to eliminate it, as LeanCor Supply Chain Group CEO Robert Martichenko outlines in depth in his two-part article on the post-COVID supply chain. We will cover many of the same points he made here, although we have additional points to make that are not specific to COVID but rather focus on the reshoring trend currently gaining momentum.
Lean inventories are not causing disruption, and more inventory won’t fix it
The first point we must address is the idea that maintaining more inventory is the answer to the supply chain disruptions we currently face. This is difficult to prove and fallaciously substitutes traditional wisdom for a nuanced exploration of possible causes for the problems we face.
For this claim to be true, maintaining inventory would have to be more cost effective than maintaining a lean supply chain. Consider first that excess inventory wastes space, labor, materials, and production time. Next, consider that there is no practical way to anticipate how much of a stock should be kept in case of a crisis. And there is no financial incentive for a company to maintain this.
This claim also fails to take into account the other factors causing the supply chain disruption that prompted people to reconsider Lean manufacturing in the first place. It is important to remember that peoples’ behavior is often unpredictable in a crisis, meaning demand signals can spike and crash in unexpected ways.
This, combined with the bullwhip effect, will create problems no matter how much inventory companies keep on hand. Another factor to consider is the far-flung distributed nature of the global supply chain, and how the sharp increase in goods overwhelmed the supply chain infrastructure.
It’s also important to take into account the effect that offshoring has had on the supply chain separately from Lean initiatives. Lean improvements do not require offshoring. In fact, reshoring would be more compatible with a lean supply chain approach, because it would be closer to actual just-in-time production by removing the transit time required to move goods from overseas.
The lean supply chain exposes inefficiencies in adjacent companies
Second is the idea that maintaining lower inventory levels pushes stock up the supply chain. While this might initially be true, if the suppliers adopt Lean manufacturing principles as well, then it would eliminate this problem. Members of the supply chain practicing Lean principles expose inefficiencies in their suppliers when their suppliers use other techniques (such as batching) as a bandaid to hide their true lead times.
If the suppliers instead adopted the Lean approach, it might result in longer lead times for the end customer, but would overall create less waste and reduce the total cost of the final product. The outcome would lead to the supplier doing more with less, operating more efficiently, and leveraging all its on-hand inventory.
The underlying assumption of the “more stock = better” argument is essentially that faster is always better, and anything done in service of speed is the right decision. While this is comfortable, it is costly and ignores several externalities and the ugly truth that producing something will always take time. There is a limit to how efficient a supply chain can be. Outside of a fully localized, near-fully autonomous production process, the bogeyman of the two-day delivery promise is upheld by overproduction and waste, and should not be the ultimate goal of every manufacturer and distributor.
As we move toward full transparency into the supply chain, which would reveal the actual minimum lead time of an item from materials to shelves, customers might soon realize that being able to buy anything, anytime and have it instantly is an unsustainable illusion. Routine overproduction is not a good answer. An example of this would be the massive amounts of wasted crops each year and the fact that excess inventory takes up valuable space and cuts into margins, whereas companies with more agile operations routinely outperform those carrying more inventory.
The new way forward
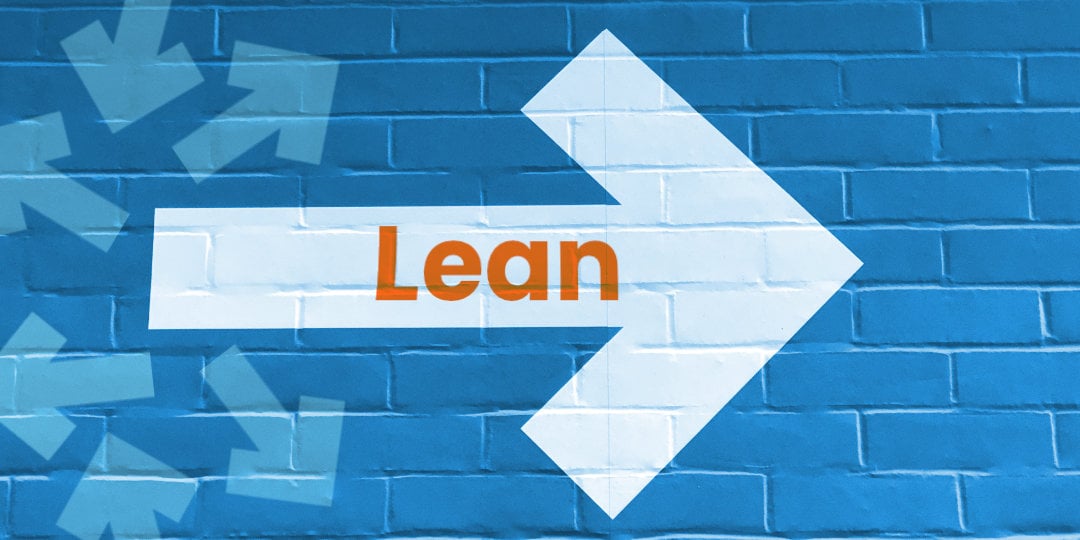
Lean manufacturing and its application up the supply chain to form a lean supply chain is not dead yet. While there are cons to this system, the alternative would create more waste overall and only hides inefficiencies.
