Capacity Planning for Manufacturing: Taking An Agile Approach
When you’re planning for the year ahead, trying to match up your labor to an unpredictable demand cycle creates frustration that is often palpable. Maybe you have lofty goals to meet, but have limited resources. You want to capture all of the demand you can without over-hiring. But how do you do that without perfectly predicting the future?
Veryable believes in turning the old way of capacity planning on its head. We acknowledge that there might be many other solutions, but we are certainly biased towards on-demand labor as a solution to this problem. That’s because with our on-demand labor marketplace, we’ve helped companies break free from their labor constraints, respond to demand just in time, increase their profits, and shrink lead times.
In this article, you’ll learn how you can predictably meet your demand without hiring more workers than you need. You’ll learn the steps you can take to adopt a more agile capacity planning strategy.
How to adopt agile capacity planning in a manufacturing facility
- Plan headcount based on minimum forecast demand
- Stop filling turnover with full-time employees
- Plan the labor to the work
- Respond to demand just in time
Step 1: Plan headcount based on your minimum forecast demand
To avoid paying people to stand around, forecast your labor needs based on your minimum demand instead of your average demand. The minimum demand you fill on any given day of the year should be the basis of your headcount planning. Setting this minimum level of output as the basis for your headcount will give you a baseline to aim for while avoiding overstaffing.
Now, we know that this is a dramatic change to the typical capacity planning formula based on the average demand. But in order to achieve truly lean manufacturing, the ability to respond just in time is key.
If you face fluctuating demand but use an average demand calculation to plan capacity, you’ve likely seen the dramatic effects of being overstaffed or understaffed on your bottom line. You will either have to send people home when order volume is low or pay overtime to keep up with demand.
Instead, you should plan to meet the minimum demand with the minimum number of full-time employees. Part-time employees or flexible solutions like on-demand labor allow you to respond as demand rises. This will save you money and empower you to meet demand without hiring full-time workers that get paid during stretches of time when they don’t have work to do.
Step 2: Stop filling turnover with full-time employees
The next step is to stop filling positions as your employees leave. The costs in both time and money that come from addressing turnover are a tremendous drain on your business.
I’d guess your turnover probably looks something like this:
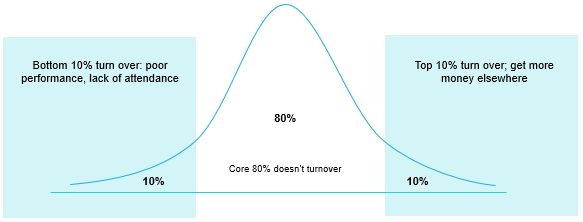
Instead of chasing your own tail by backfilling turnover, stop chasing the 20% of workers who leave. According to a SHRM survey, the average cost to hire one employee today is $4,479 (adjusted for inflation).
Instead, invest in the core 80% of your workers who stick around. By halting the revolving door of turnover in your business, you will save money and free up time to focus on workforce training, development, and incentives. When demand rises above what your core 80% can handle, that’s when you can utilize an on-demand labor solution to match your labor with your demand.
Step 3: Plan your labor to match demand
Planning the labor to fit the work is a significant shift in mindset from the typical capacity planning method. Typically, businesses have planned the work they can do to fit the available labor.
In the past, you might have asked yourself something like, “I’ve got 30 employees coming in today, 20 coming in tomorrow, and 25 coming in the next day. However, I only have work for 20 employees each day. How can I split up my demand these upcoming days to be as efficient as possible?”
Then, you would artificially shift demand to smooth out your production over the course of the week, and end up running less efficiently. Lead times get extended one day and the next day you're asking people if they want time off because you have no work for them.
This line of reasoning is how businesses end up paying employees they don’t have work for. Not only does efficiency drop, but employees lose patience when there isn’t much work available. They might be pushed to meet quotas they can’t maintain because the work just isn’t there. It’s also likely they will be asked to work overtime when order volume picks up. You can easily see how these factors inevitably lead to employee turnover.
To solve the capacity planning problem, a better question to ask is this: “I’ve got to get 200 units out tomorrow, how many workers do I need to accomplish this most efficiently?”
This is what we would call planning the labor to the work. This simplifies managing your headcount by removing the possibility of having to ramp down. Assuming you’ve already built your full-time labor for the minimum demand, you would know you’ll only ever need to ramp up your headcount to produce the 200 units.