As reshoring gains momentum, the productive sector of the economy will return to a similar working environment to where Lean was originally developed. In Japan during the time when Lean was developed, there wasn’t the cash or the space for huge factories. Also, the relatively small size of the island of Japan meant that nodes of the supply chain were closer together and shipping times were shorter, so Lean methodology would work all the way up the supply chain.
As US companies reshore and attempt to avoid high upfront costs while bringing parts of the supply chain closer together, the US might find even more utility in the lean supply chain. This would create a common point of interest for the US, Canada, and Mexico to cooperate and accelerate reshoring production to North America.
The future of manufacturing will be localized, asset-light, and responsive to demand. This cannot happen with legacy approaches where excess is produced and then companies attempt to generate enough demand to get rid of their costly waste product.
To reach new heights in digital manufacturing, a new way forward would include the Lean approach of maintaining less cycle inventory, while breaking slightly from the Lean methodology to produce interchangeable parts that might be used for agile production of customized products at the local level.
Companies need to embrace flexibility and respond to demand signals as they occur. Martichenko says that “this competency needs to be considered a function of national security,” and Veryable’s CEO Mike Kinder has called out that it is time to accelerate the trend of reshoring as our duty.
The first, and most crucial step in this process, is getting the labor part of the equation right. Agile response to demand will require flexibility, and on-demand labor is the solution manufacturers need to meet the new challenges we will face. Learn how this benefits your business in our blog about how on-demand labor enables instant flexible capacity.
For more information, visit our Lean Center of Excellence Homepage or our homepage for Continuous Improvement, Operational Excellence, and Lean Professionals.
Previous Posts
Trump 2.0 Week 25 In Review: July Deadline Extended, 50% Copper Tariff Announced, and Higher Tariffs for Canada, Brazil, and BRICS
The Future of Manufacturing and Logistics
Create a free business profile today to explore our platform.
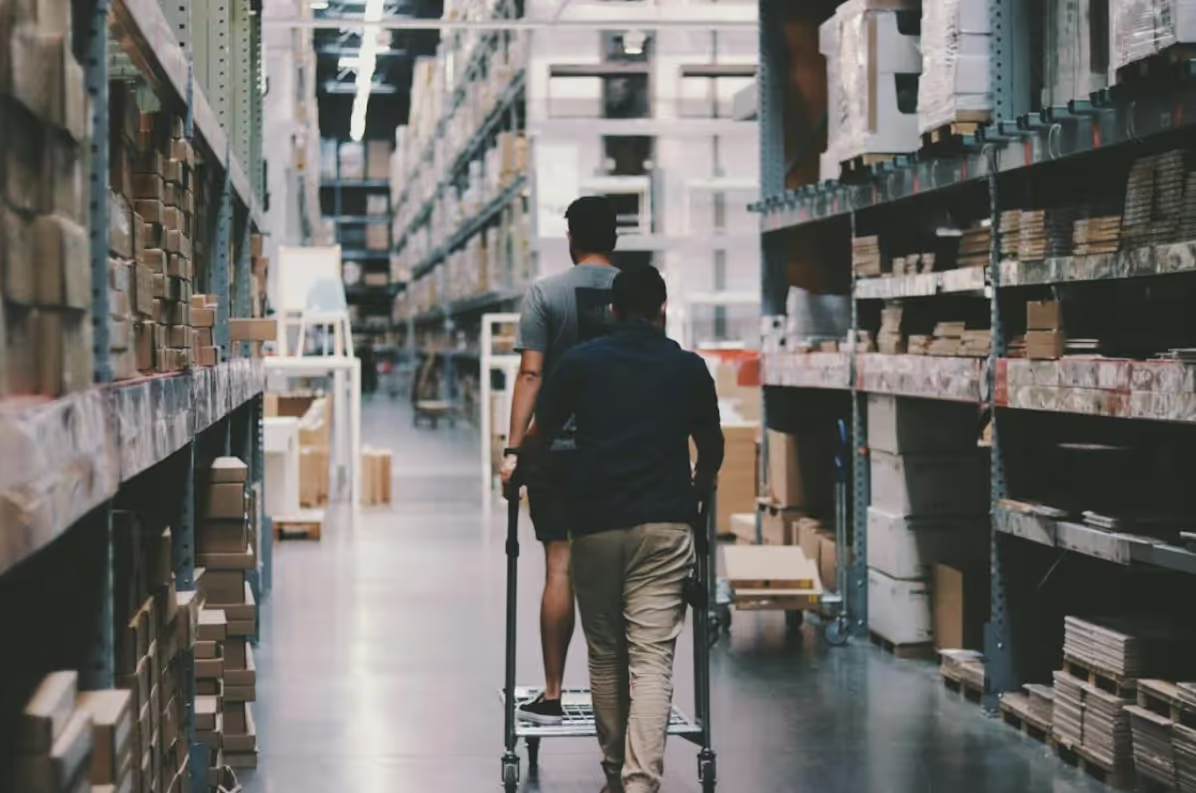