When you plan the labor to the work, you shift into thinking about output per worker and solving for how much labor you need instead of how to spread out the work. This leads to tightening your processes and tracking how much each worker can do. What you measure can be improved, so naturally this will lead to improvements in your operational efficiency.
Planning the labor to the work is better than accepting the average output as a given and nitpicking an inefficient plant throughout the year for minimal improvements. When you embrace and respond to the unpredictable nature of demand instead of relying on guesswork, you can focus your efforts on what matters. You can stop wasting time continually tweaking a capacity plan that is inefficient by design.
Do not concede to planning by averages. Instead, make your business agile in responding to demand. Avoid shifting the demand around artificially to fit your labor constraints. Instead address the labor variable, which is within your control, unlike demand.
Step 4: Respond to demand just in time
There is tremendous potential value gained by conducting capacity planning with a focus on matching the labor to the work. When you no longer have to rely on guesswork, you save money on faulty predictions. Instead, you can bring workers in to work when you realize the work is there.
By responding to demand just in time, you are only paying for the work you need. This is the most efficient way to match labor to demand.
To do this, you will need a way to quickly find workers. There are multiple options for this, including temp staffing agencies and on-demand labor. With the many differences between these solutions, you should compare traditional staffing to on-demand labor so you know which solution works for you.
You’re ready to capacity plan a more agile way
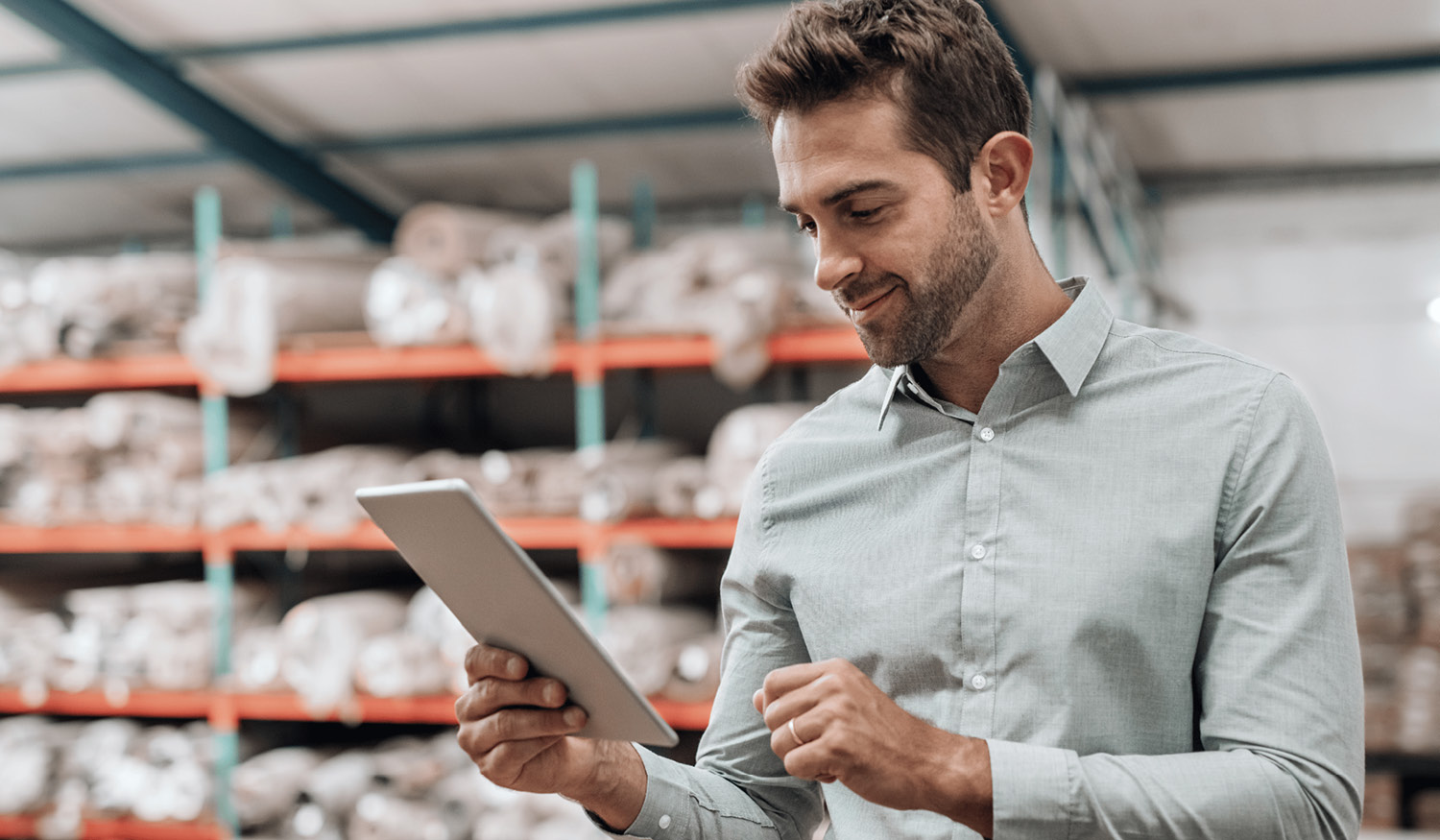
The best time to start the transition to this approach is now, and it begins with stopping the backfill of turnover. Instead, these positions should be filled only when the work is there.
Prepare to increase headcount just in time to respond to your demand by reading about how on-demand labor is a great solution for finding workers fast and can be a tool for infinitely flexible capacity.
To learn more about how the Veryable solution can help you take a more agile approach to capacity planning, check out our most recent article: Taking Control of Your Daily Capacity Challenges
Previous Posts
Trump 2.0 Week 13 Recap: Discussing Ongoing Negotiations With Key Trade Partners, A Potential Deal With China On The Horizon, and More
The Future of Manufacturing and Logistics
Create a free business profile today to explore our platform.
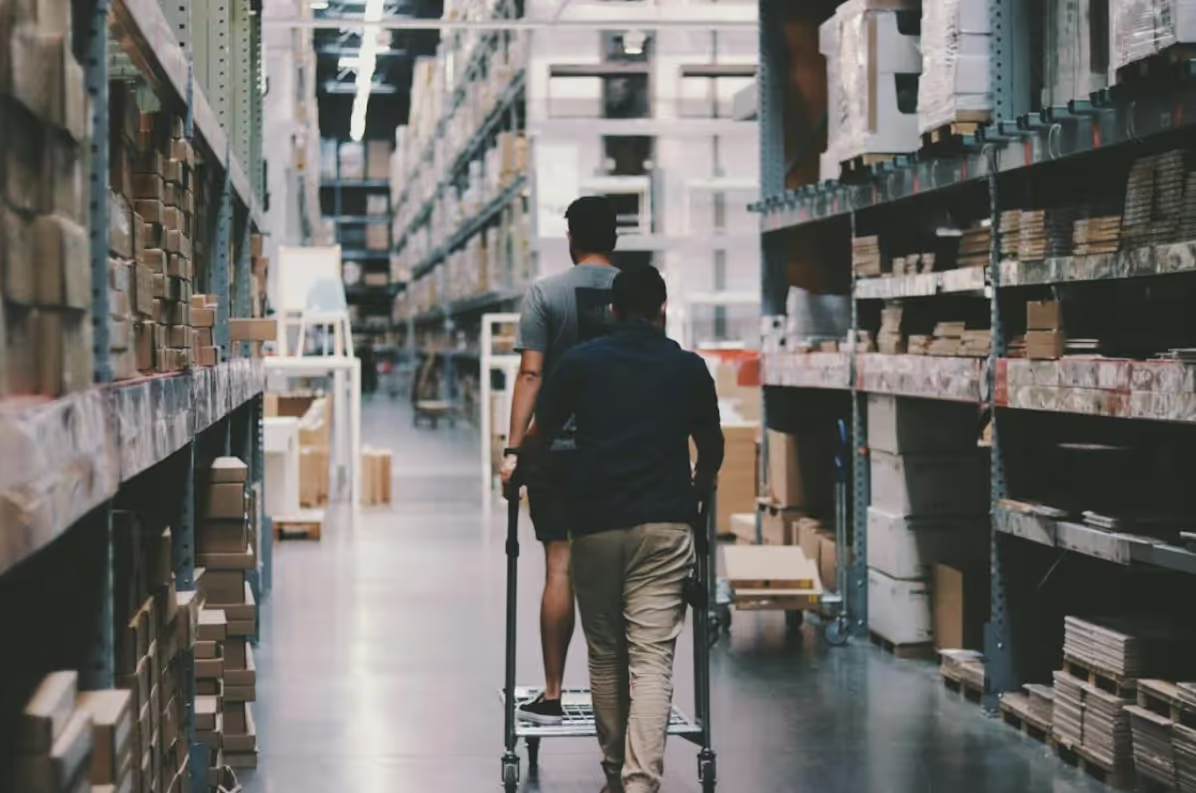